Grinding of the inner diameter of tubes
Pro perfektní odstranění vnitřních povrchových vad
Description of the device
Grinders for internal pipe diameters are used for:
- to remove surface defects after rolling and
- for deburring after rolling
- to improve the appearance of the inner surface of the tubes
The tube rotates by means of driven radial lunettes and a guide rod with a shaft and stone grinding wheels at the end of the rod is inserted into the tube in a uniform manner. The pressure and feed of the discs on the pipe surface is controlled automatically from the control panel. The resulting abrasion material is carried away from the pipe through the filtration by a fan.
Technical parameters of the machine
Inner diameter of pipes: | 180 – 600 mm |
Length of pipes for single sided grinding: | up to 8 000 mm |
Max. Max. length of pipes when grinding from both sides: | up to 16 000 mm |
Material removal in one cycle of passage: | up to 0,20 mm |
Repeated grinding cycles on a defined section in order to grind: | up to 1,6 Ra |
Automatic mode allows for: |
|
Abrasion extraction: | By connecting an elastic abrasion resistant hose to the end of the pipe using a replaceable conical head. |
Other equipment of the machine.
- Input tray tables with automatic loaders The loaders move the pipe from the table to the radial rollers to the grinding axis The loaders move the pipe from the table to the radial rollers to the grinding axis.
- Loaders for moving the pipe from the rollers to the side table.
- Filtration device with a fan for suction of particles after grinding. Filtration device can be set up in the production hall.
- Semi automatic insertion of the suction hose to the suction end of the pipe.
- For long pipes over 8 m, the alignment of two mirror grinders for grinding the pipe from both ends is necessary. This solution increases productivity of the production of long pipes and saves handling times incl rotation of the pipes by 180 degrees.
- Manual ultrasound tube wall thickness measurement.
- Extended visualization with an emphasis on intuitive and detailed display of operating states and the place of failure of the grinder.
- Extended service with the possibility of displaying guides, service manuals and other necessary documentation on HMI machines in order to minimize service times.
- Collection of agreed production parameters with automatic saving, display and data export.
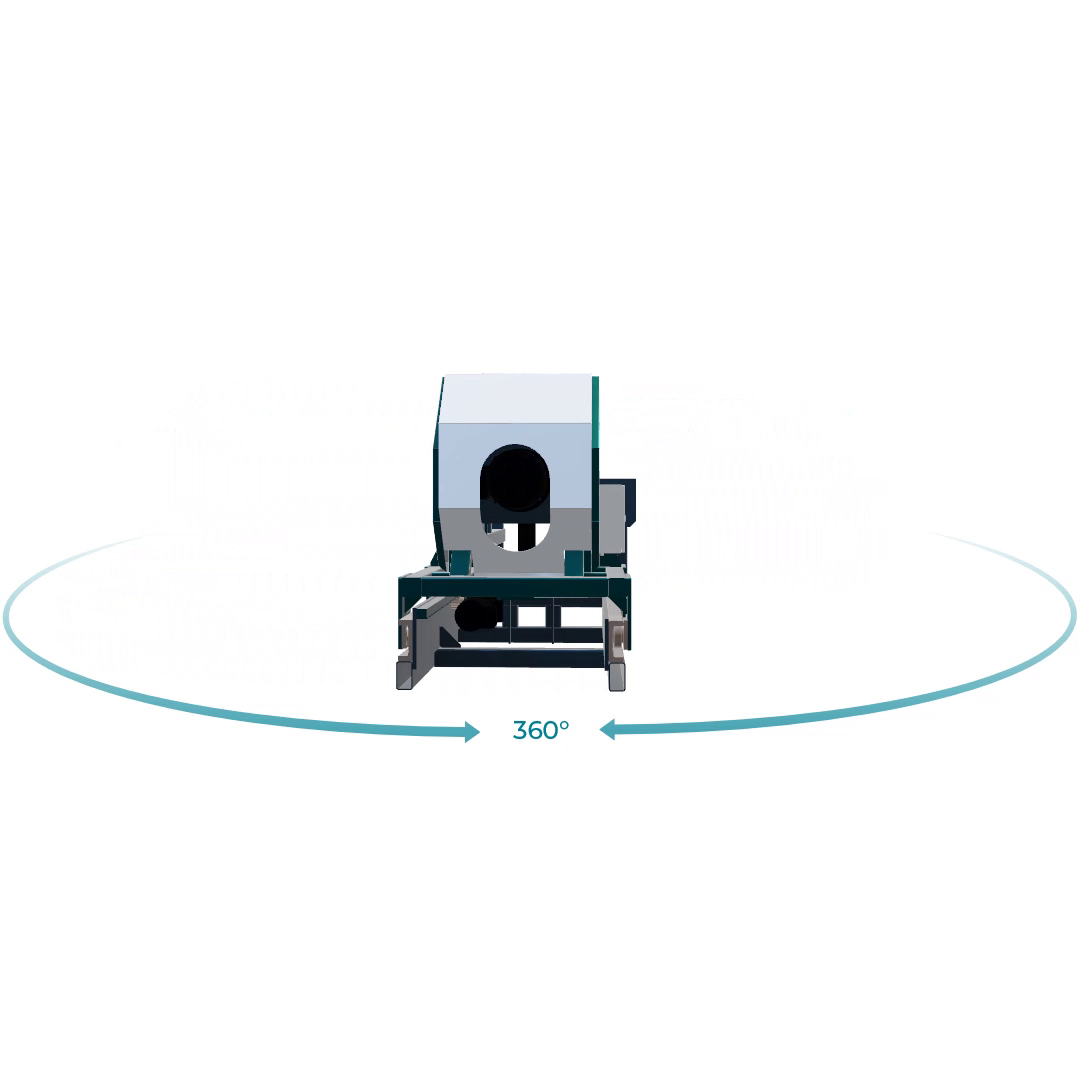
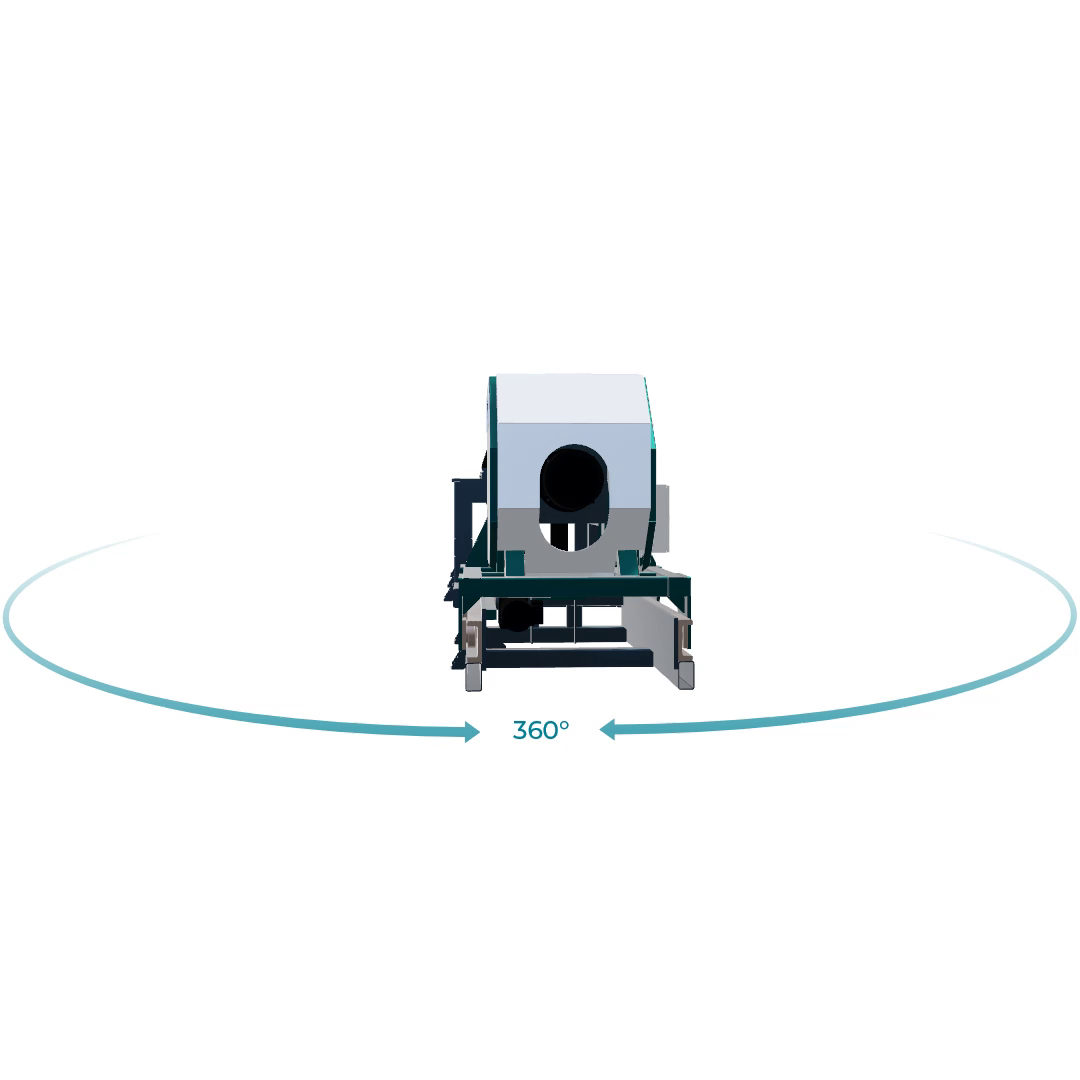
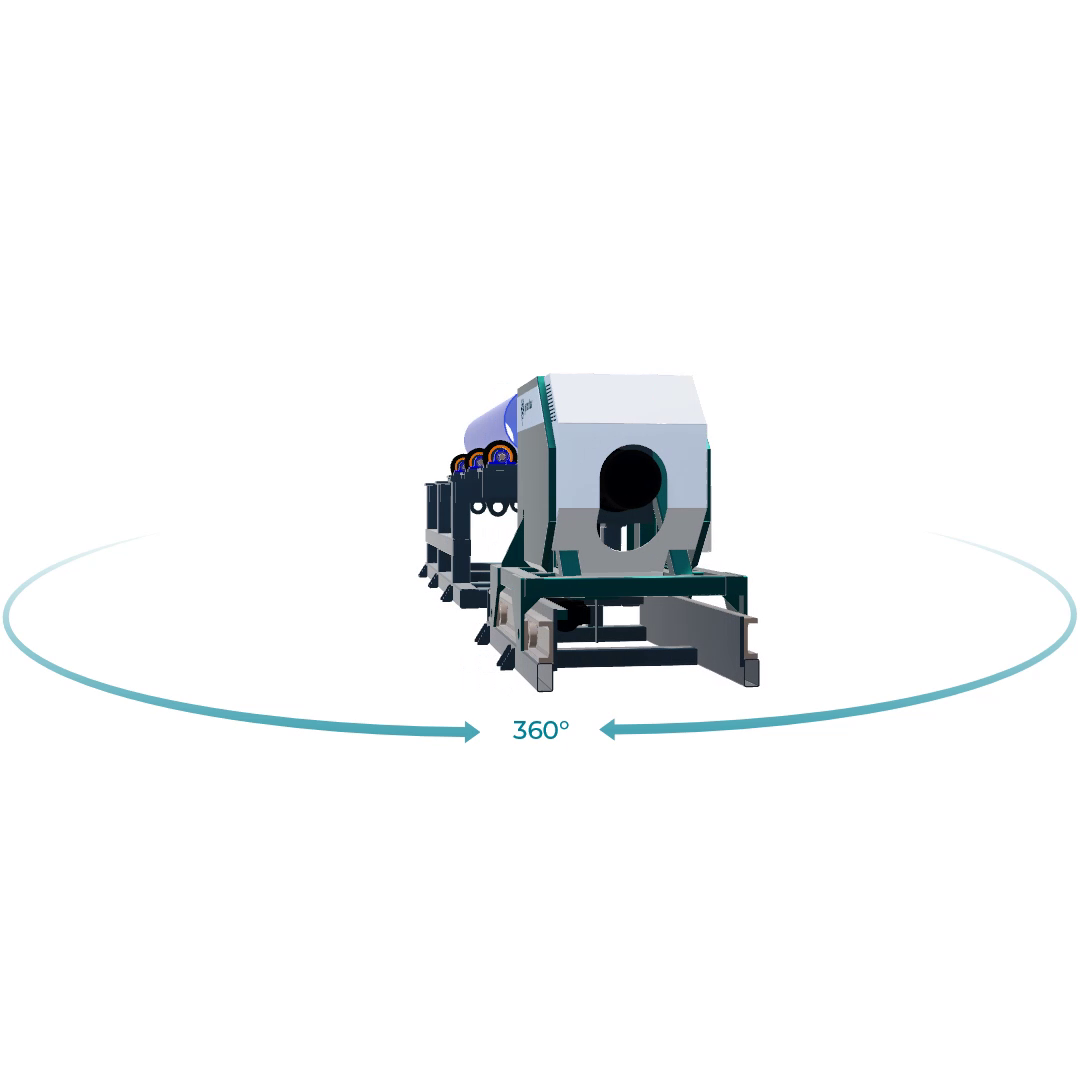
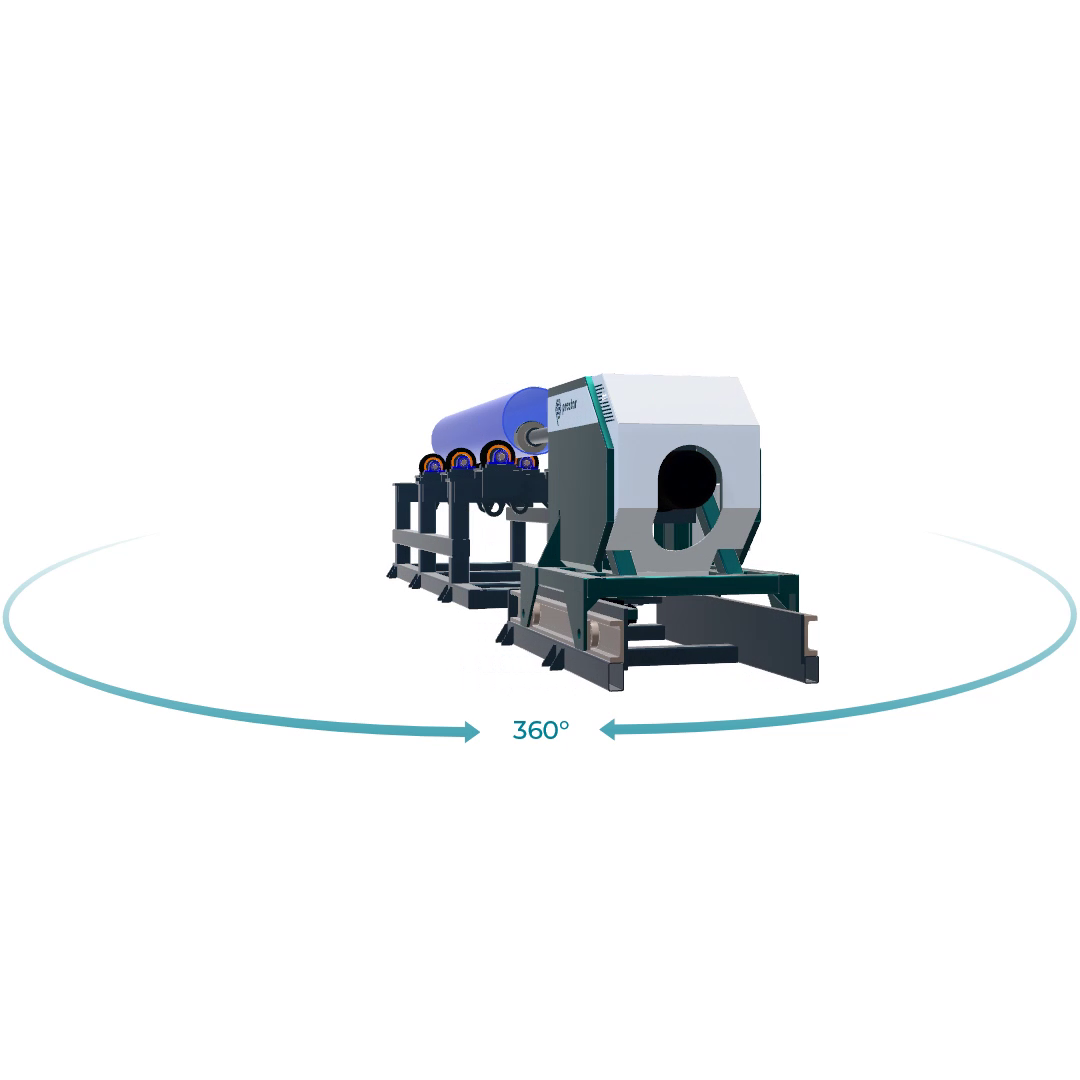
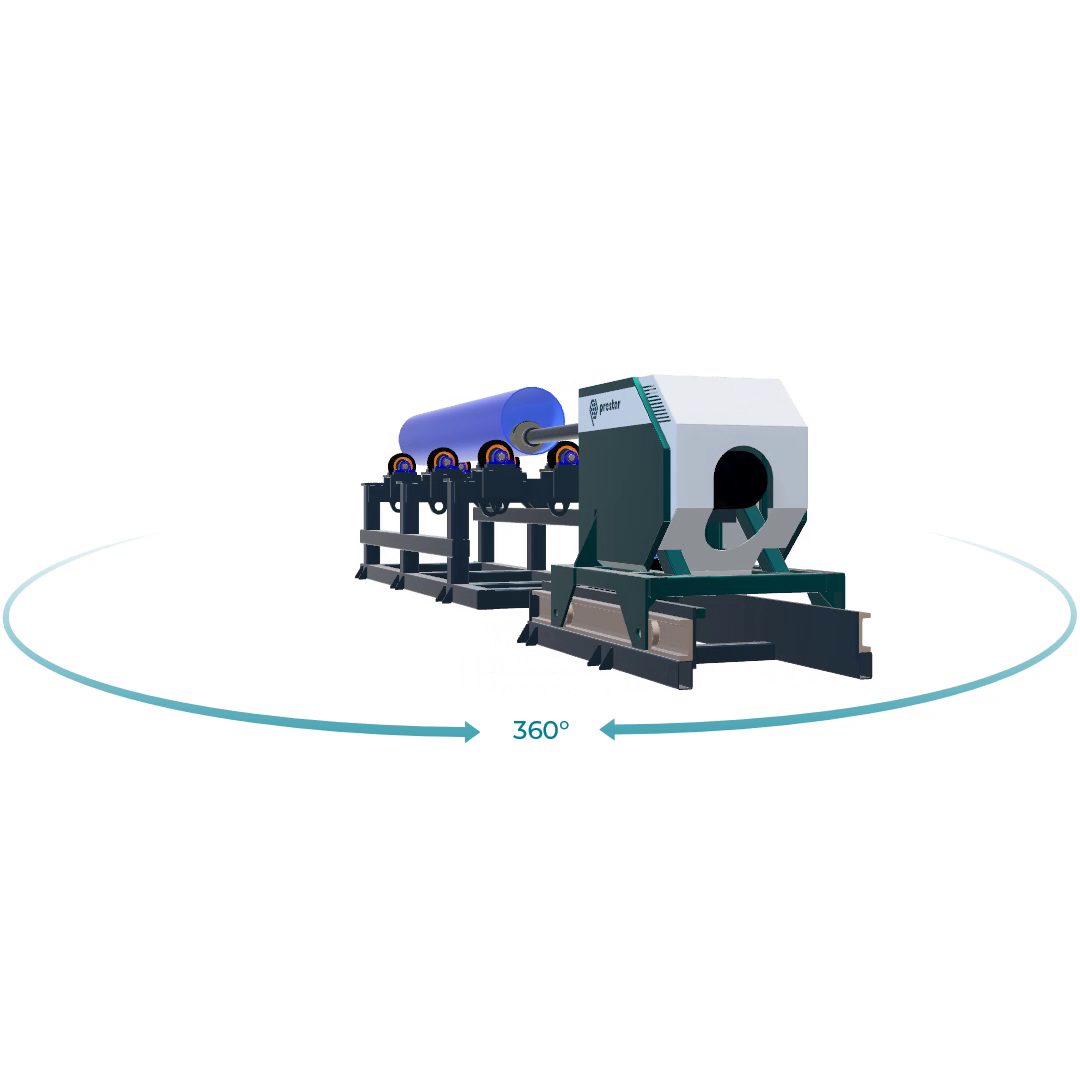
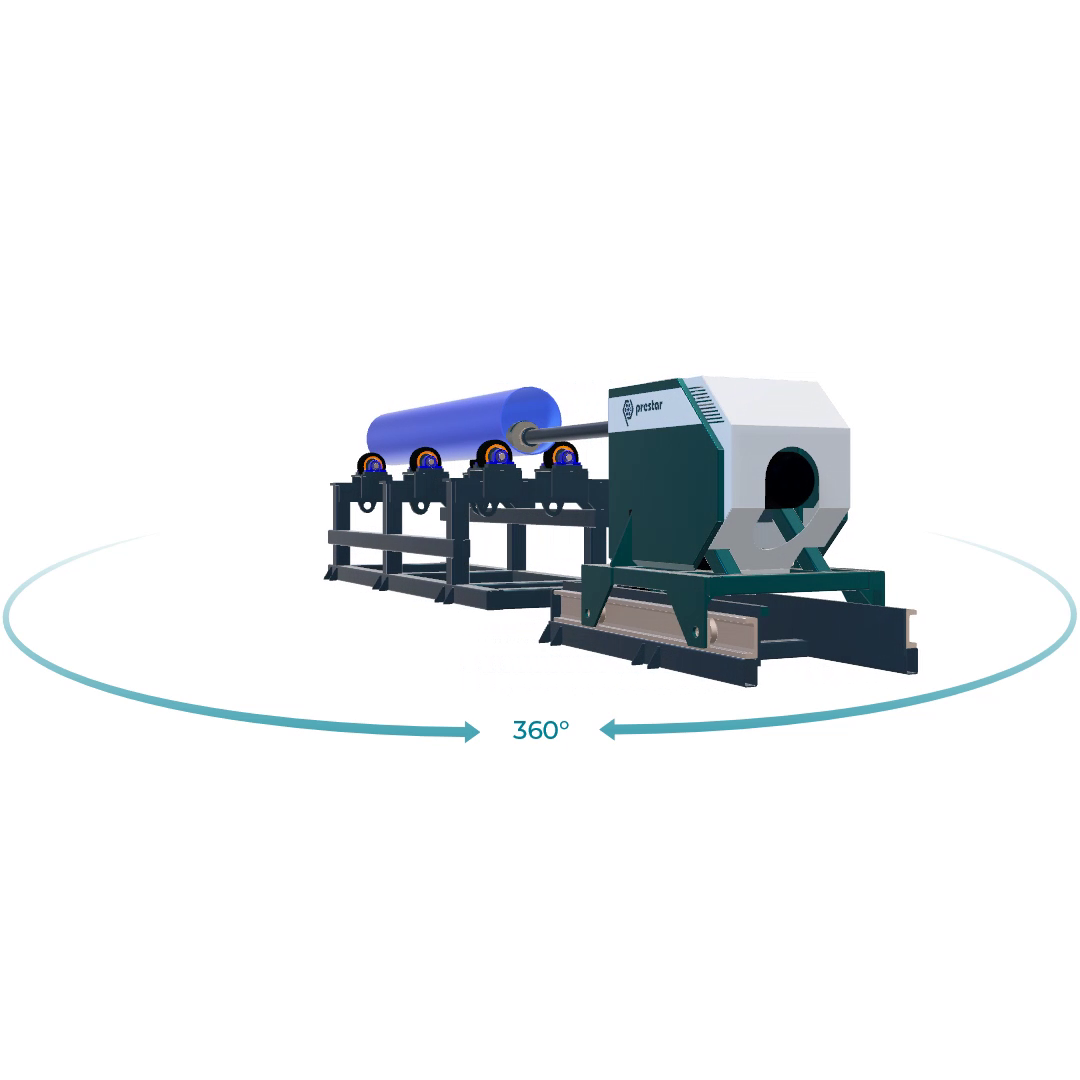
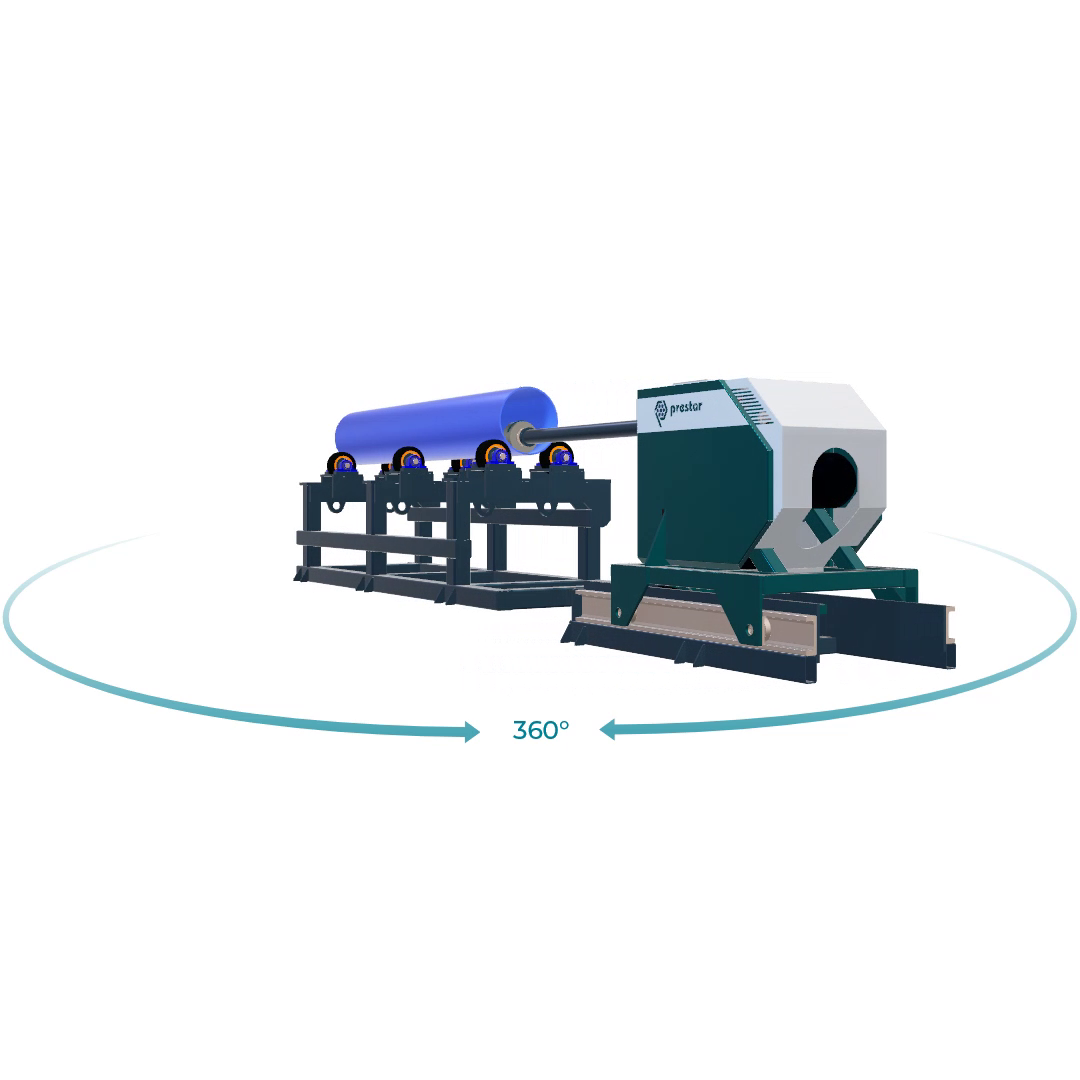
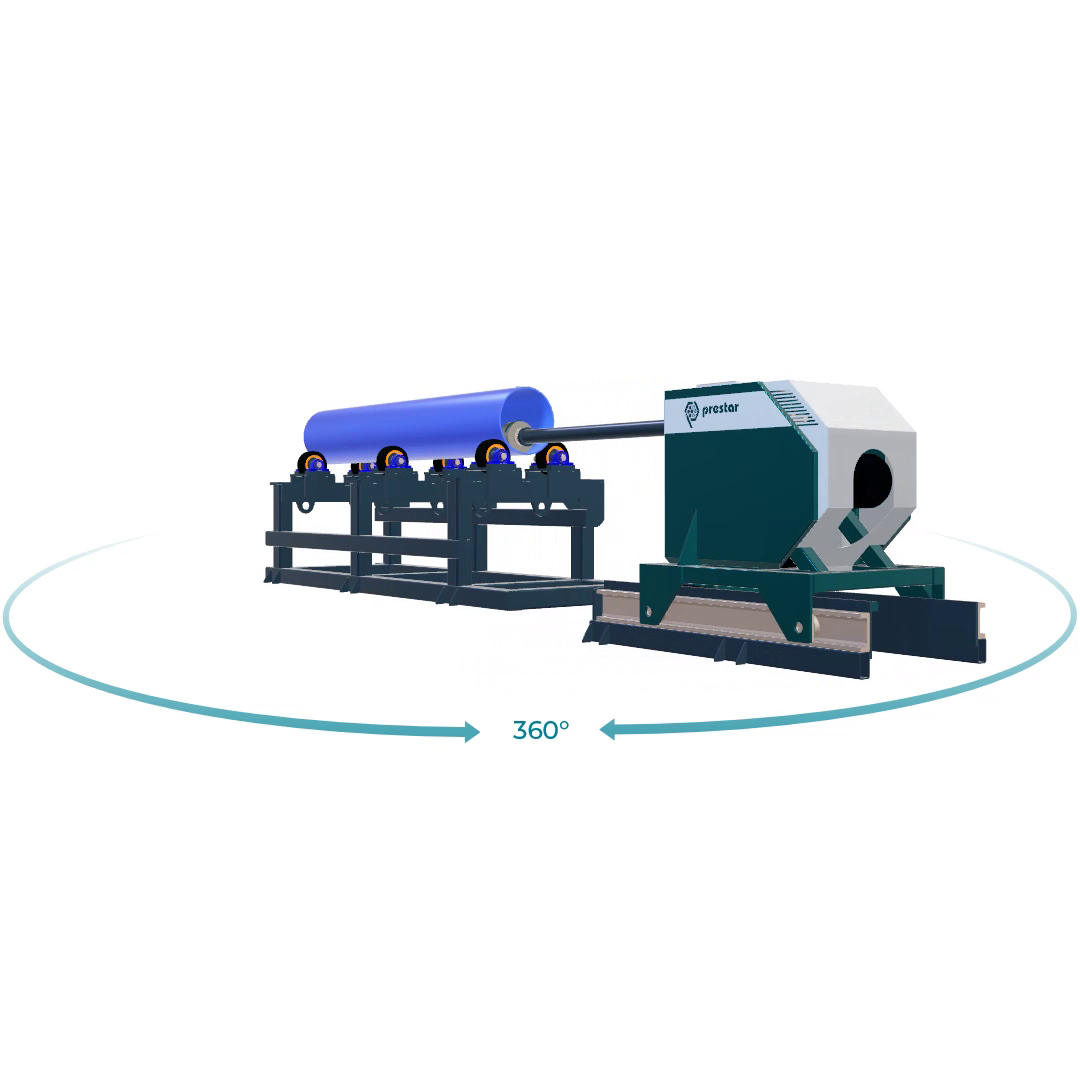
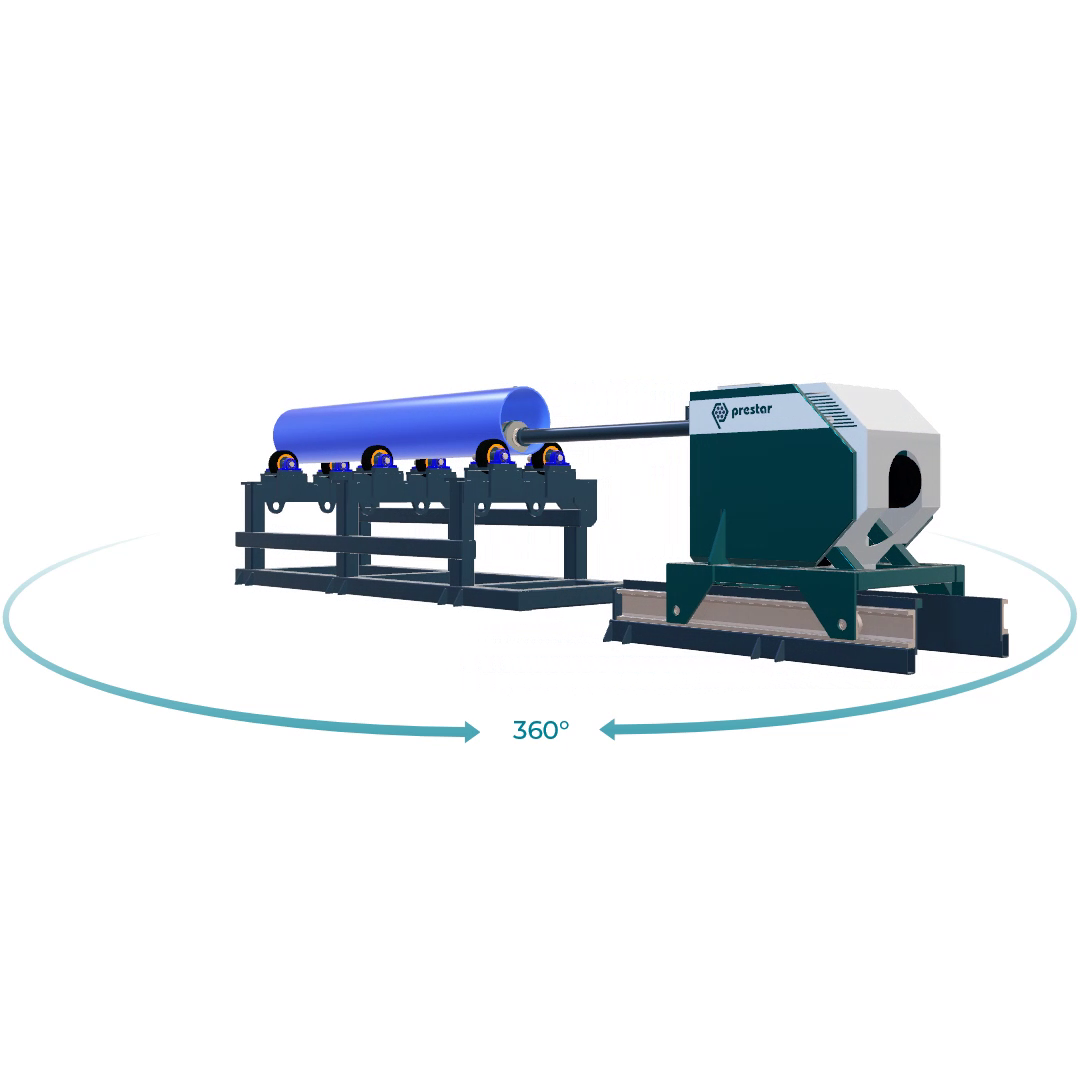
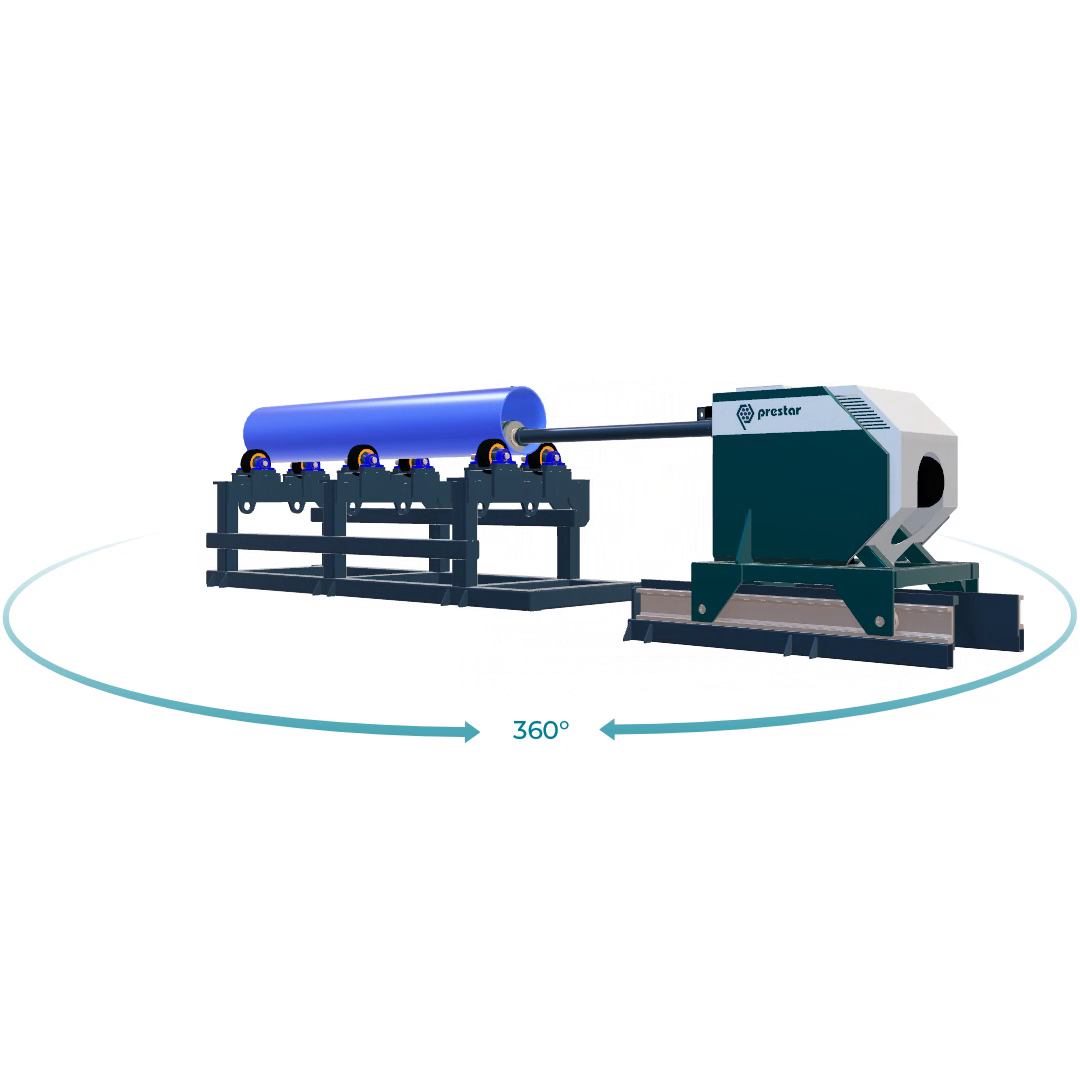
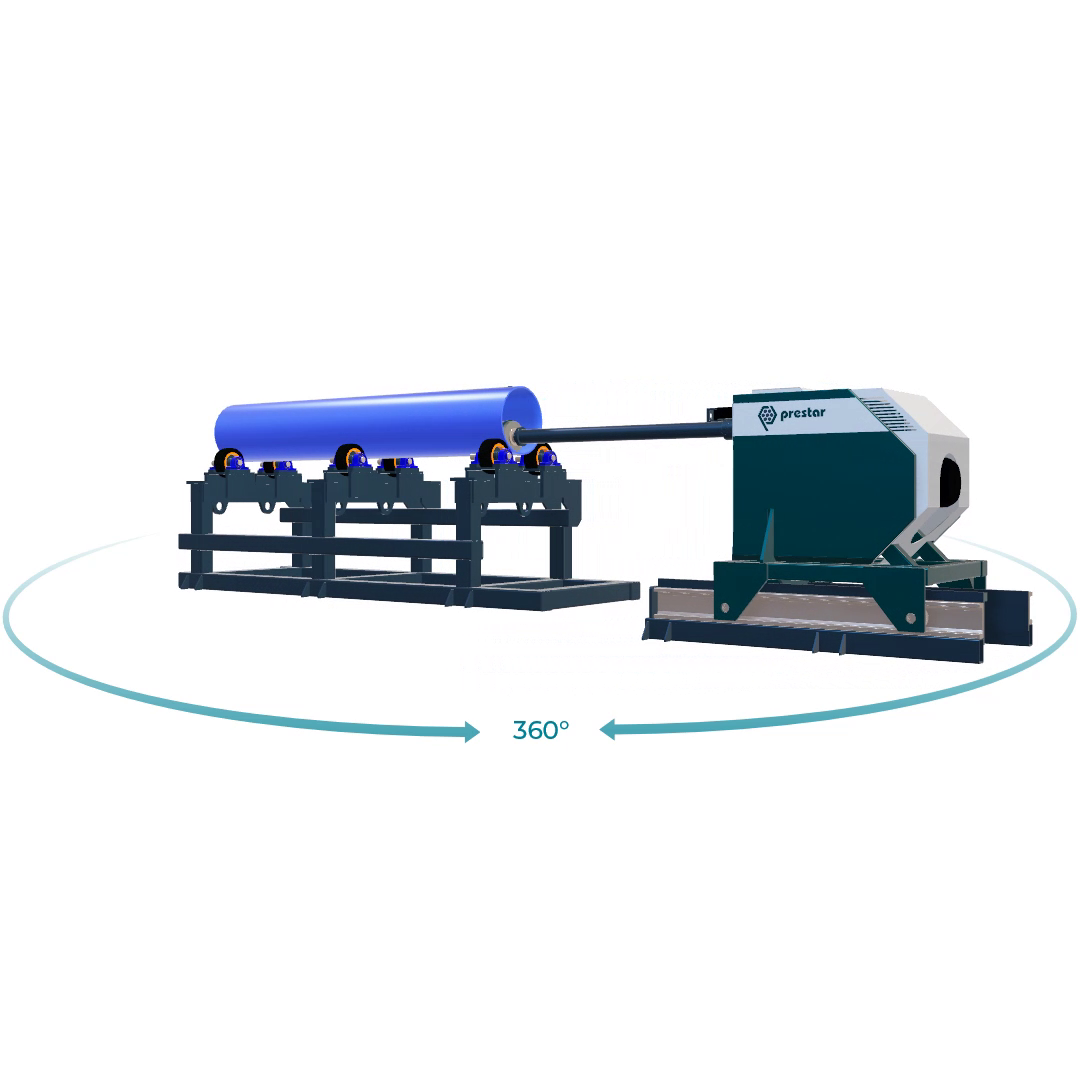
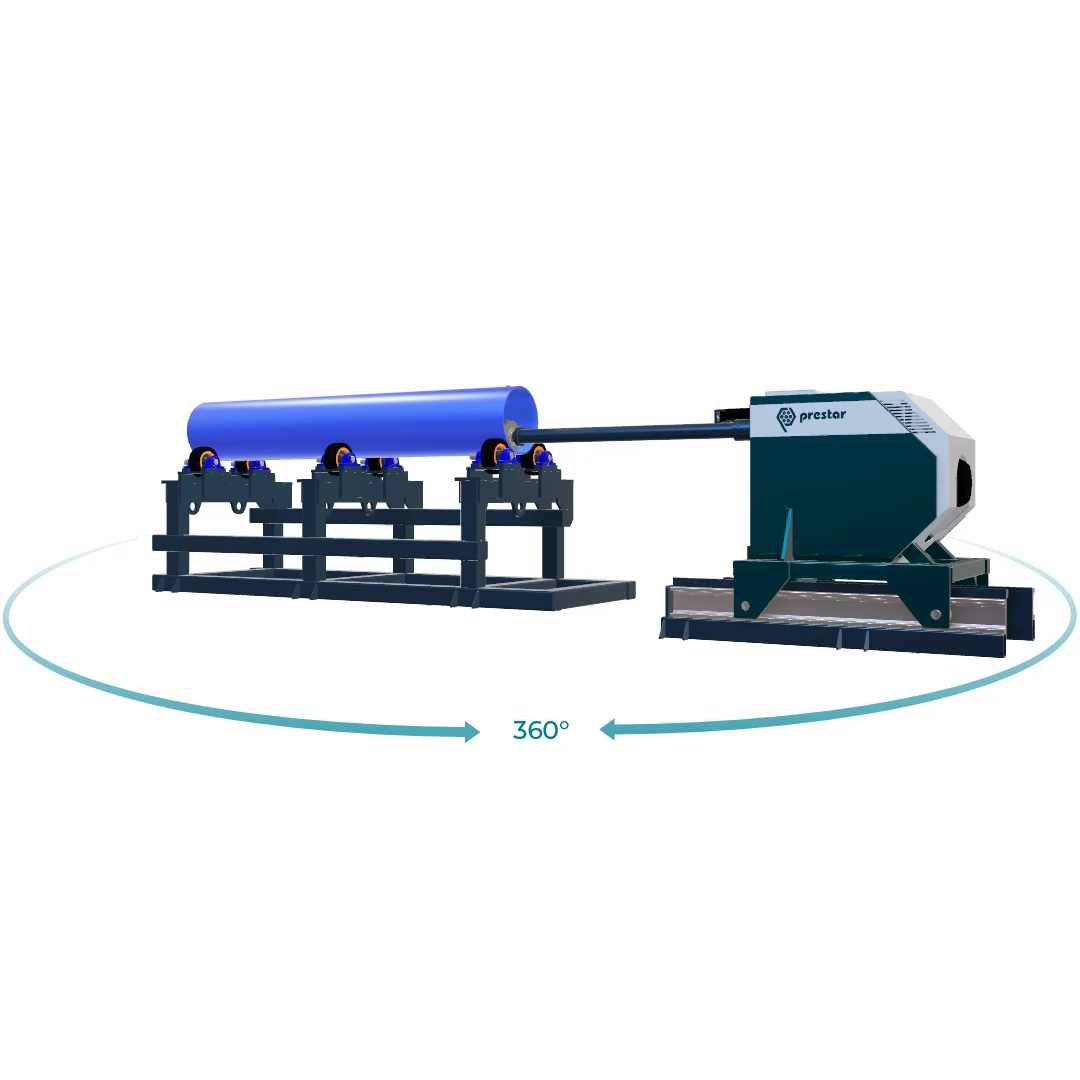
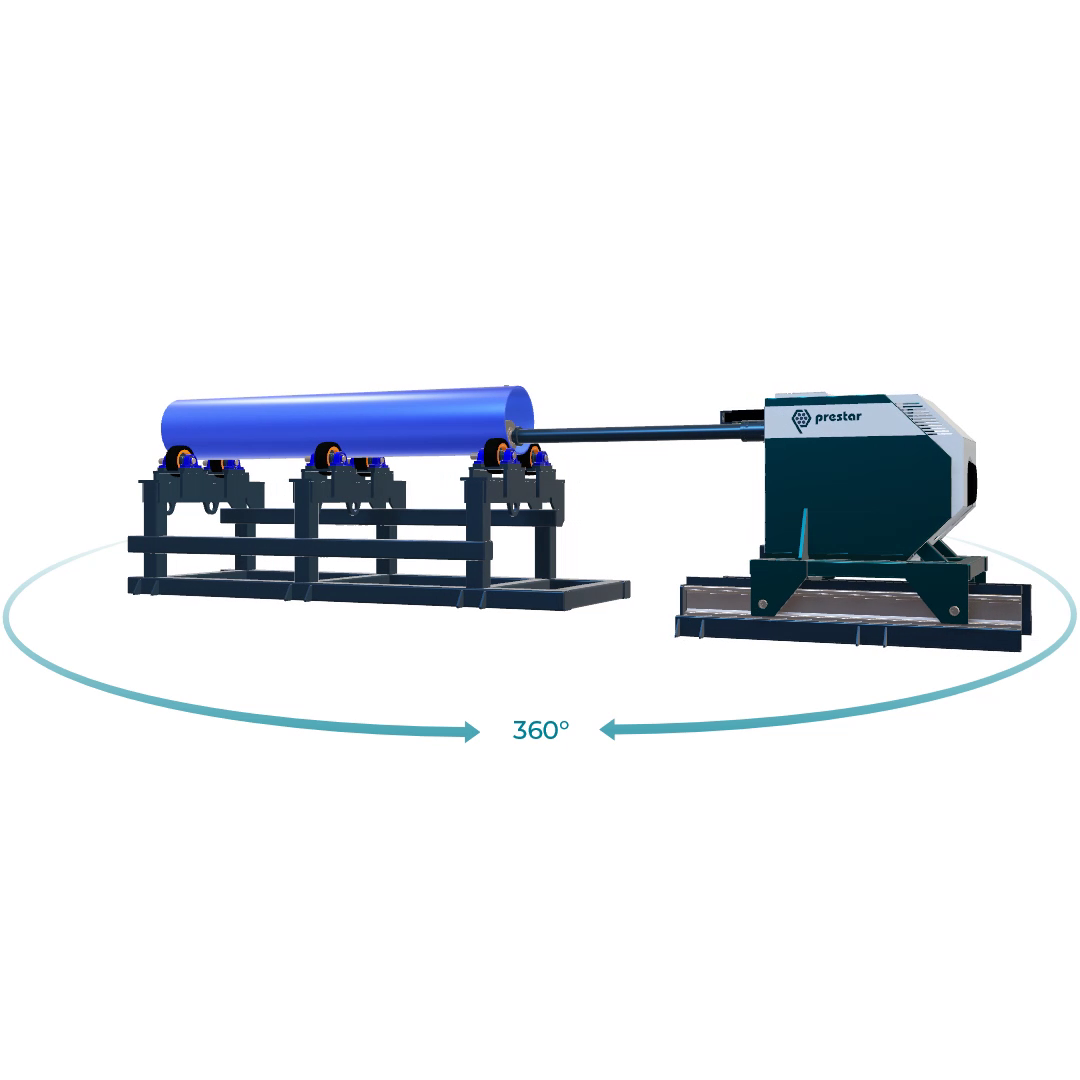
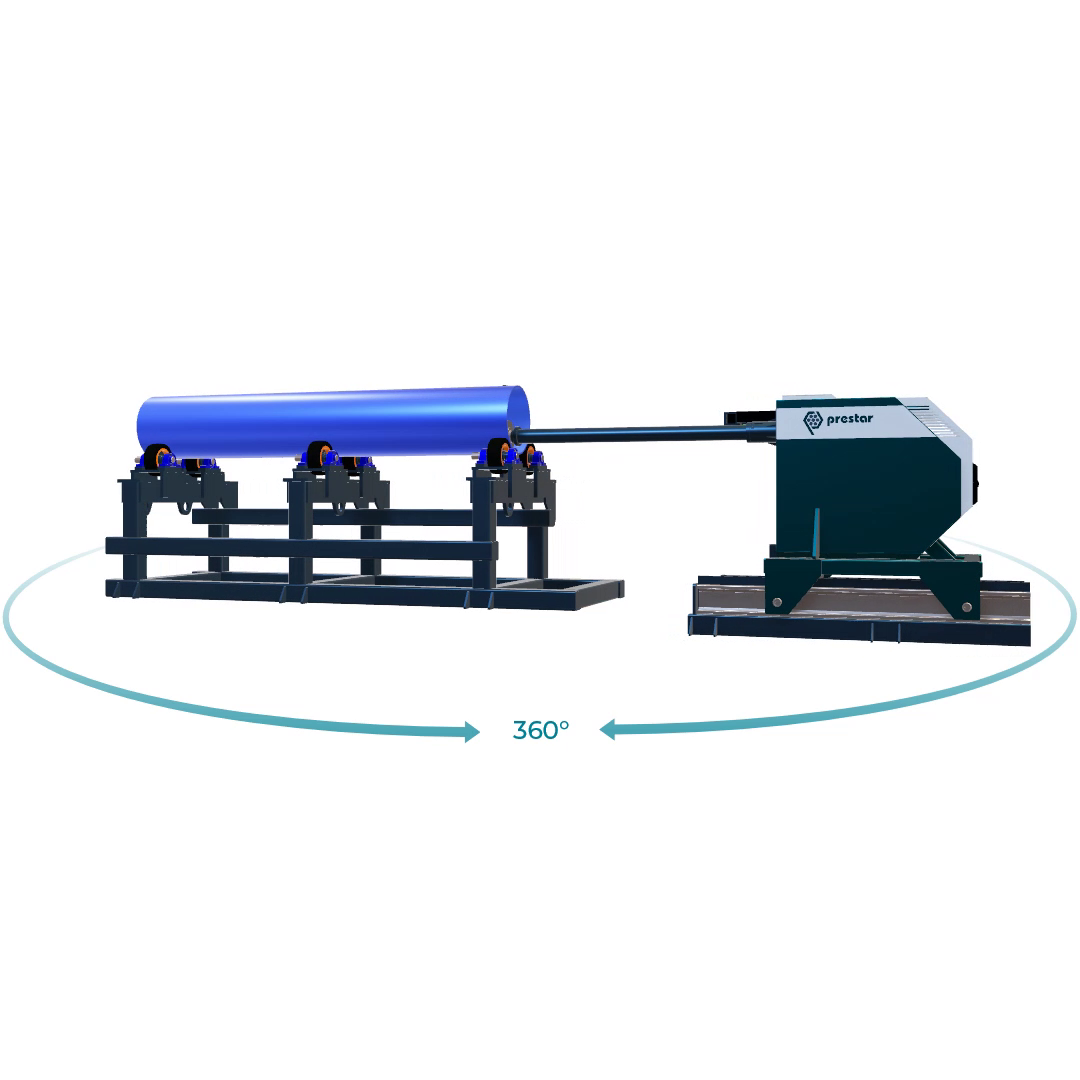
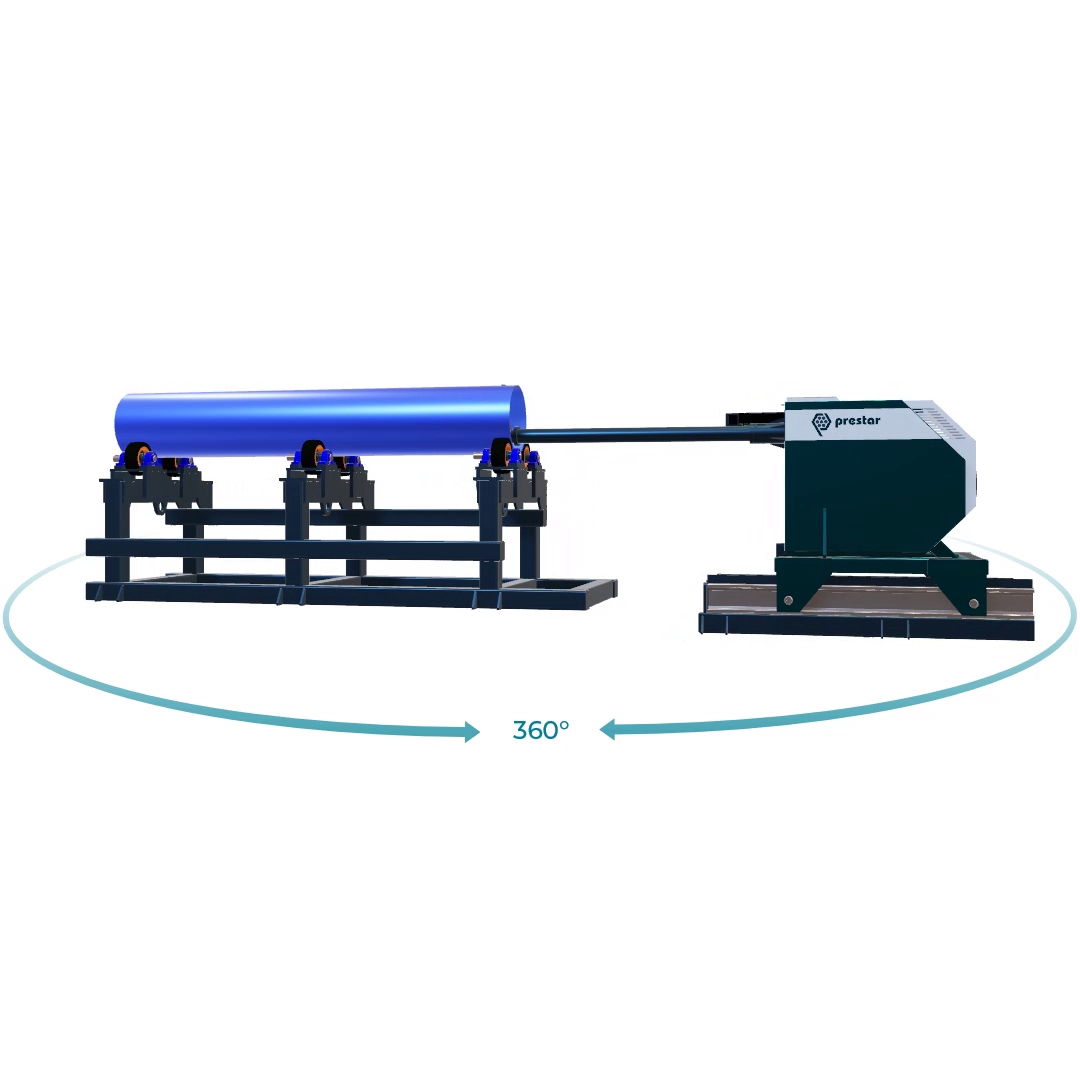
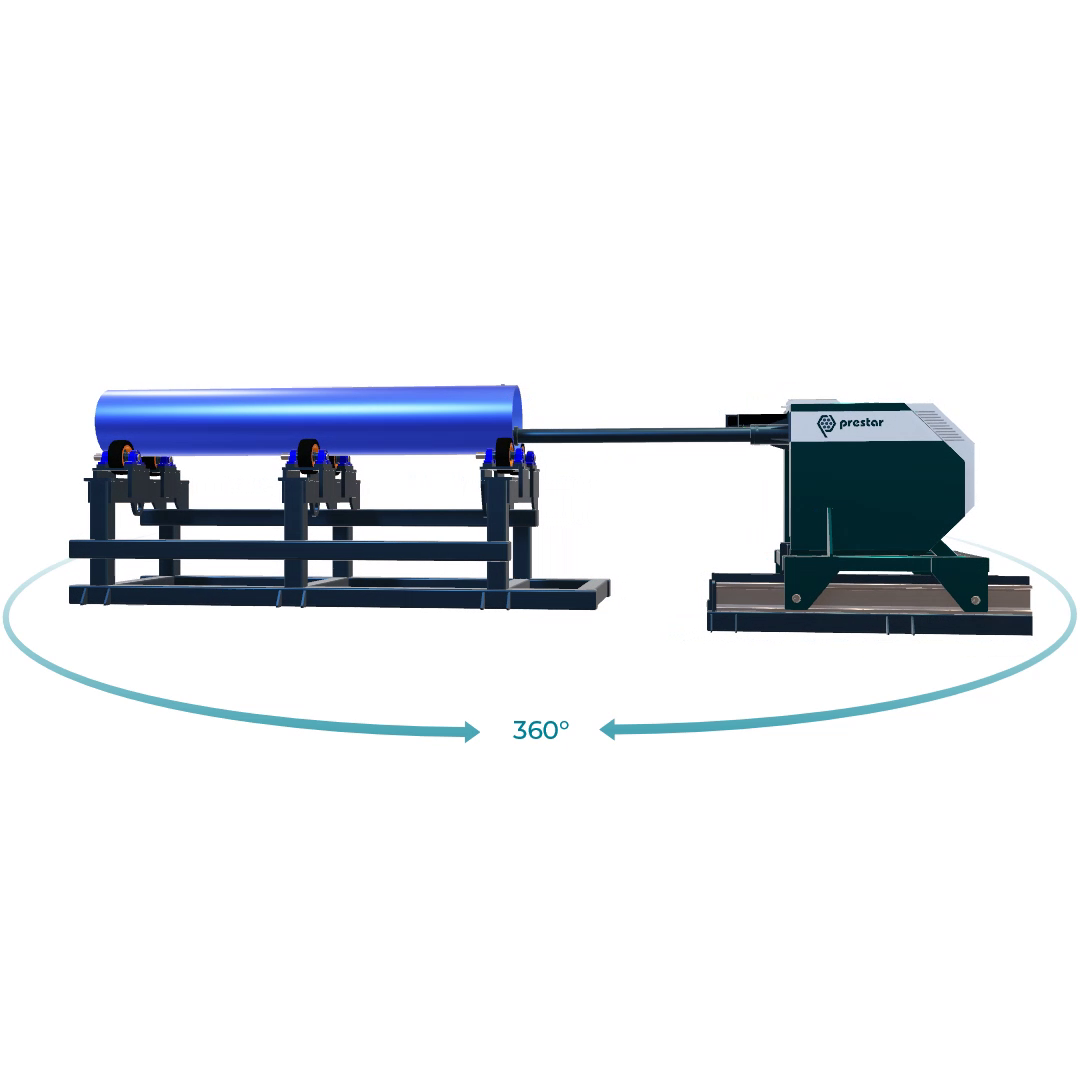
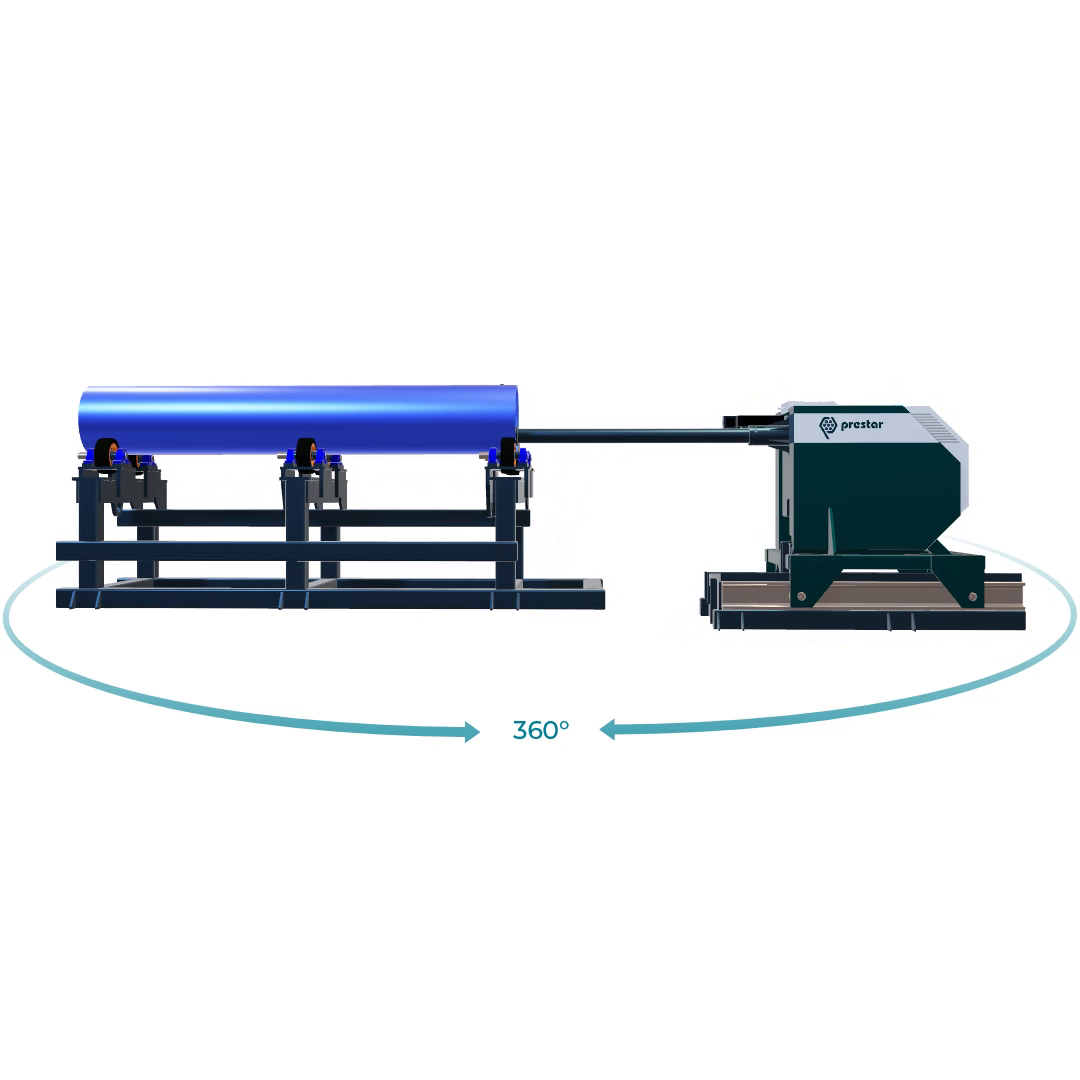
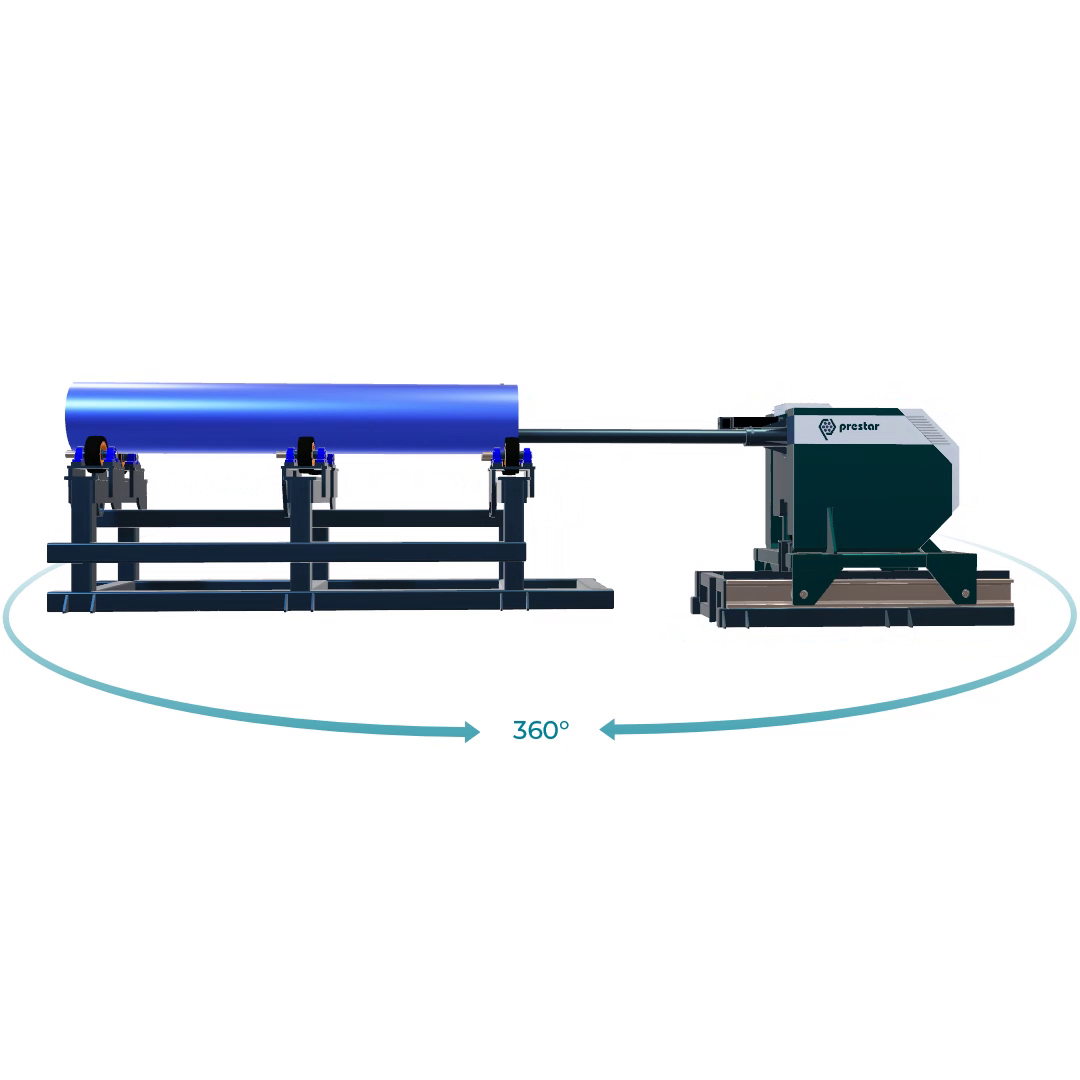
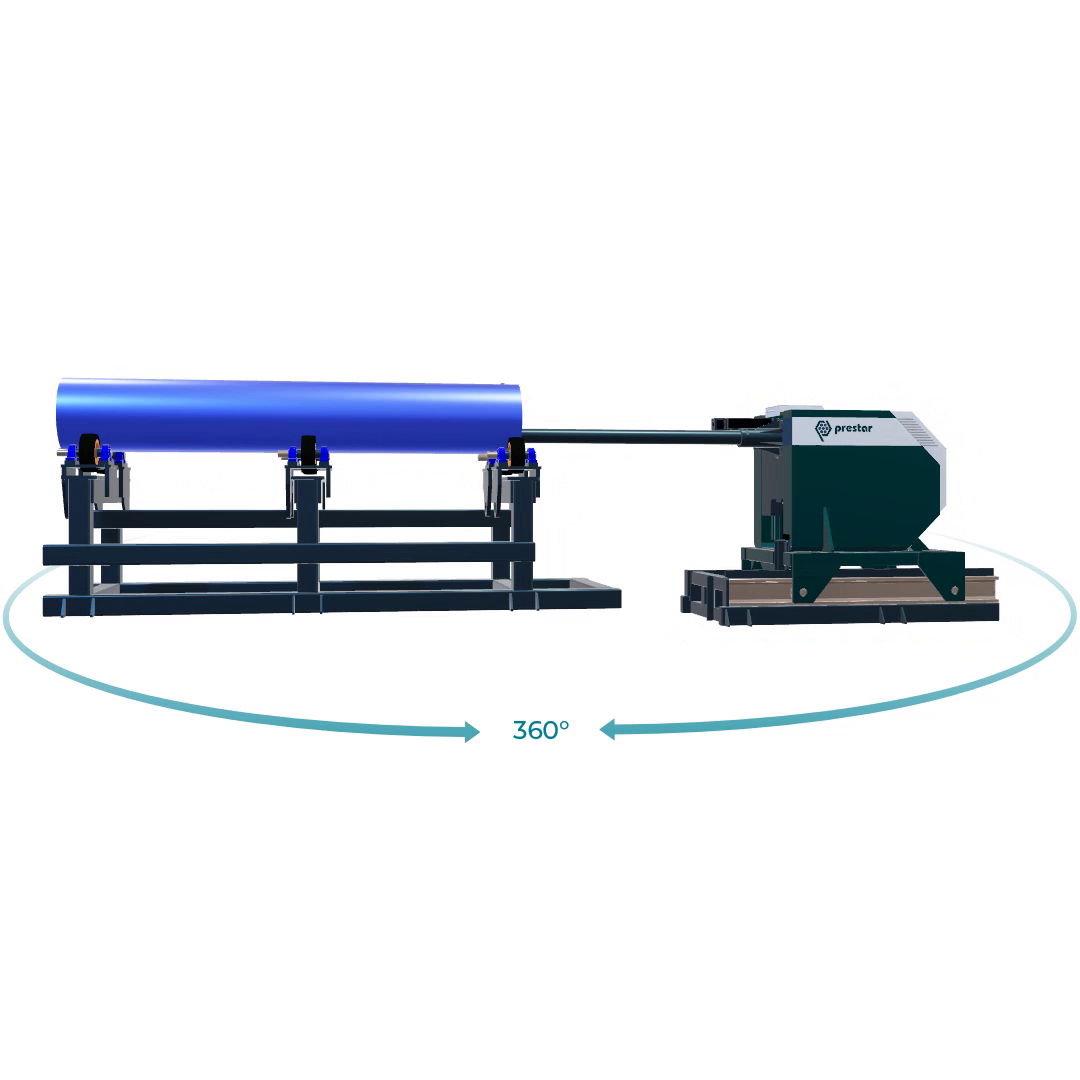
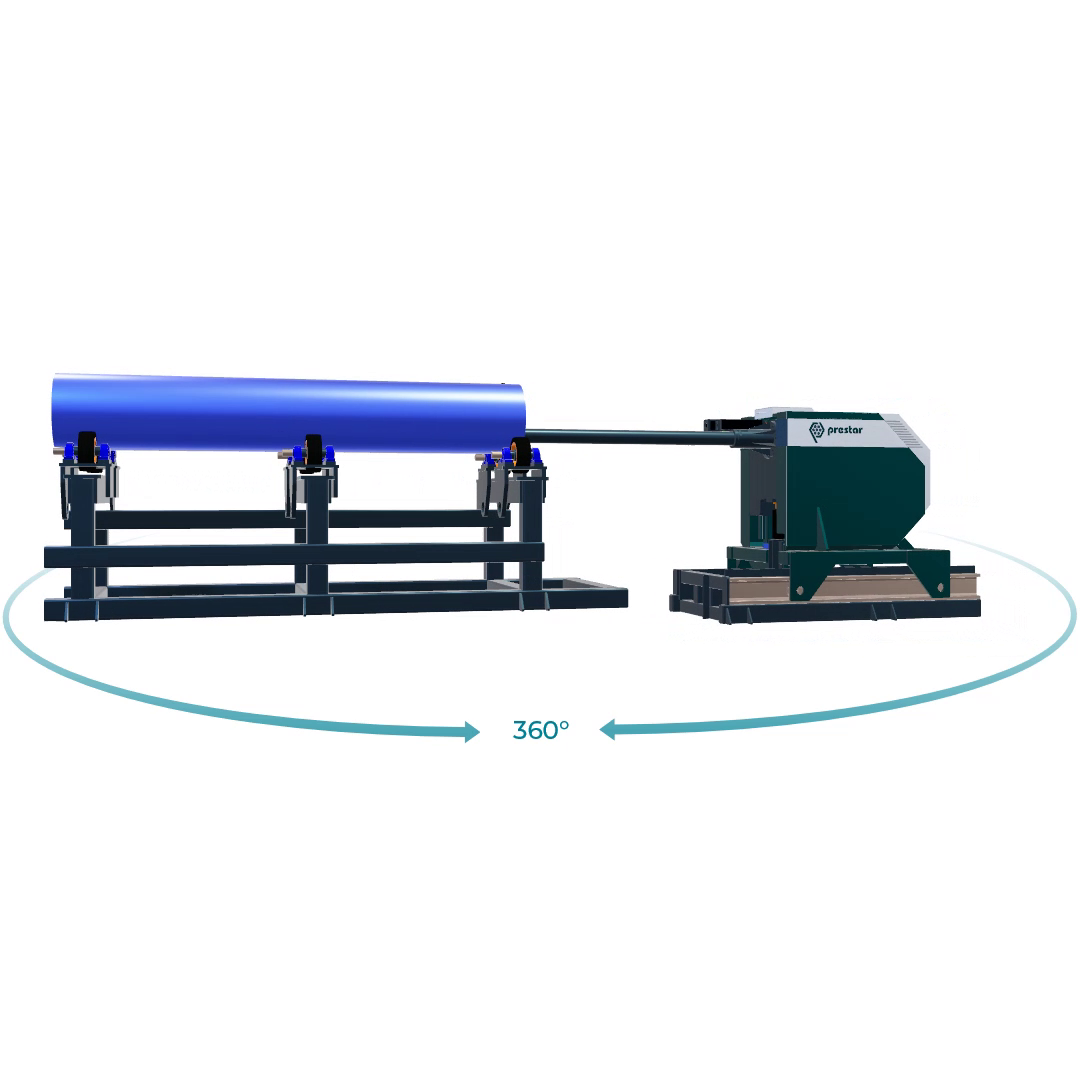
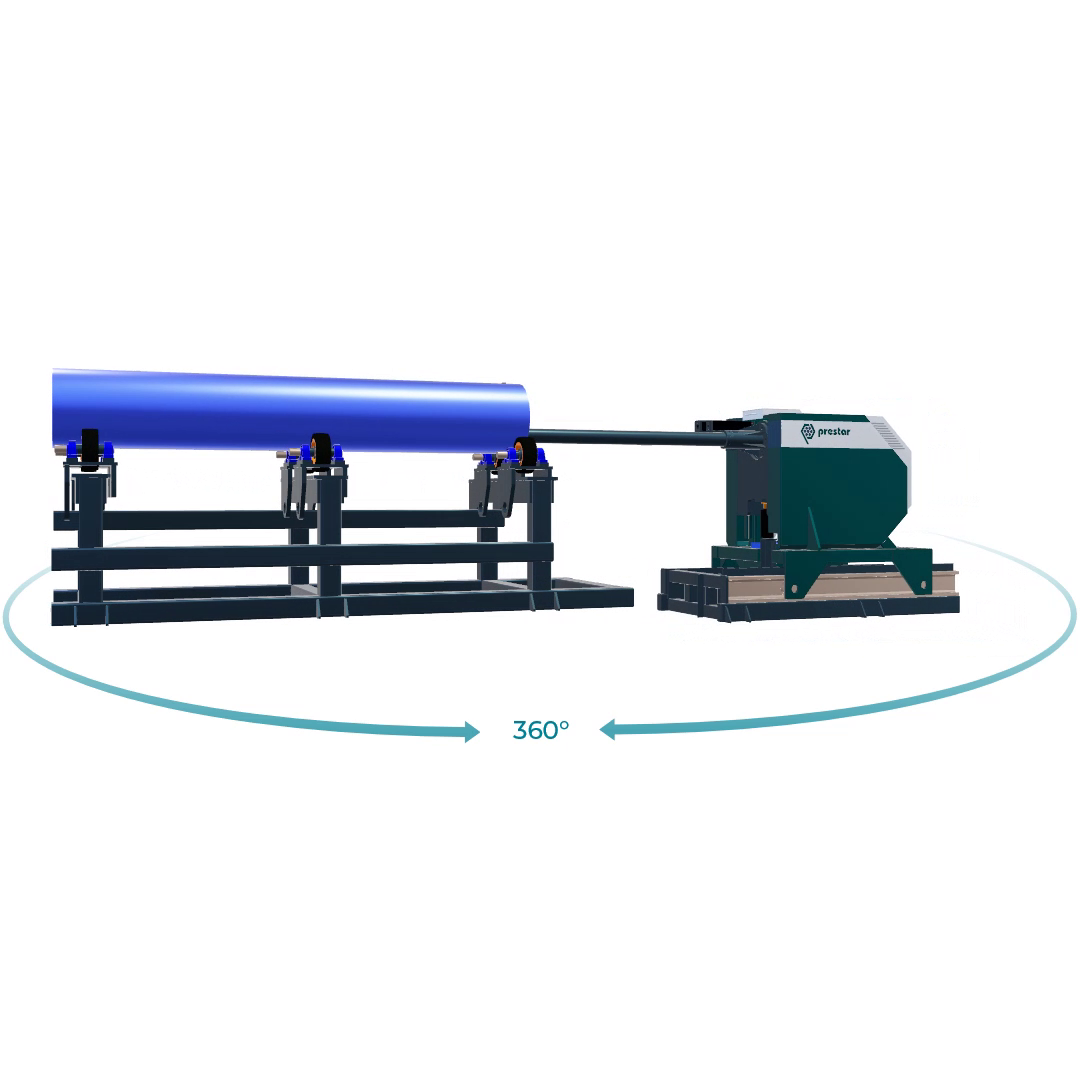
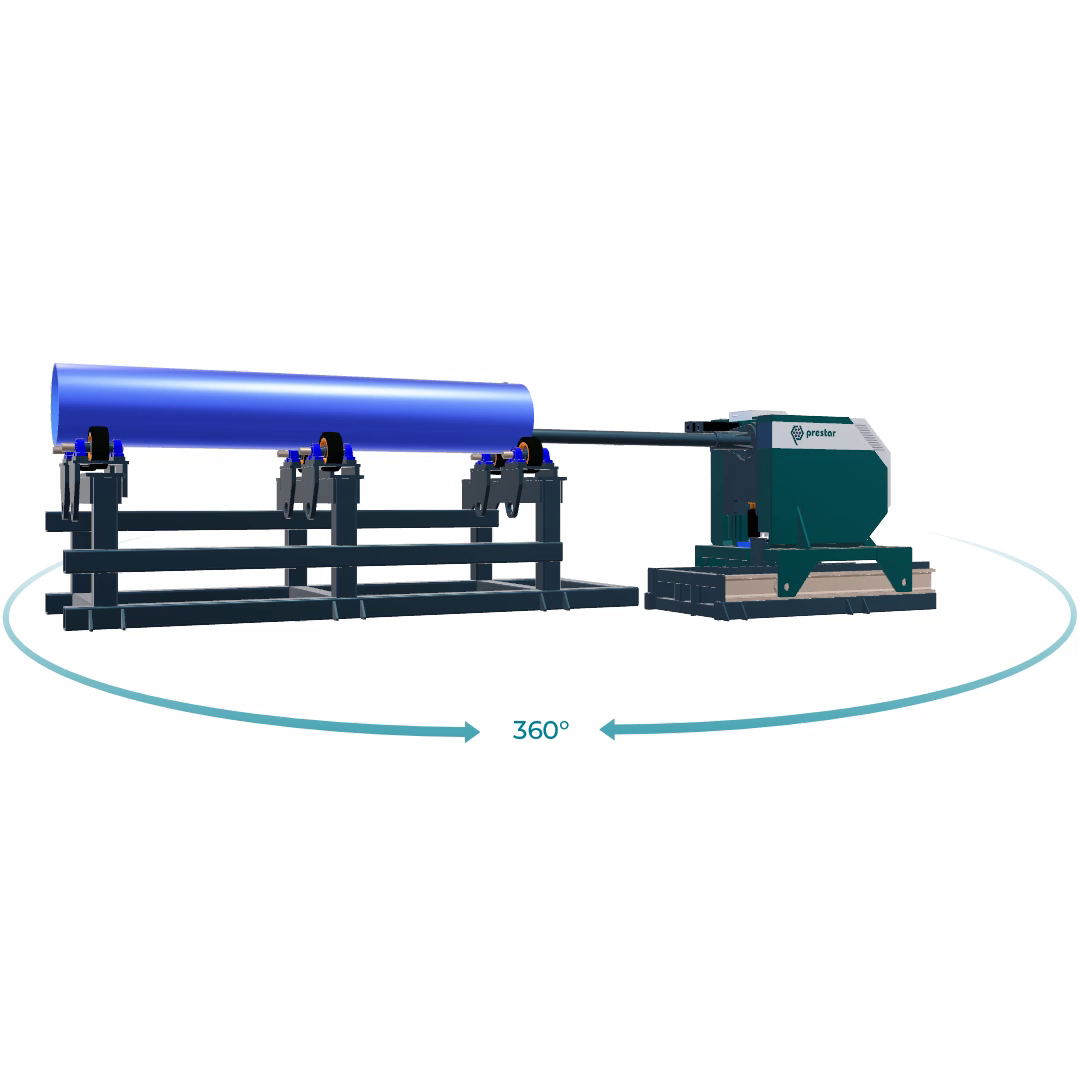
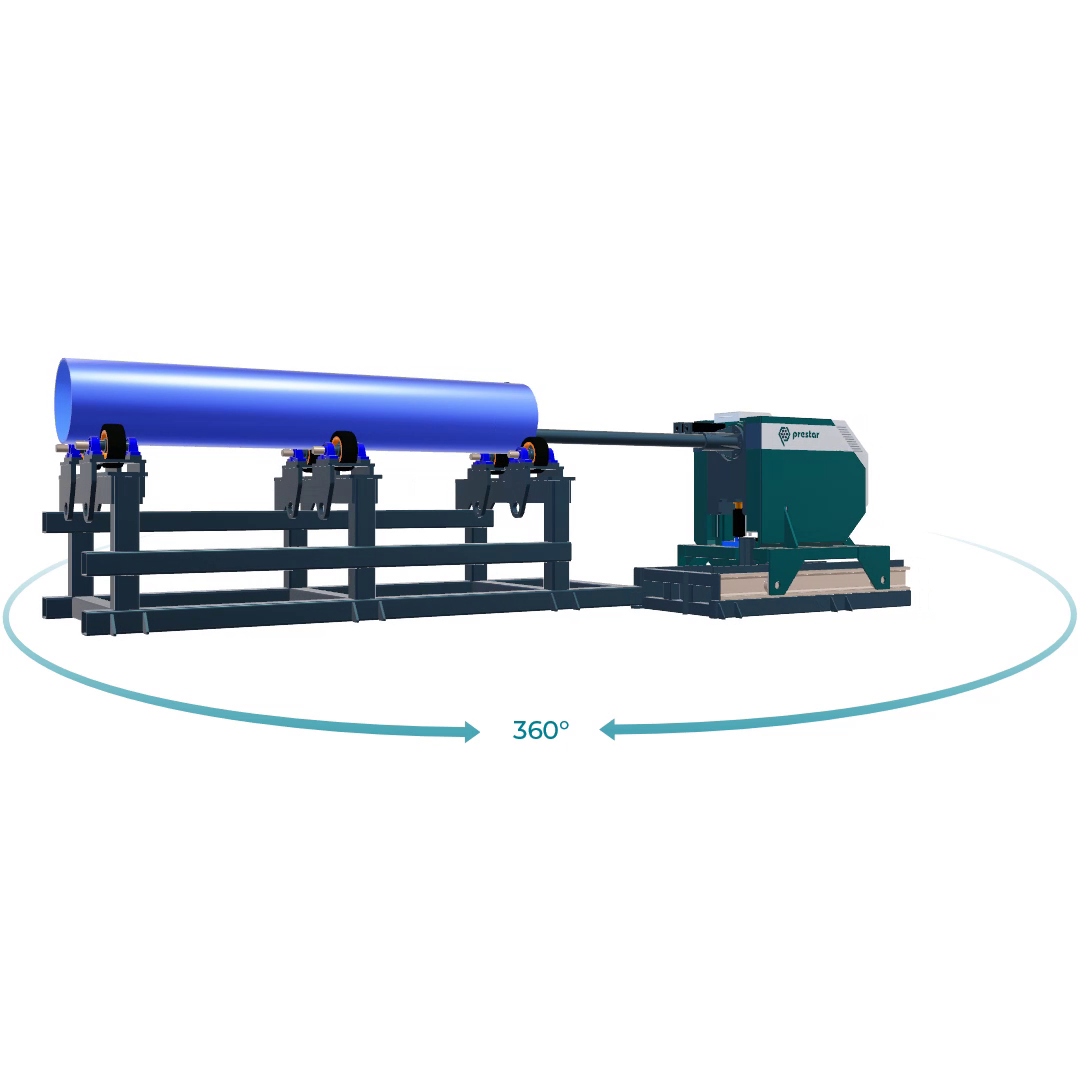
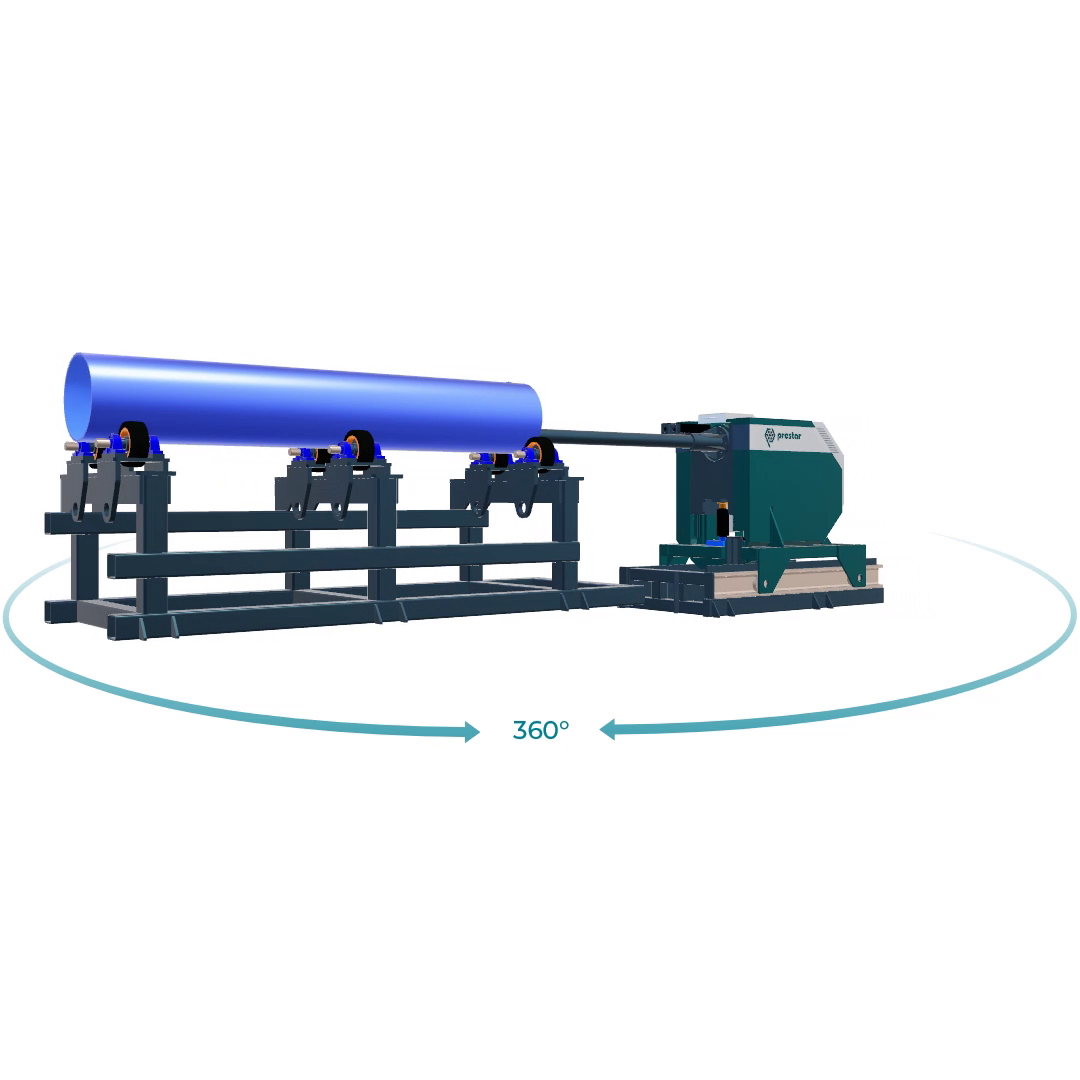
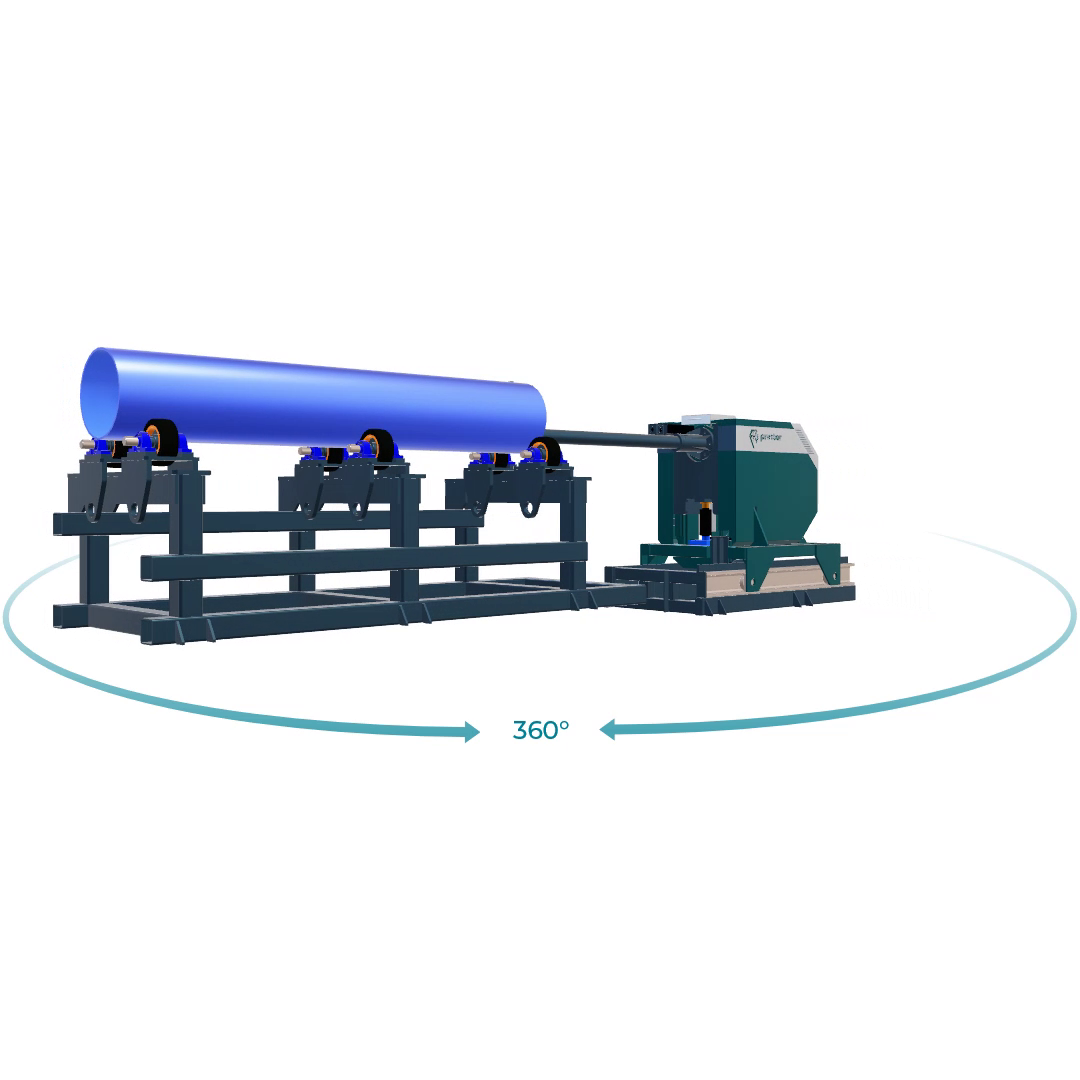
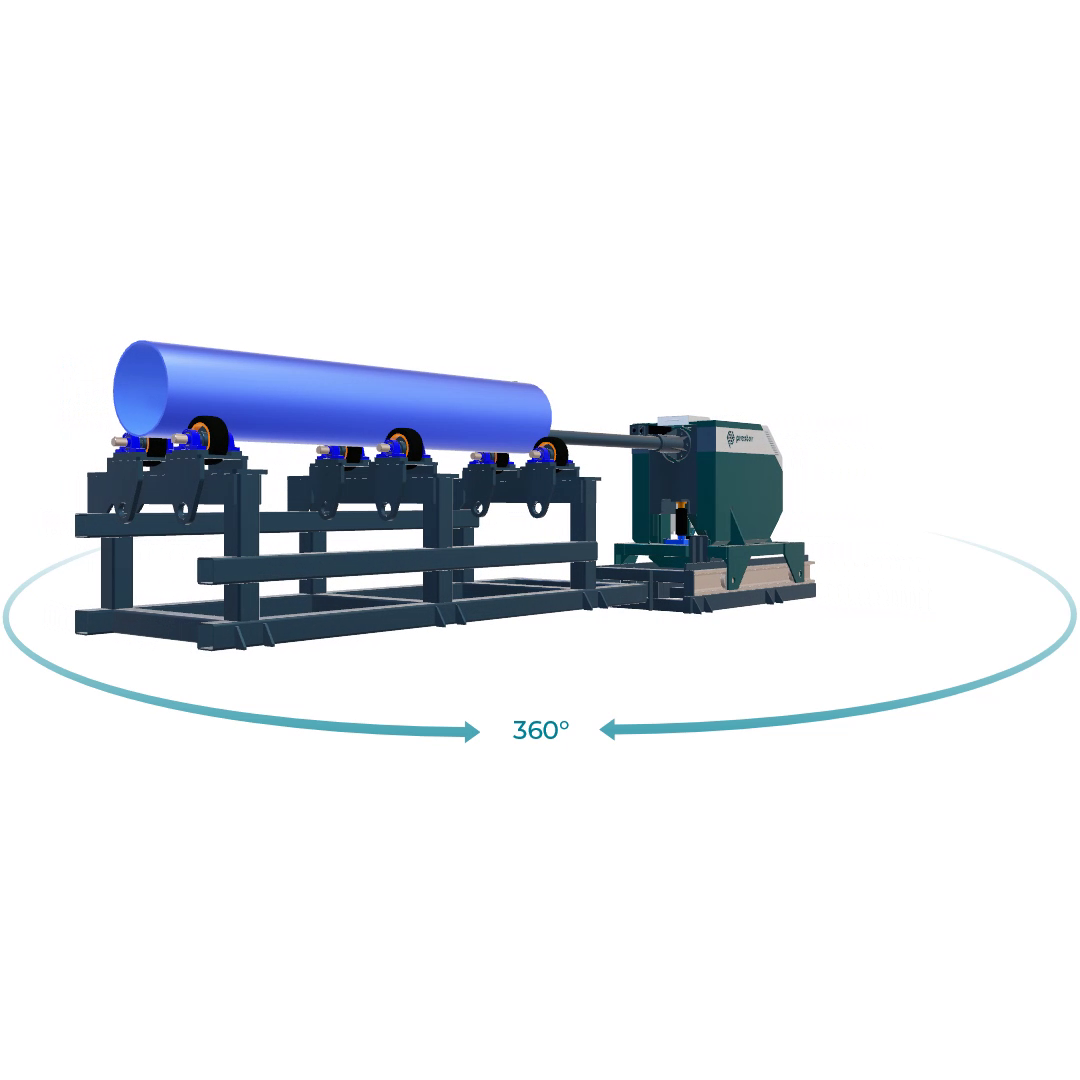

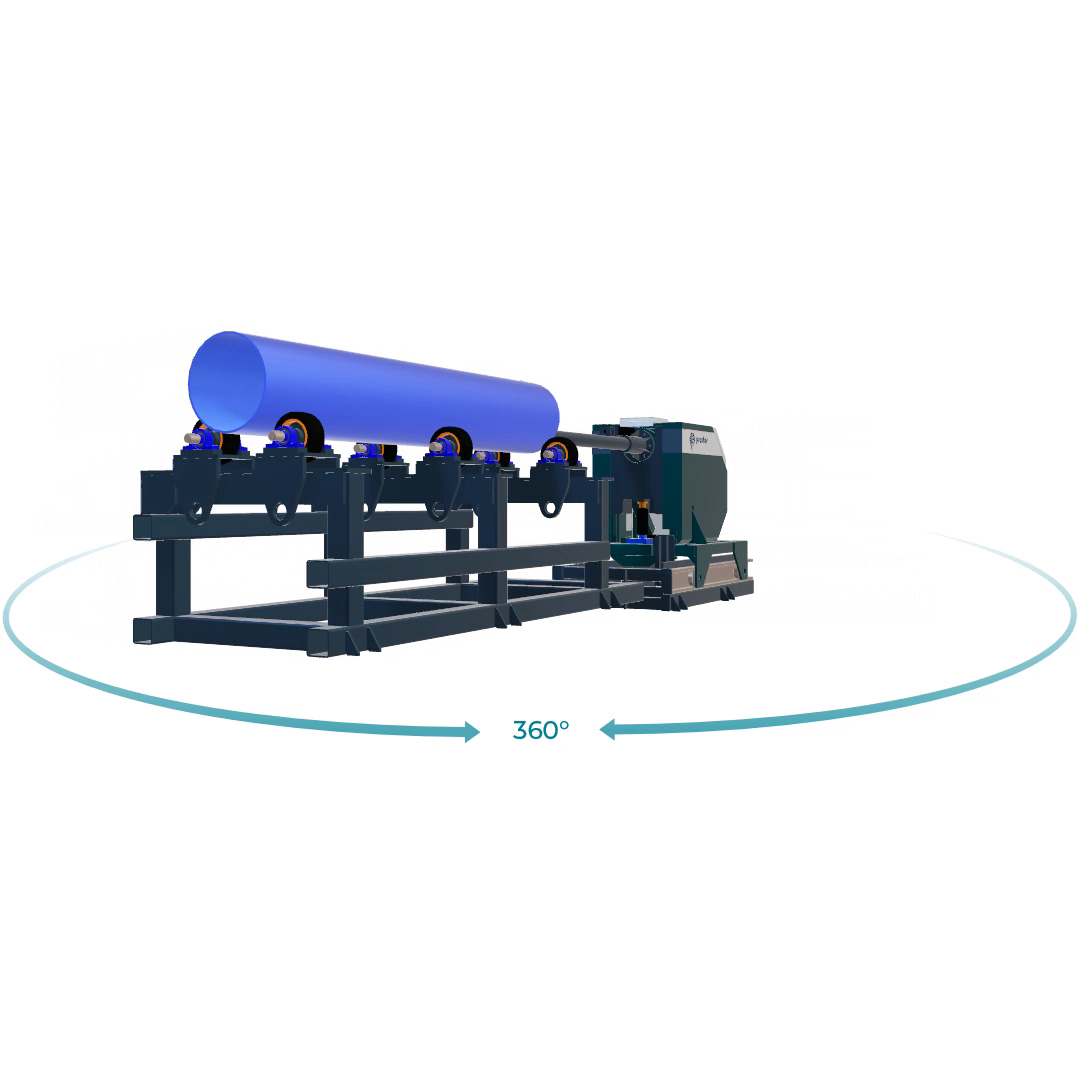
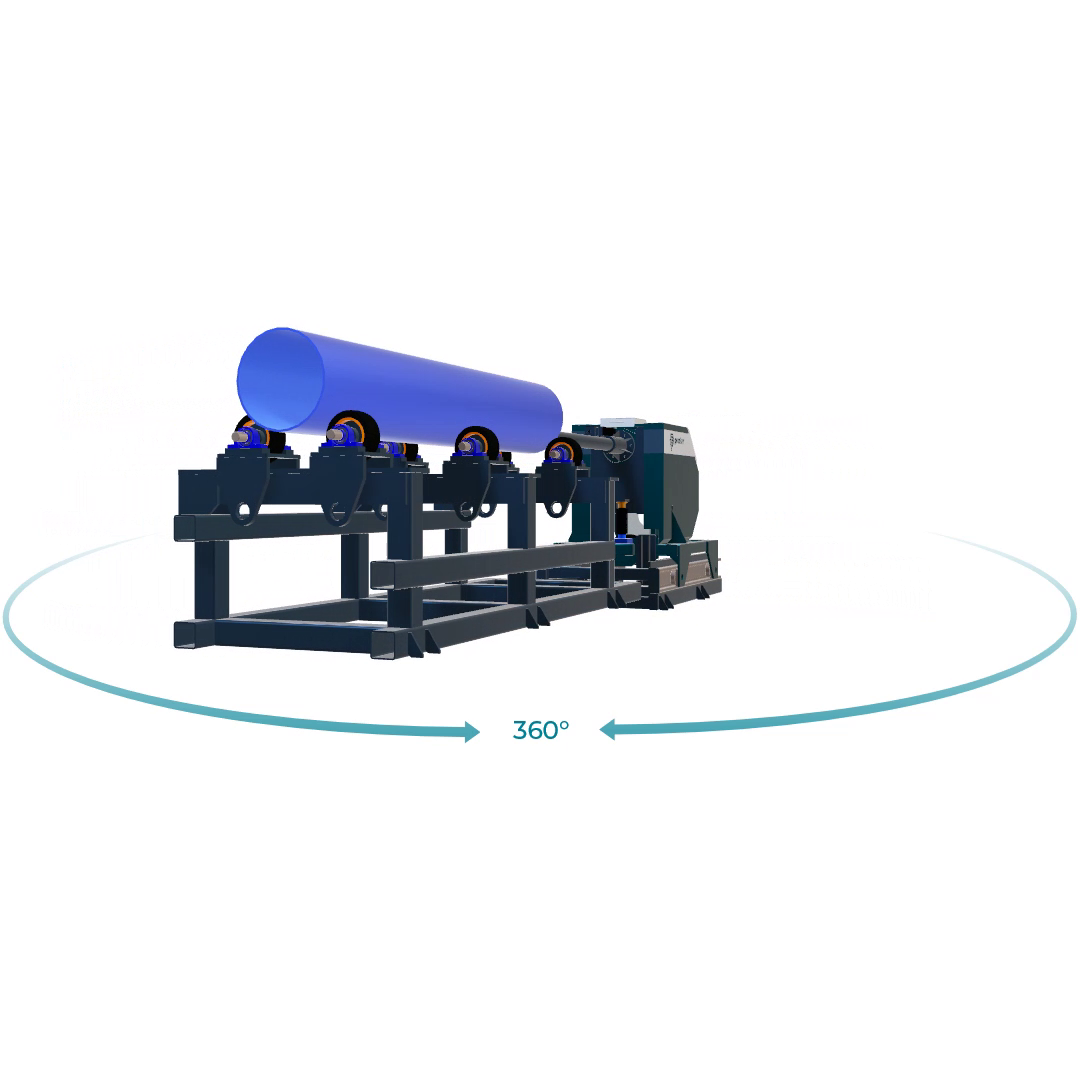
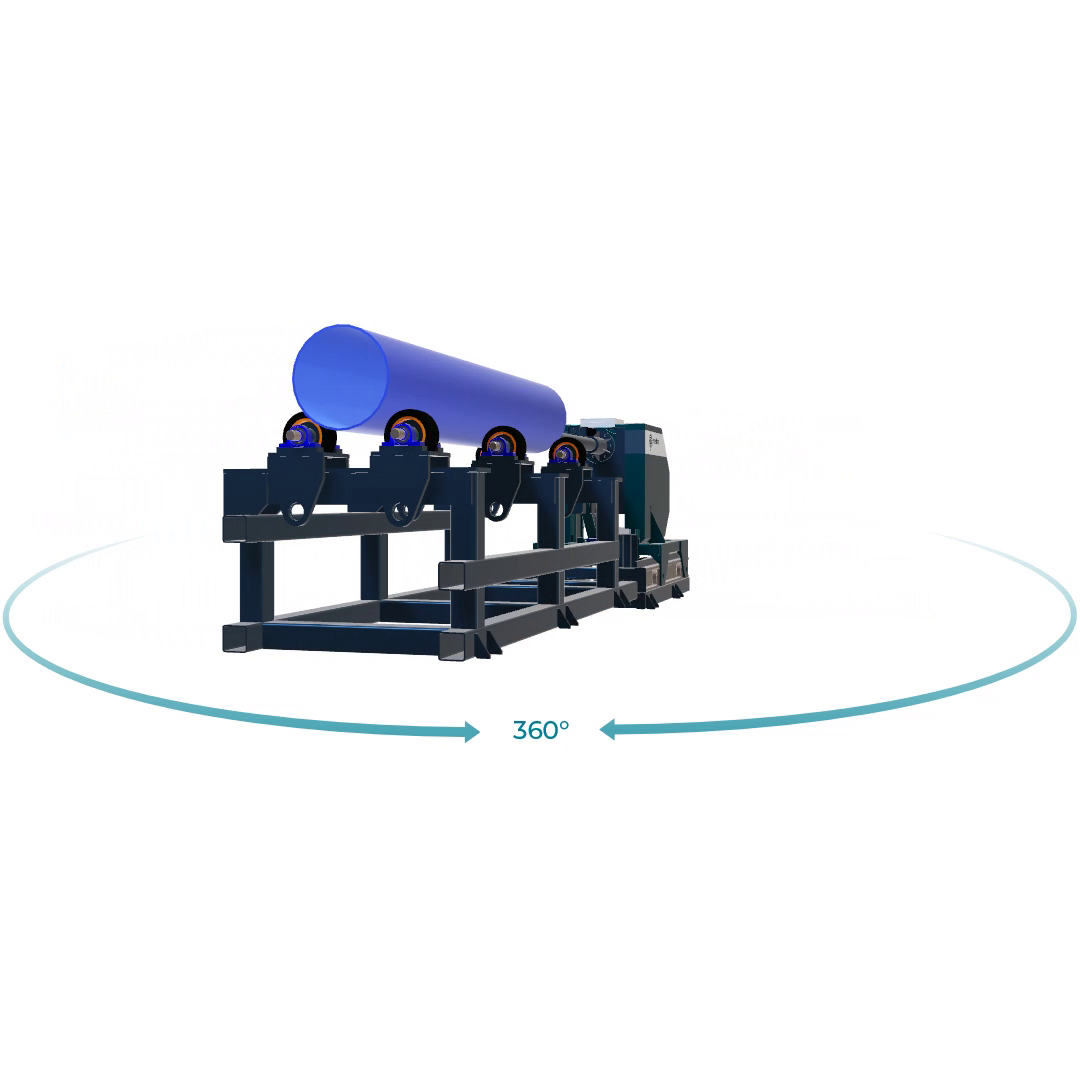
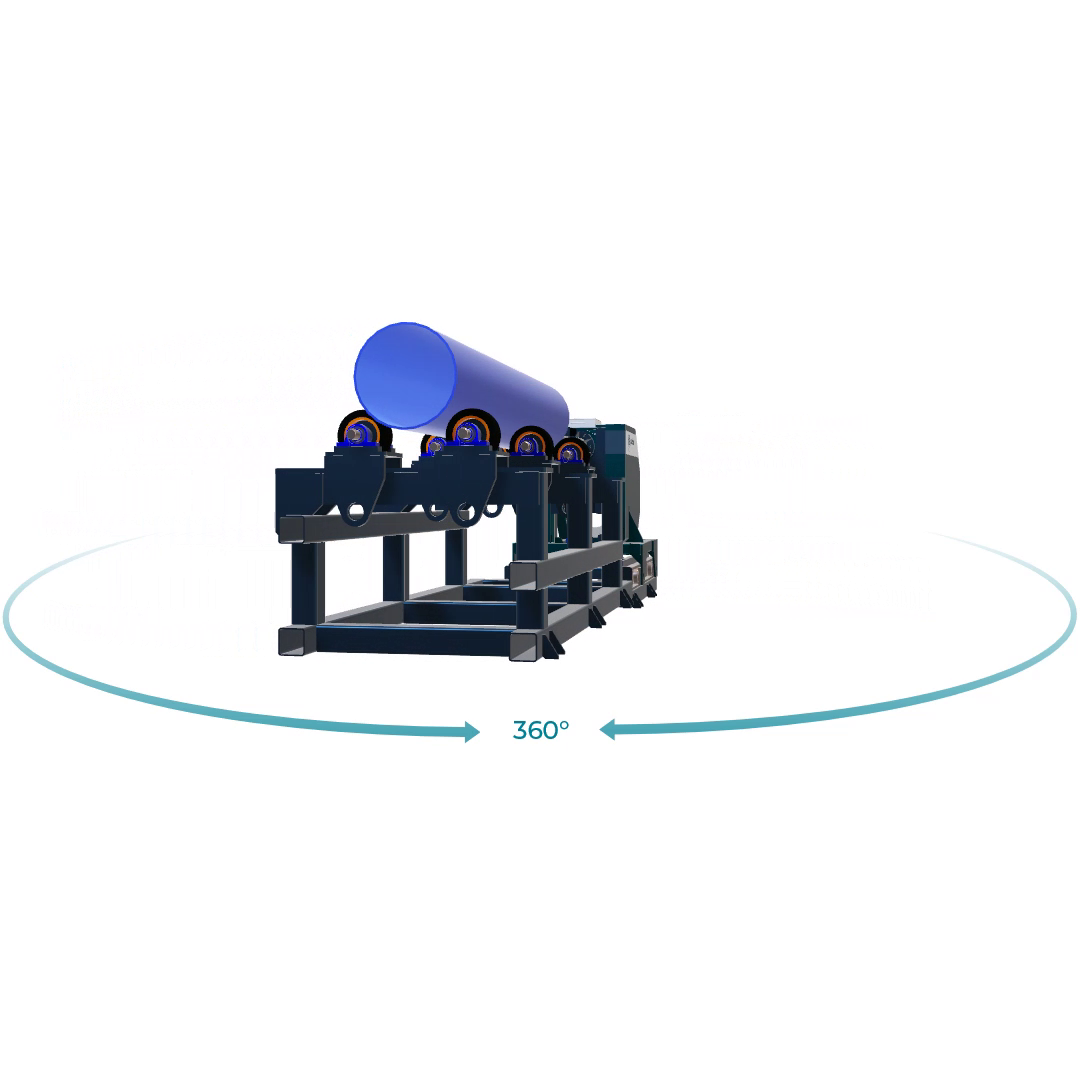
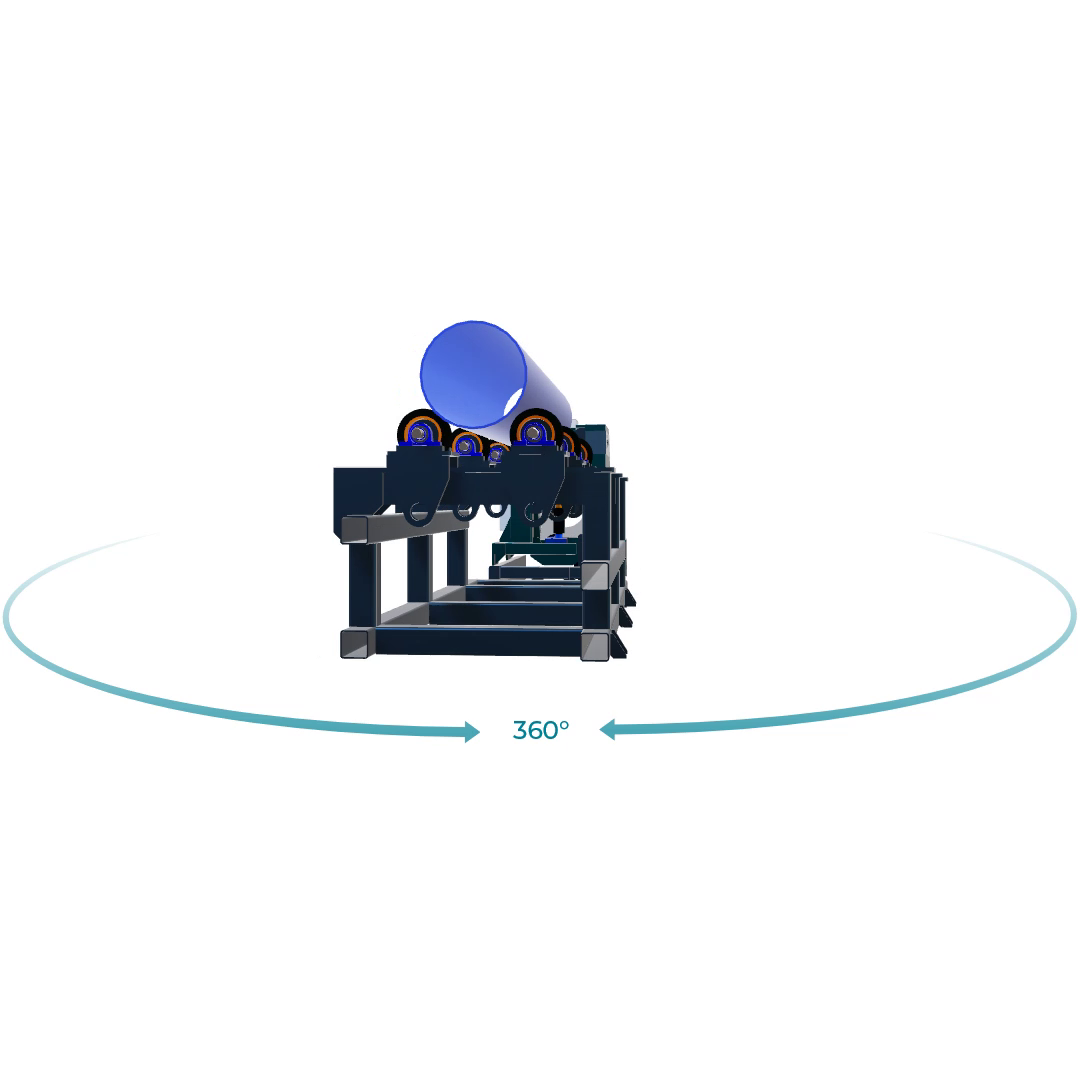
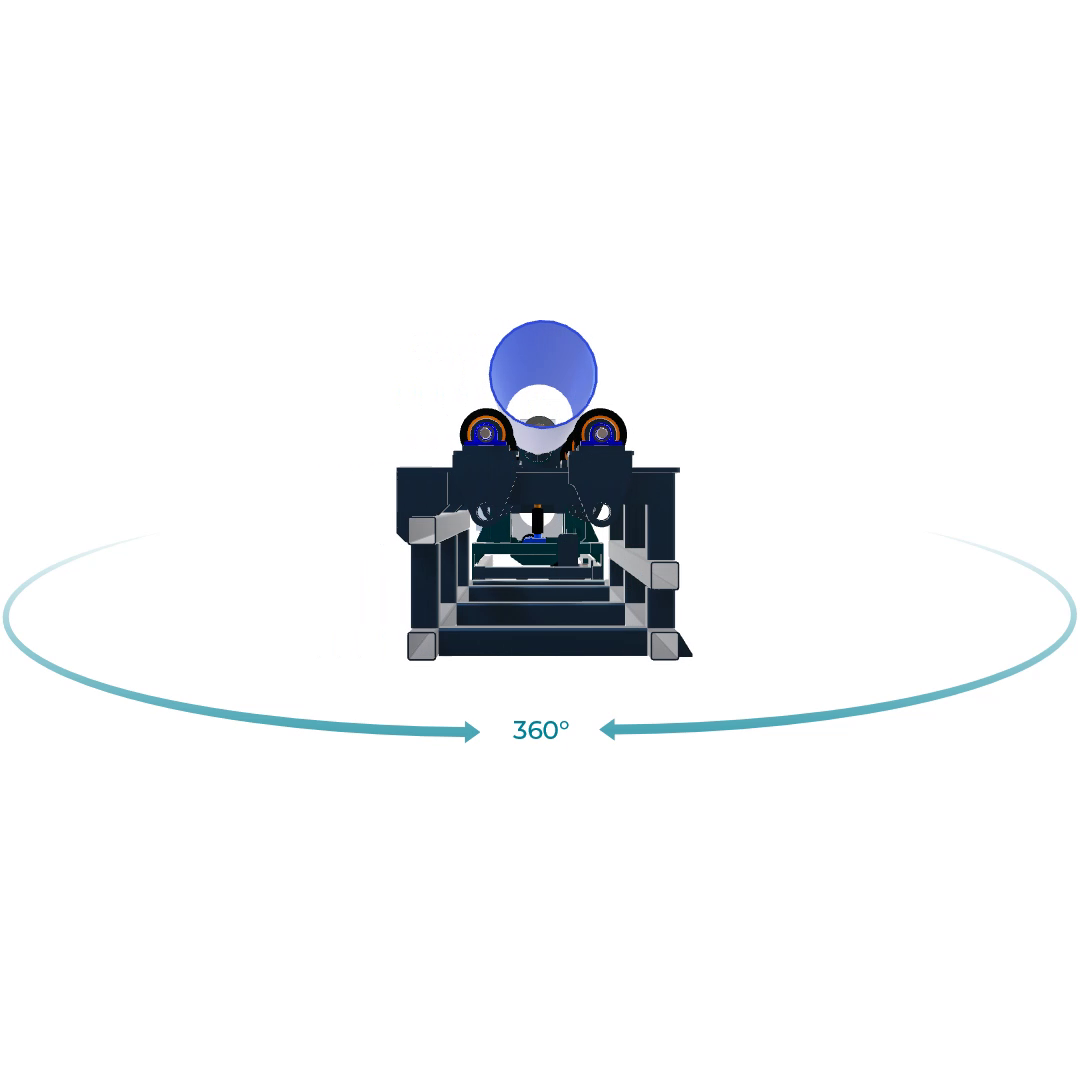
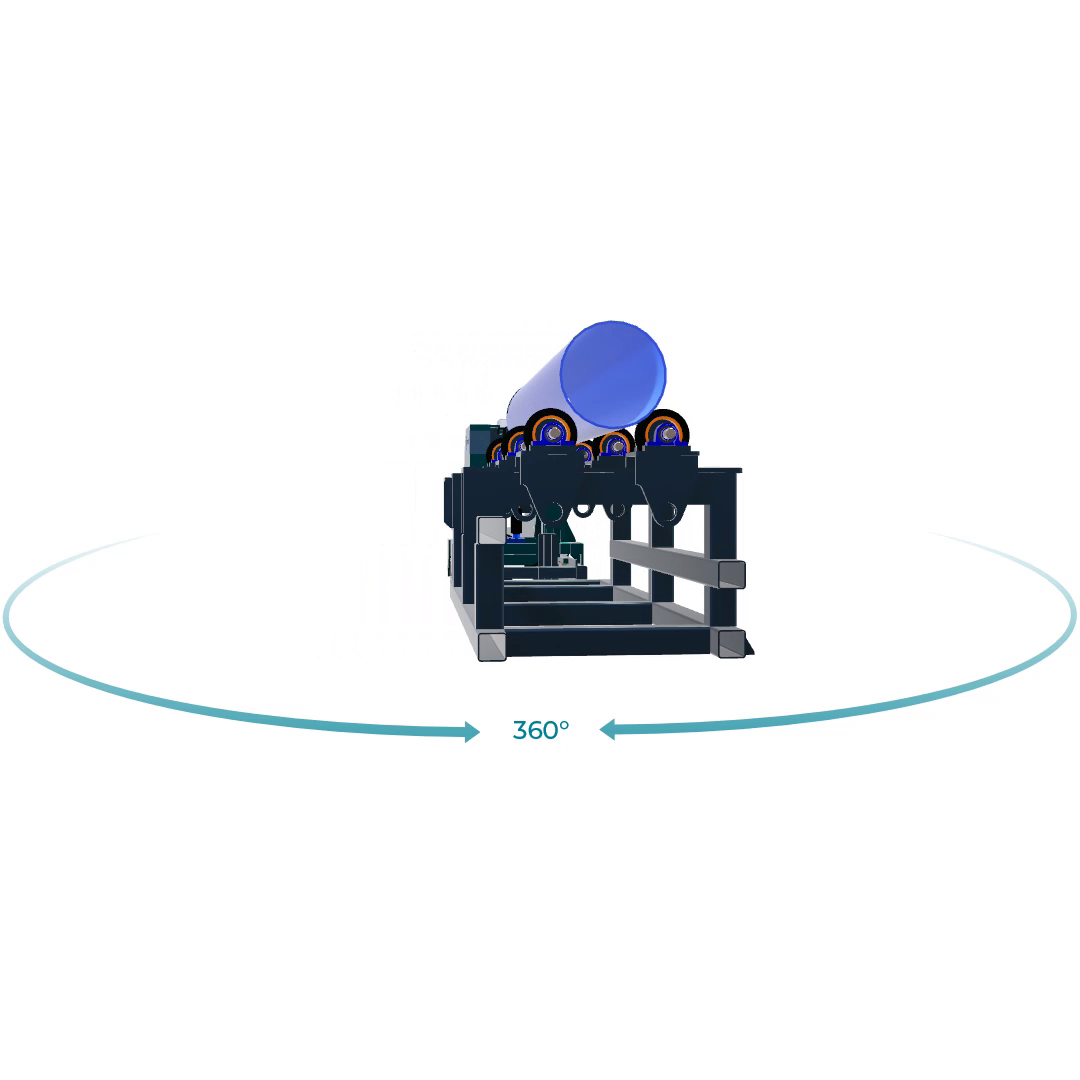
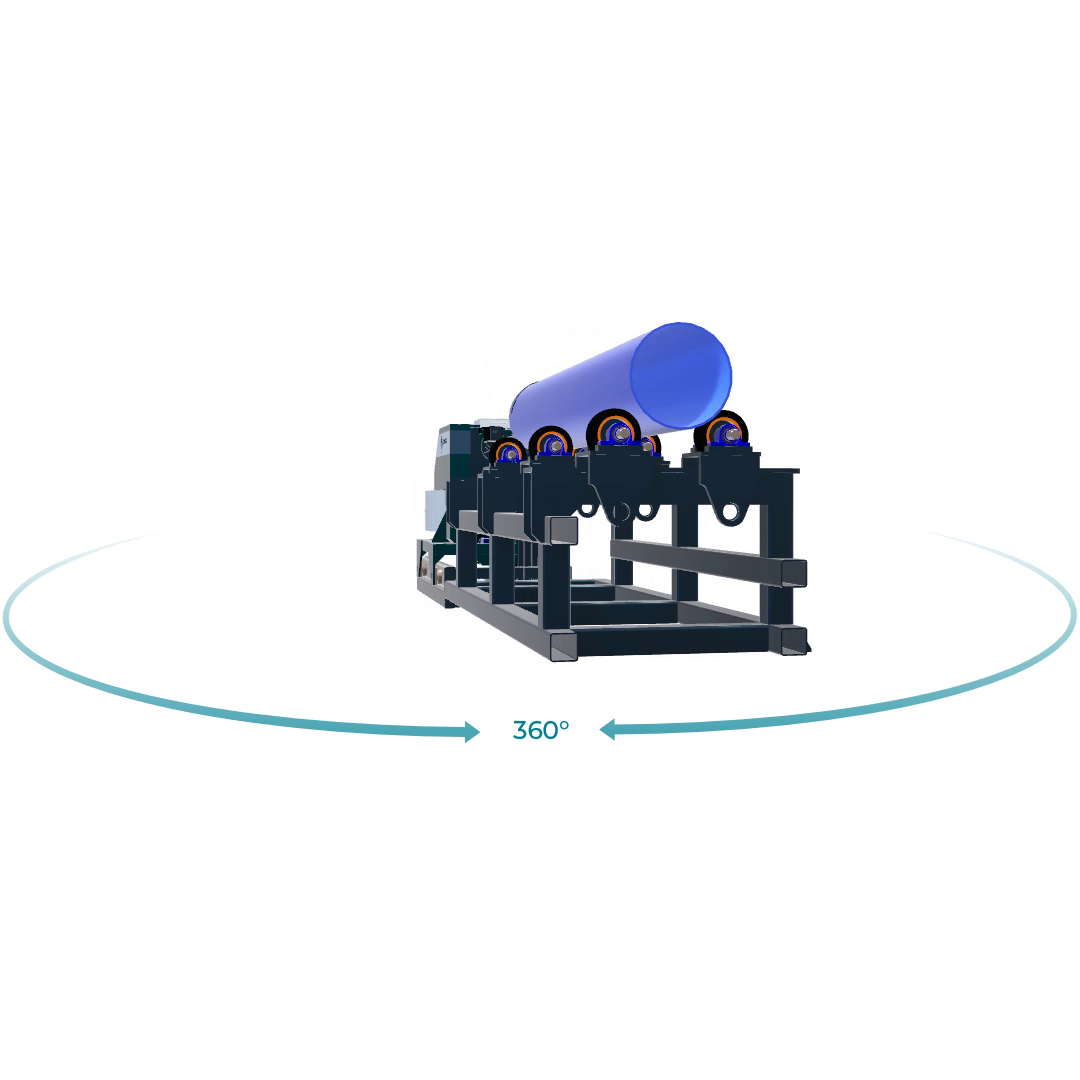
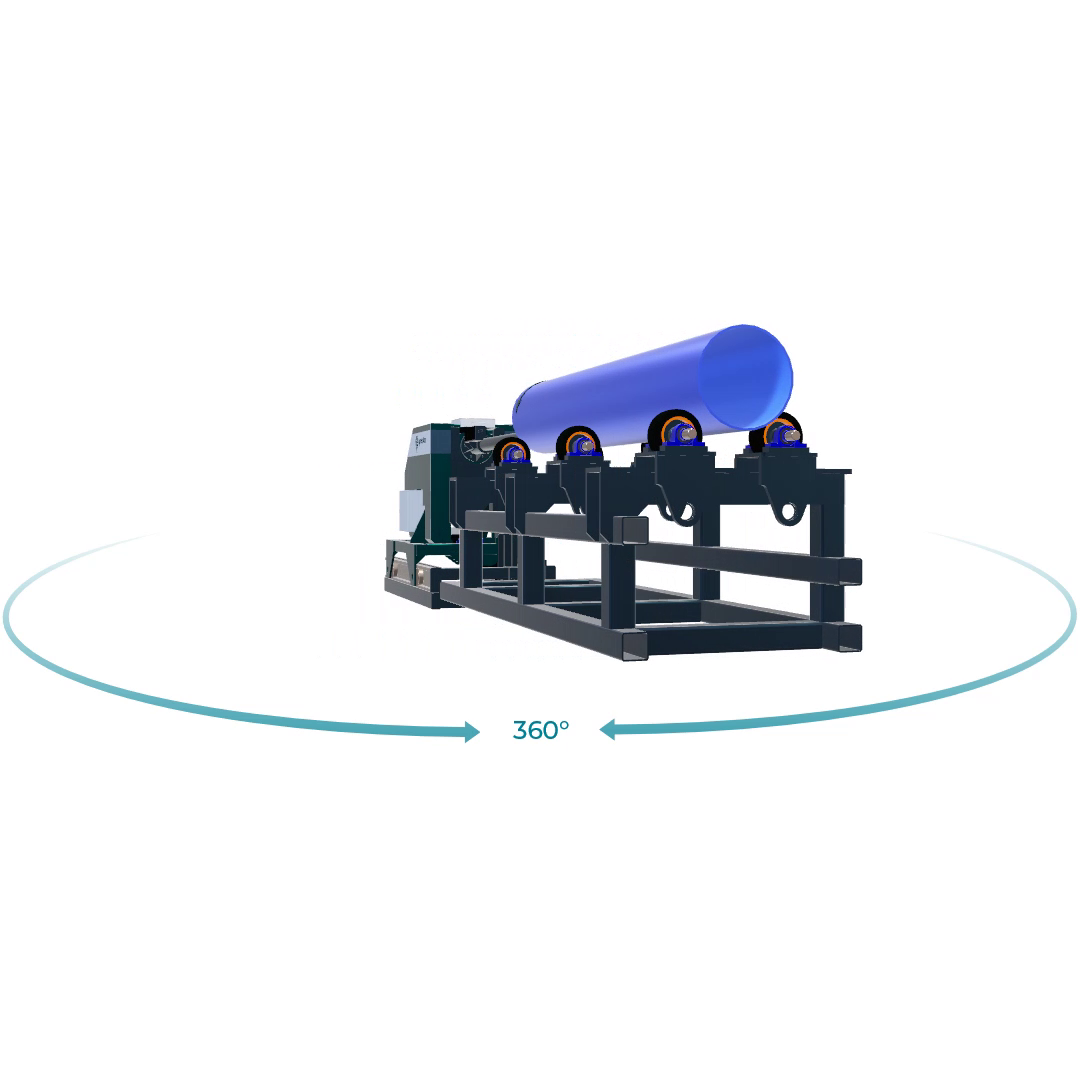
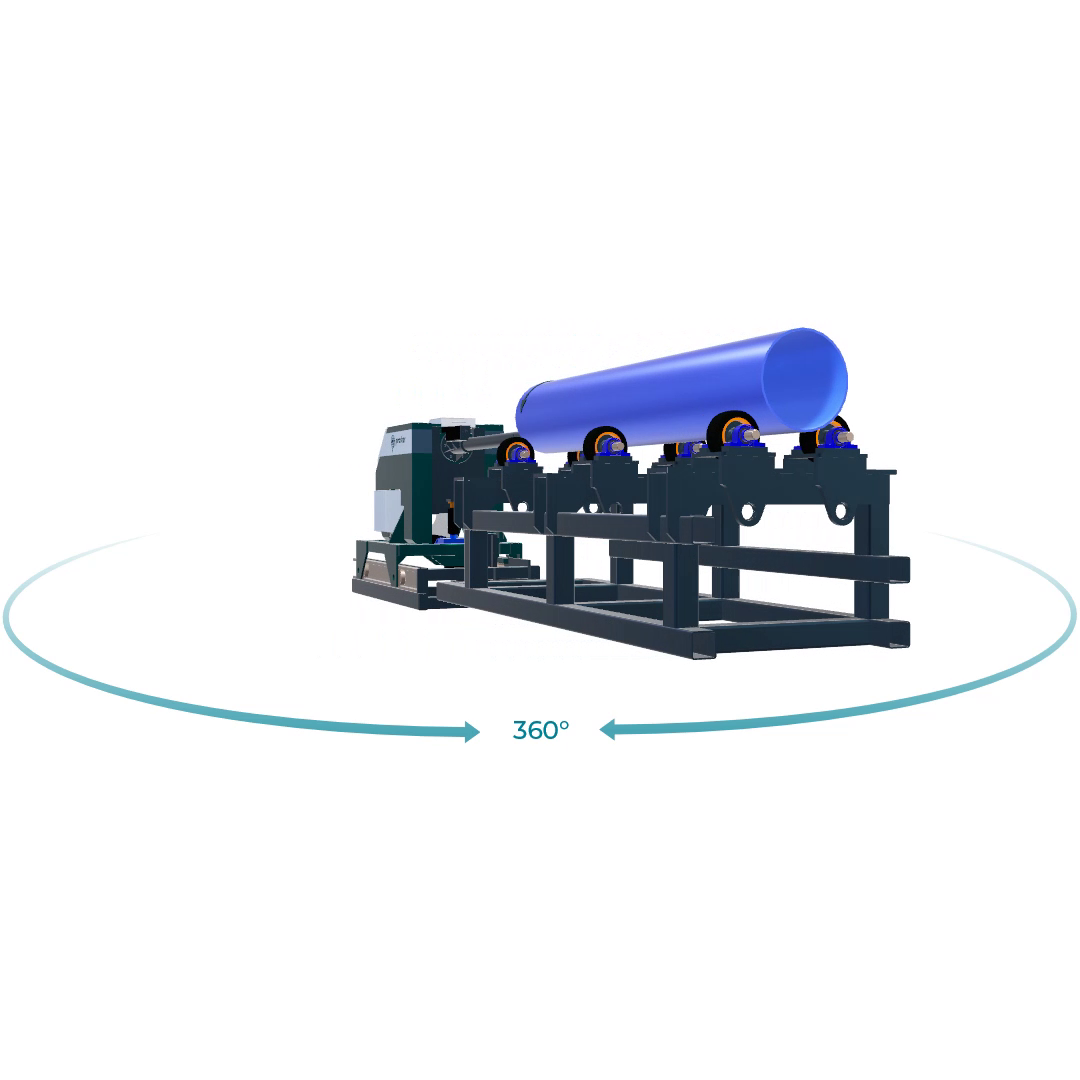
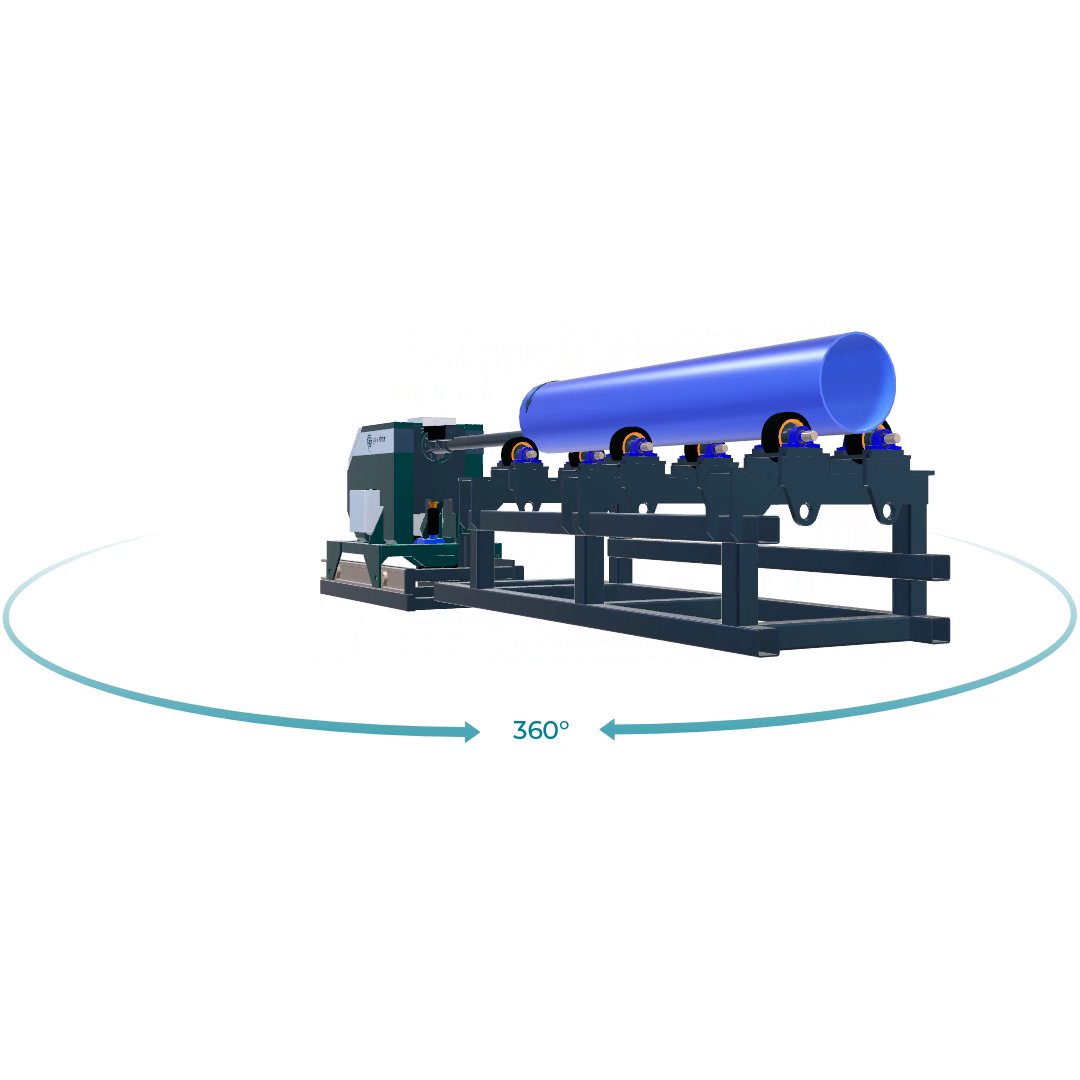
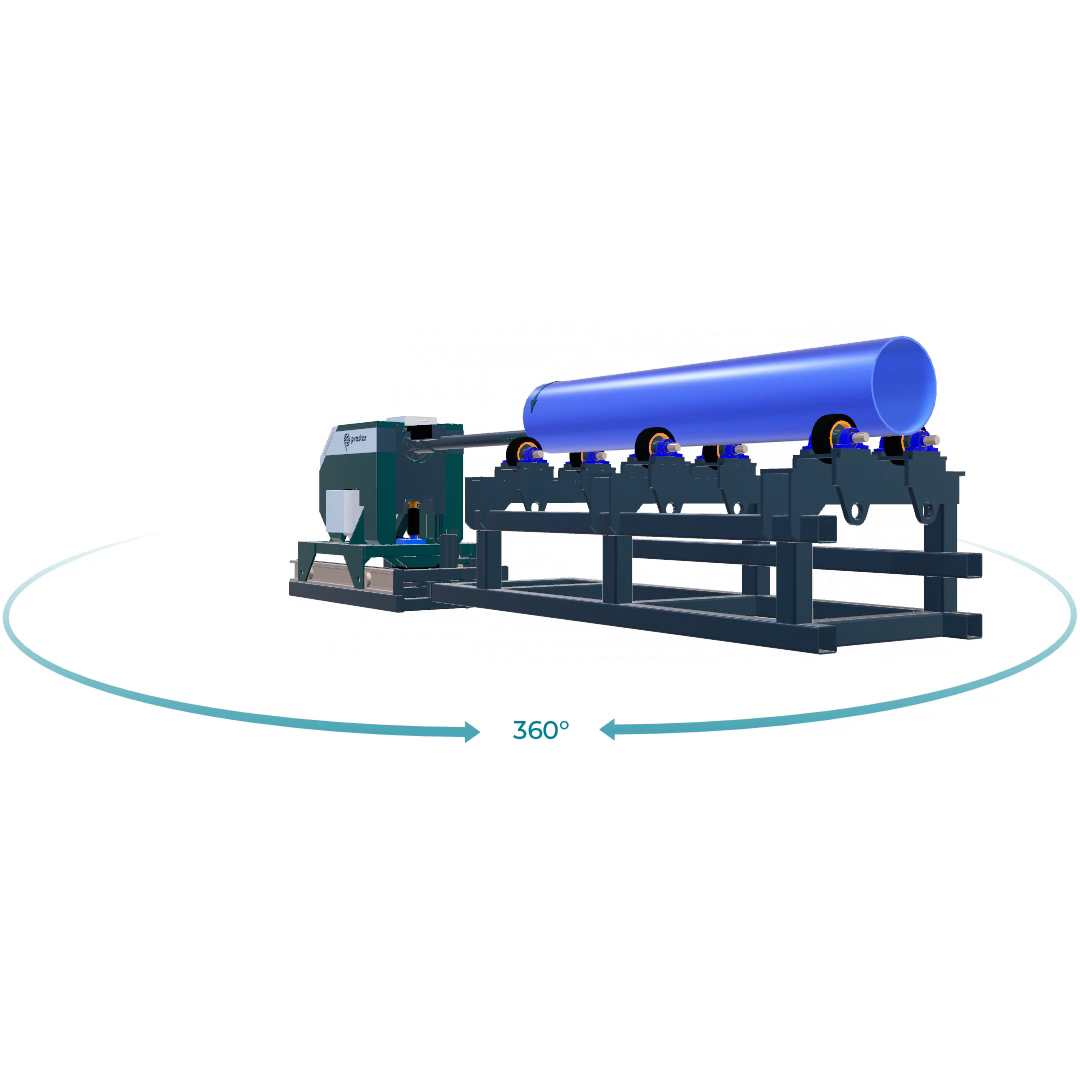
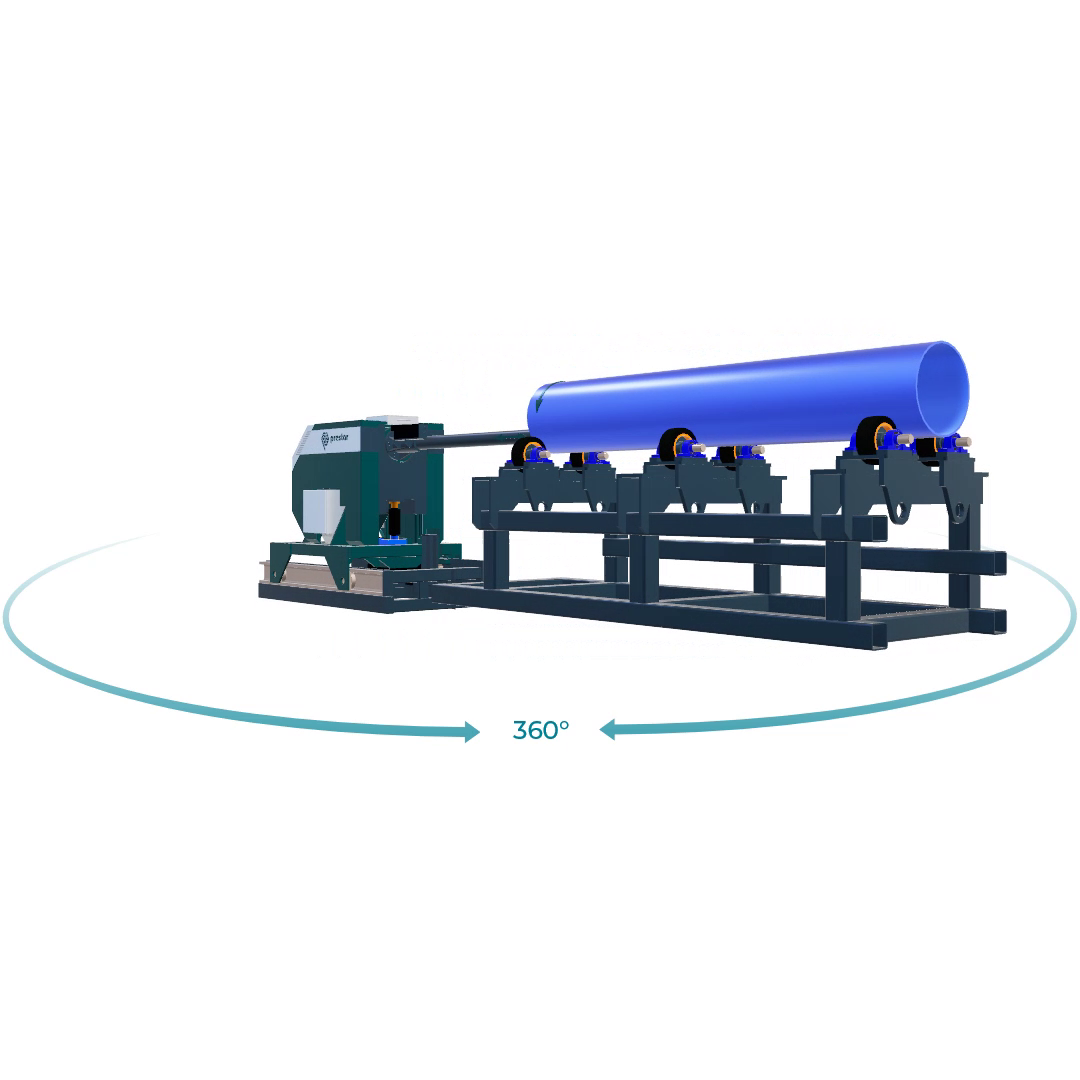
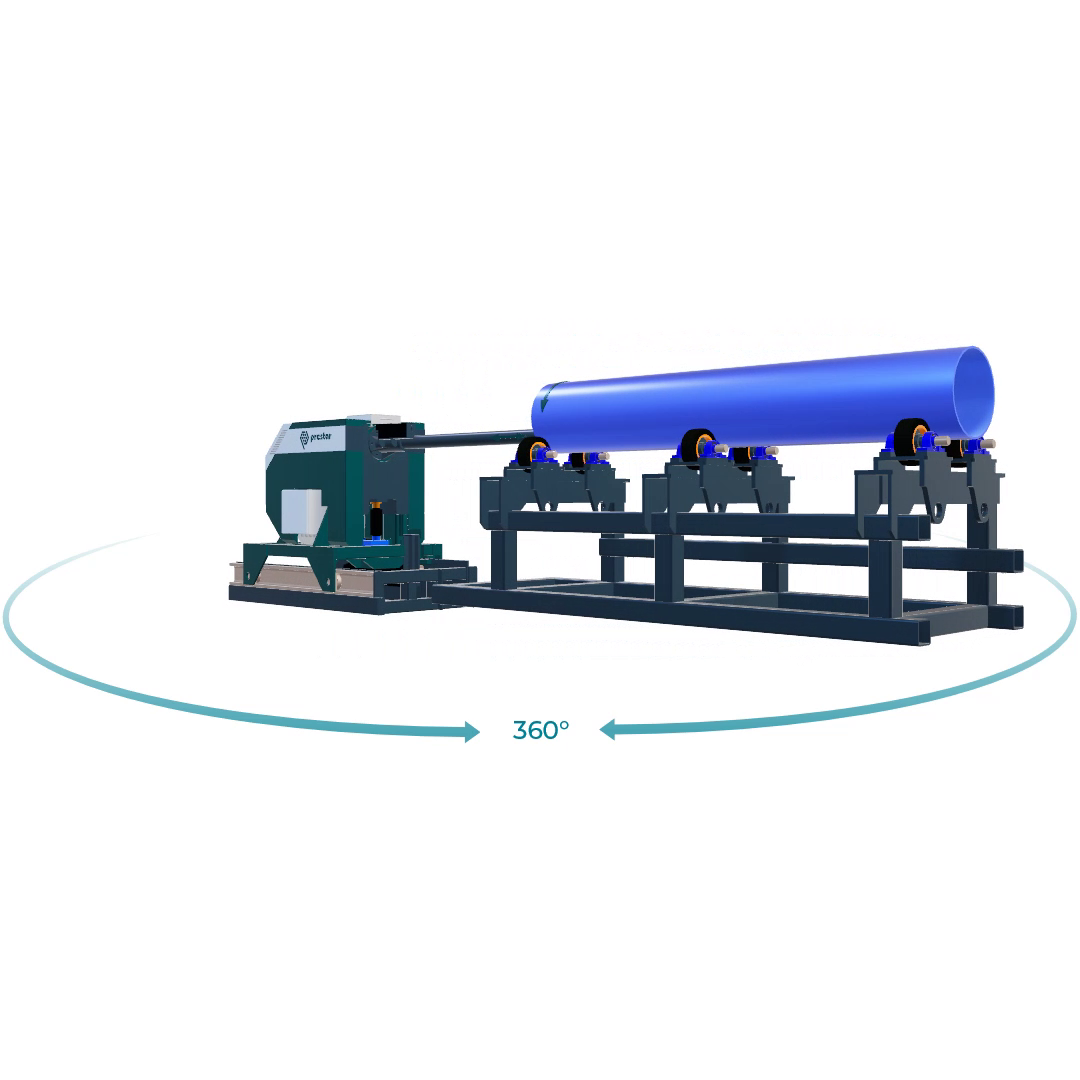
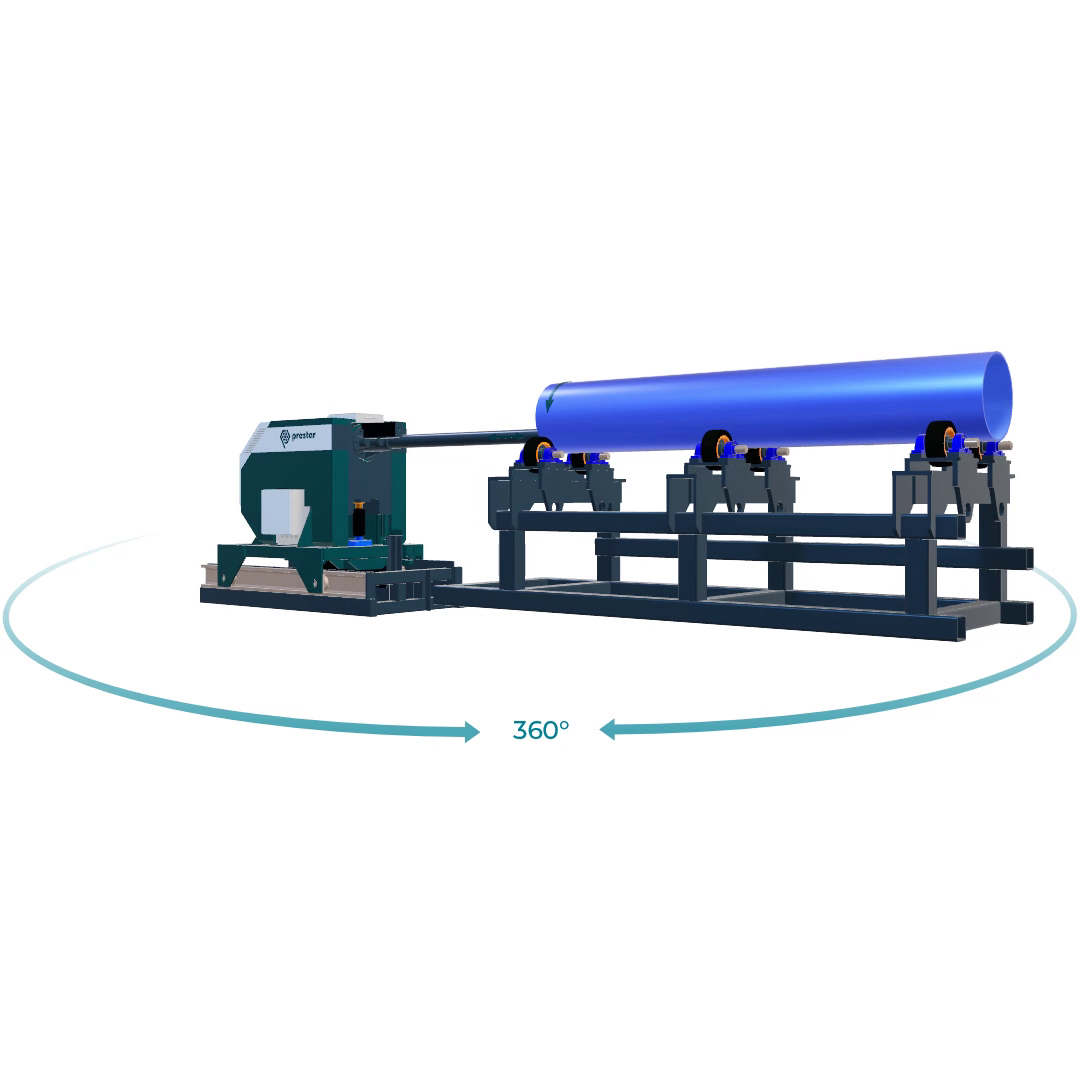
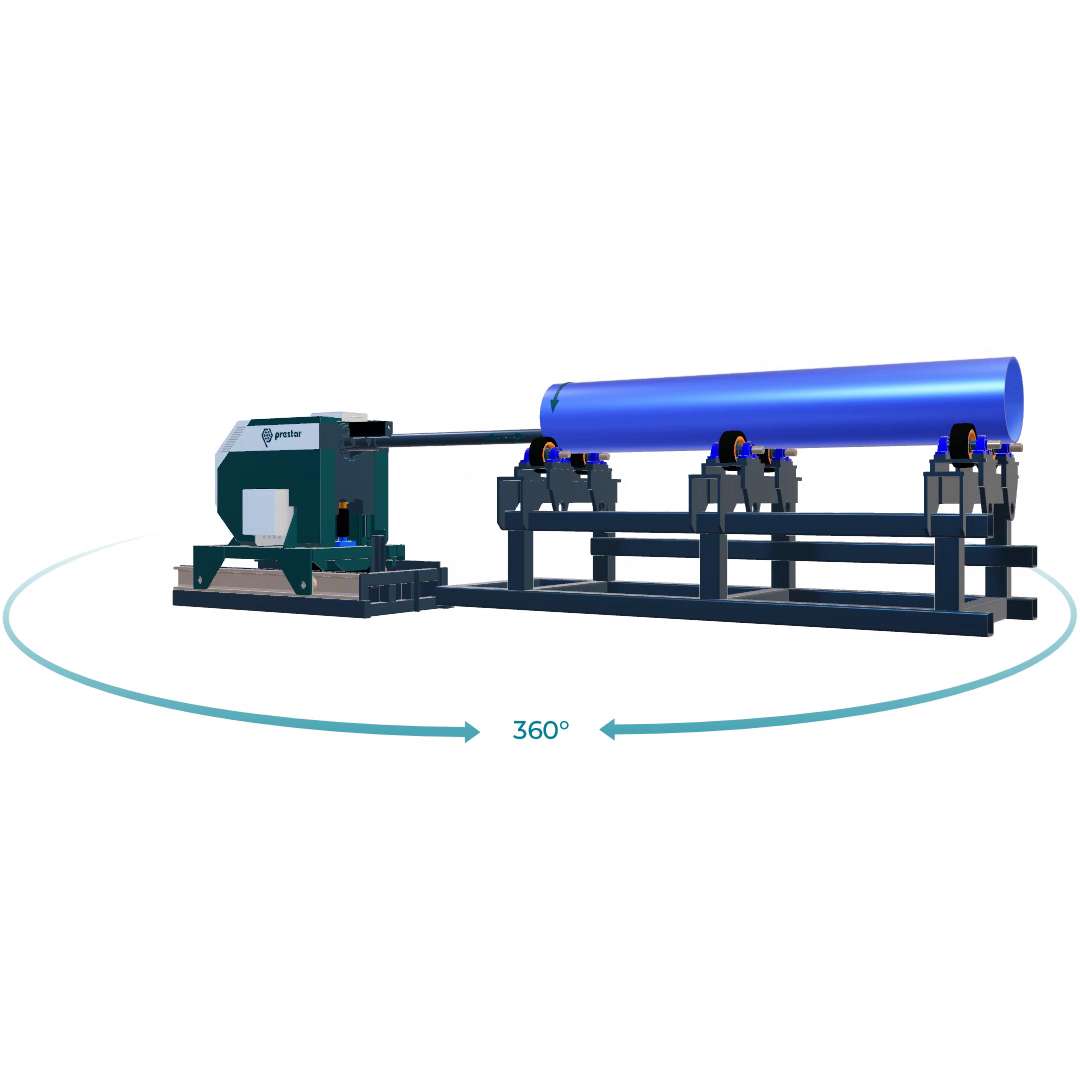
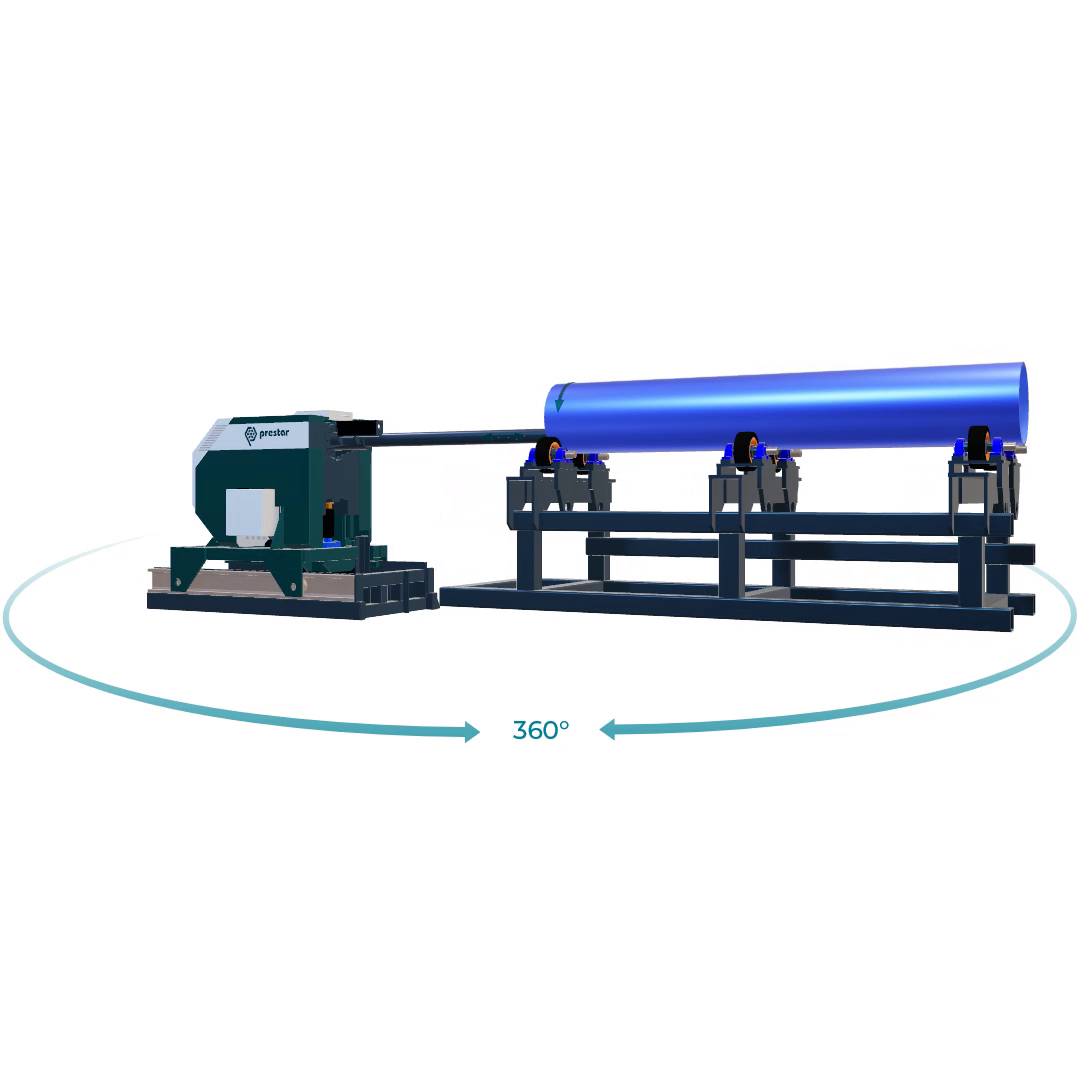
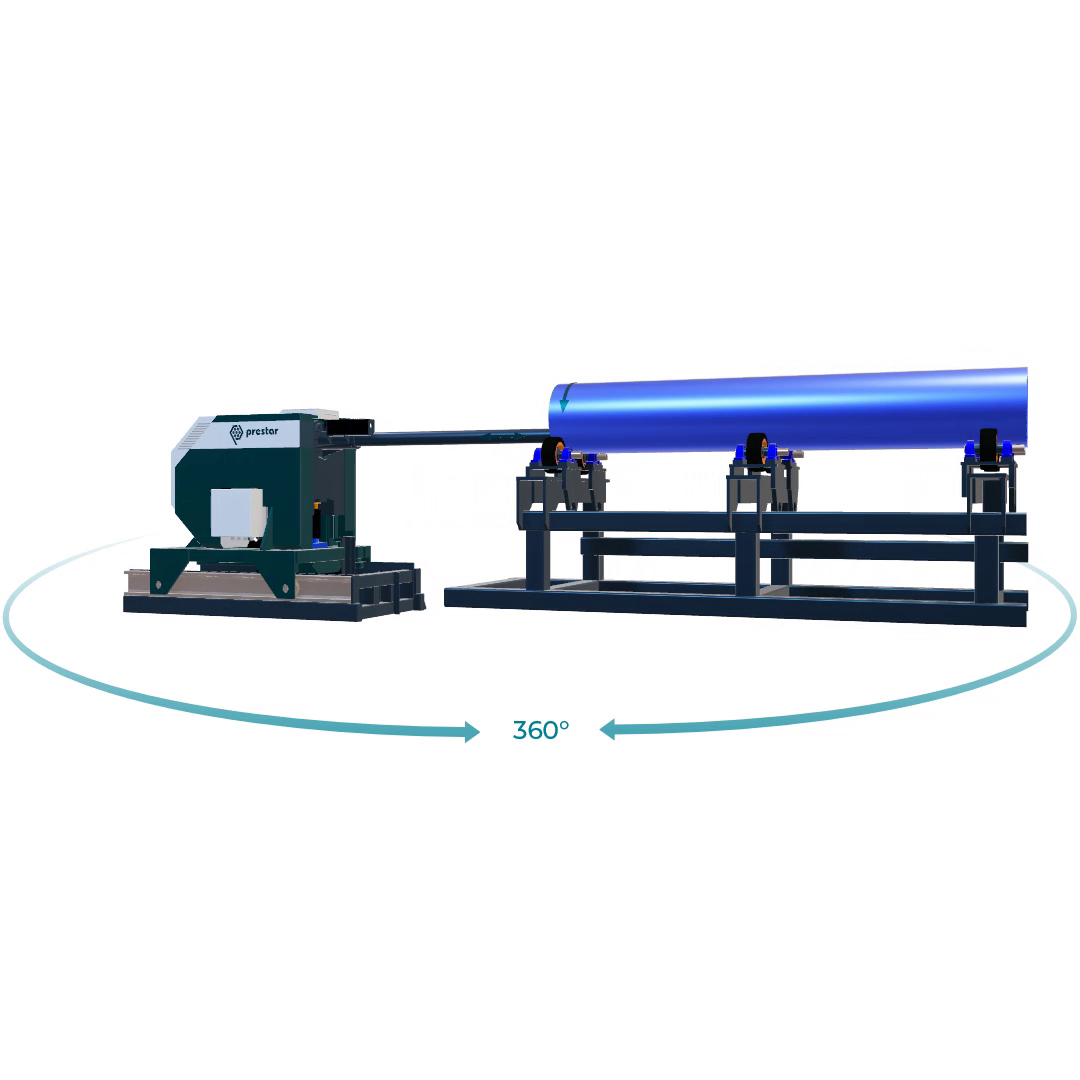
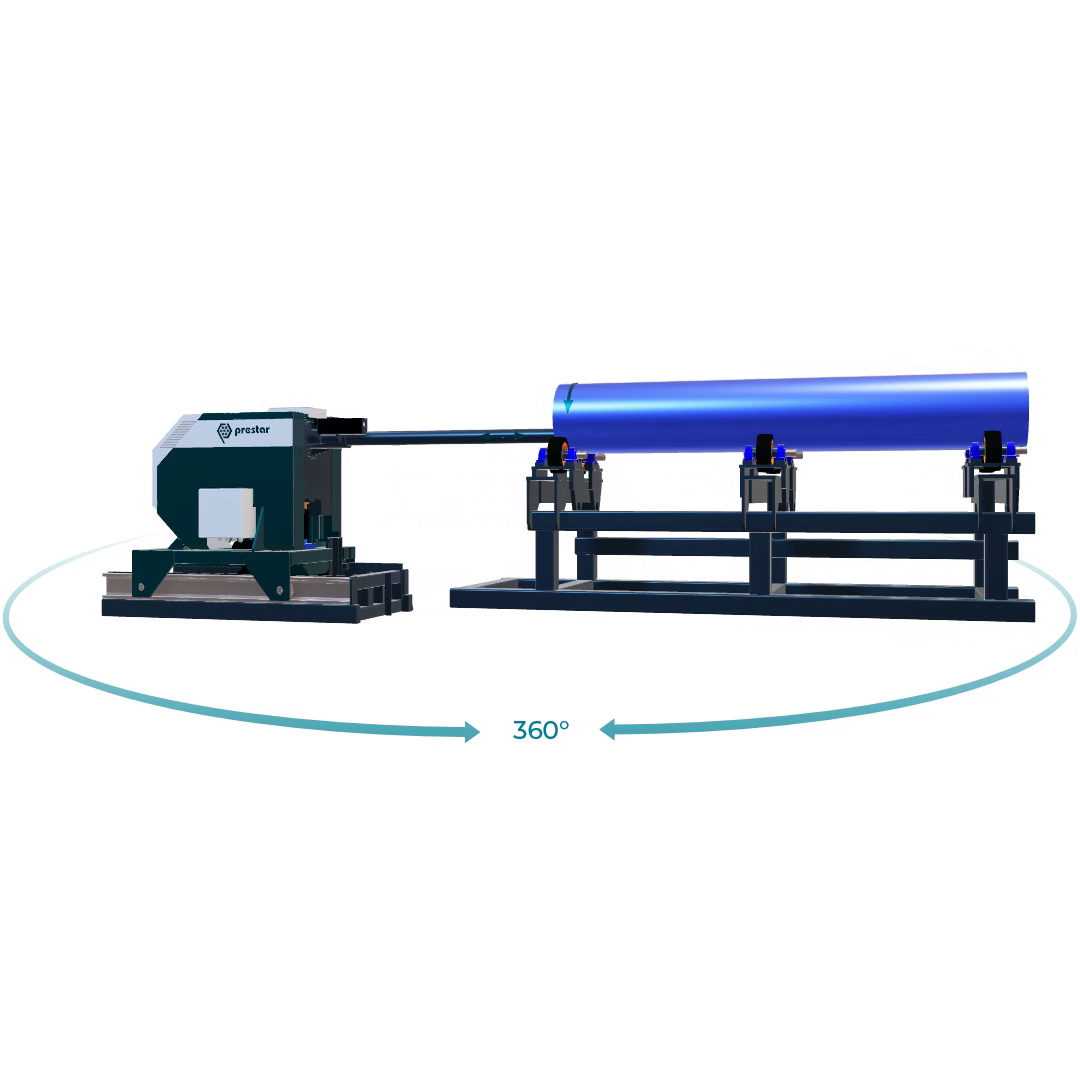
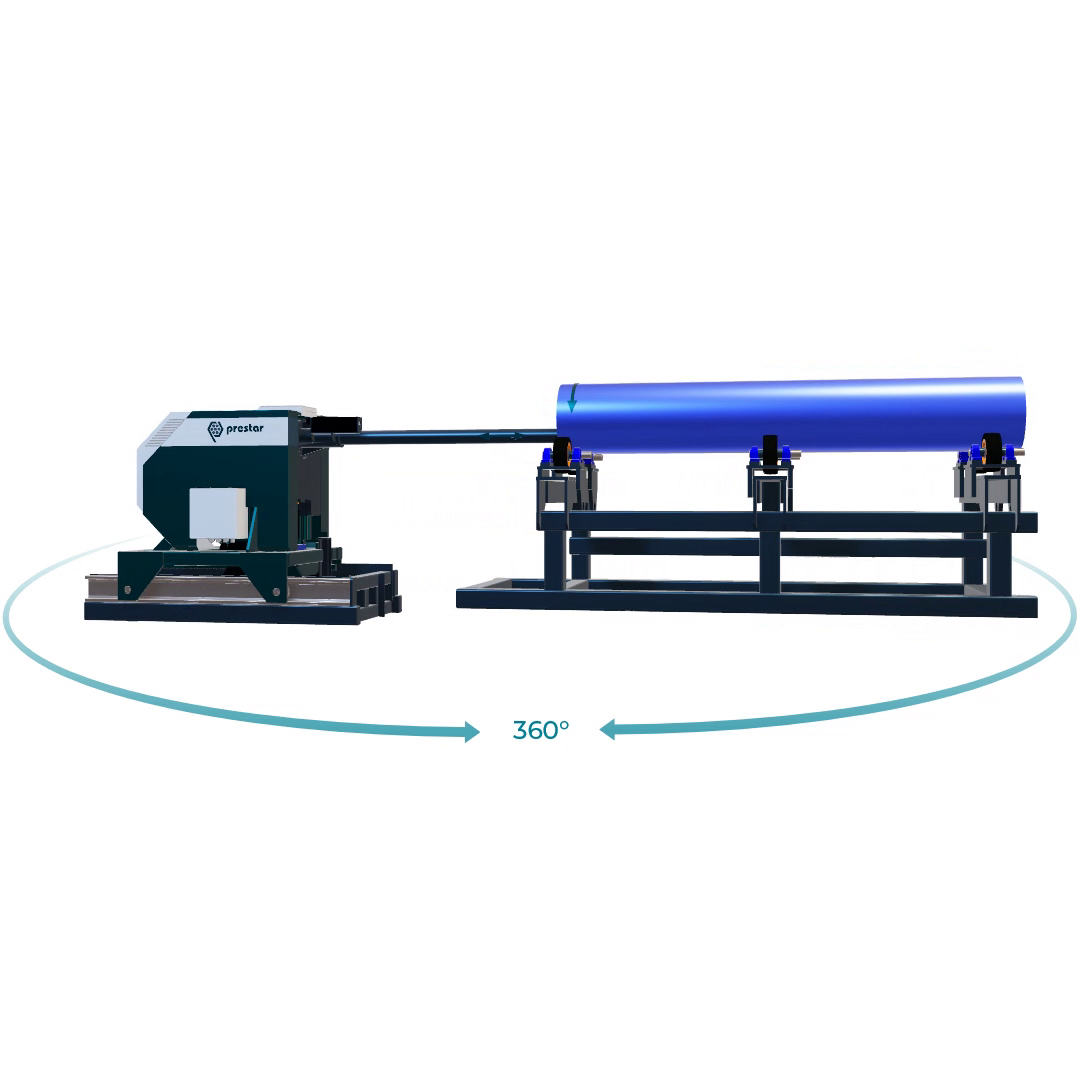
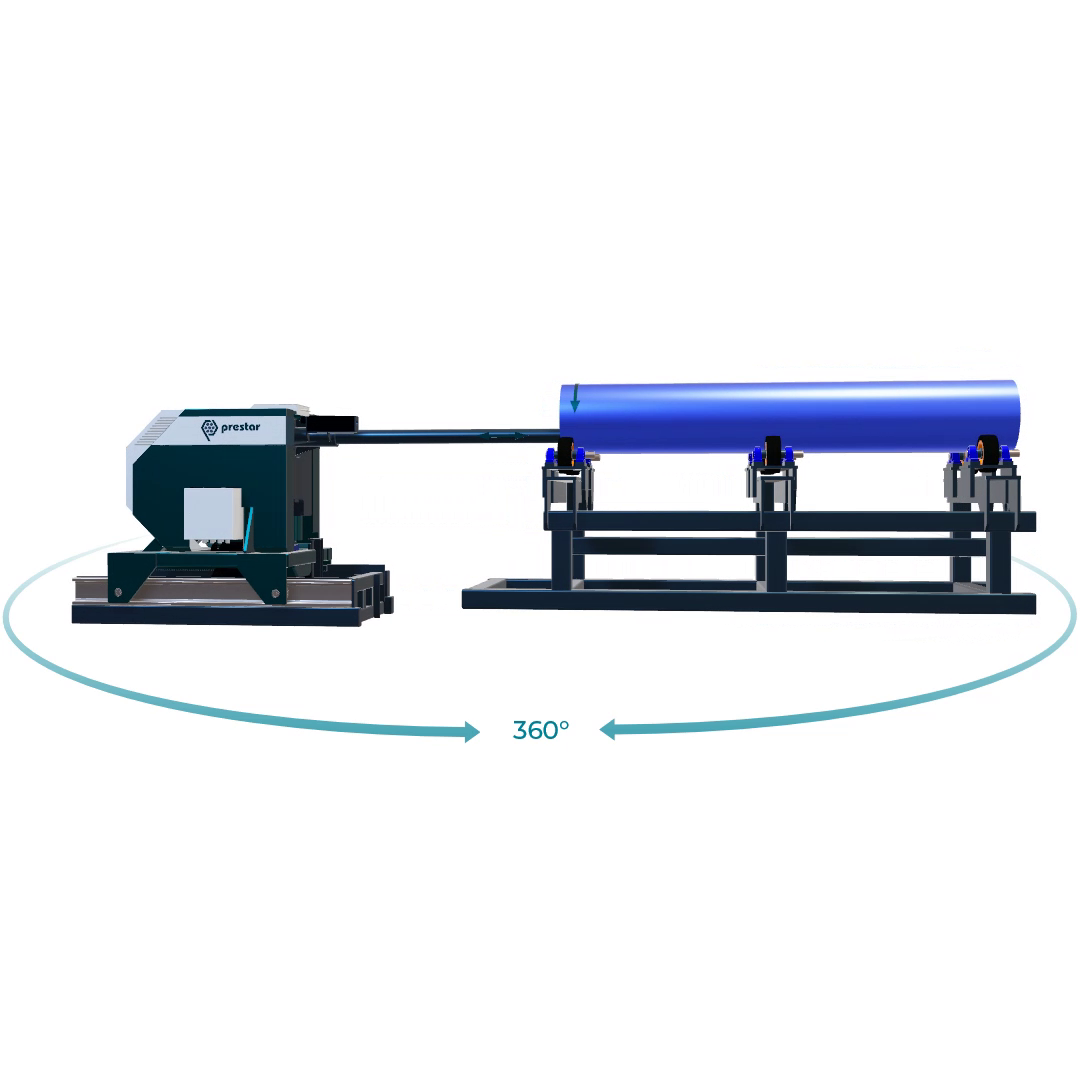
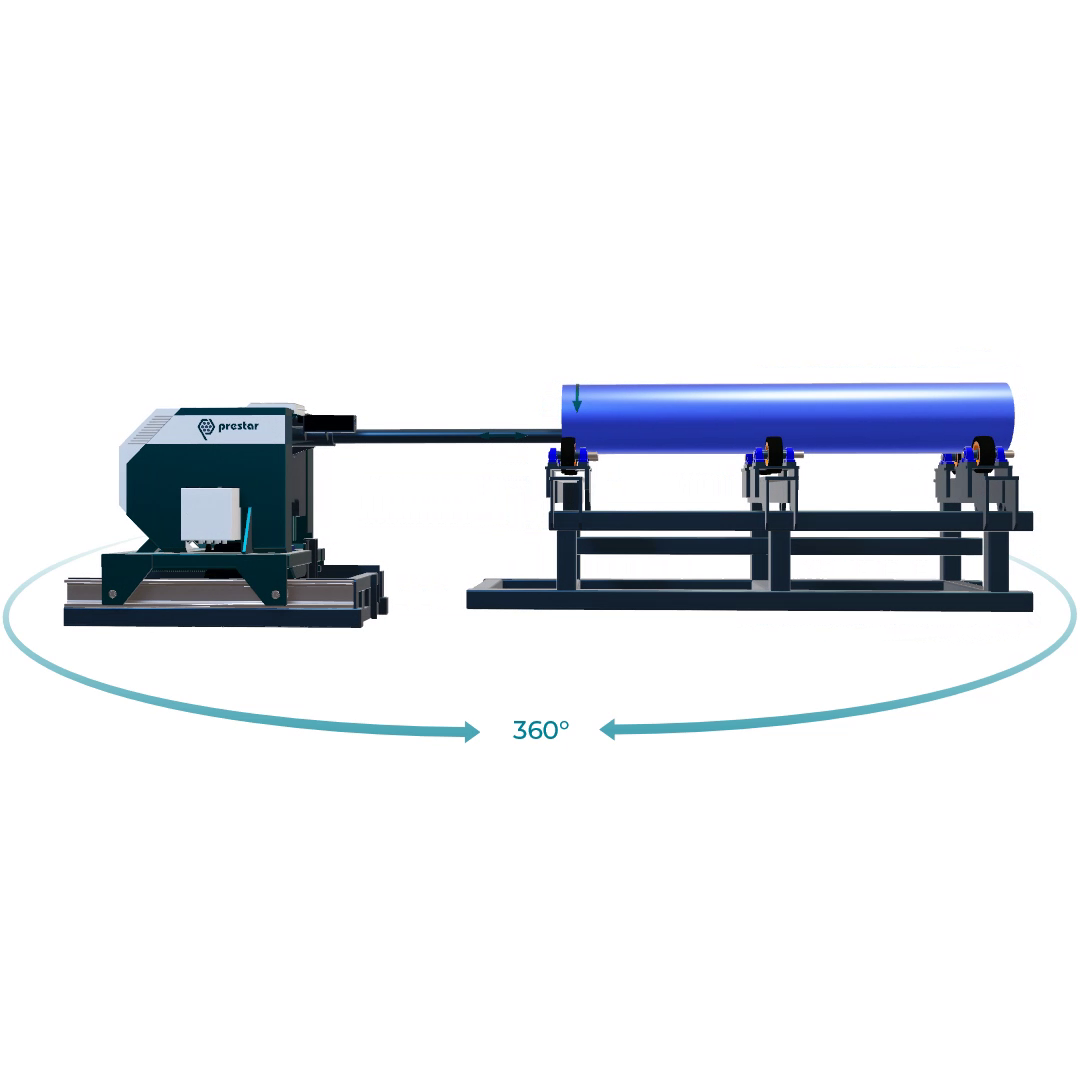
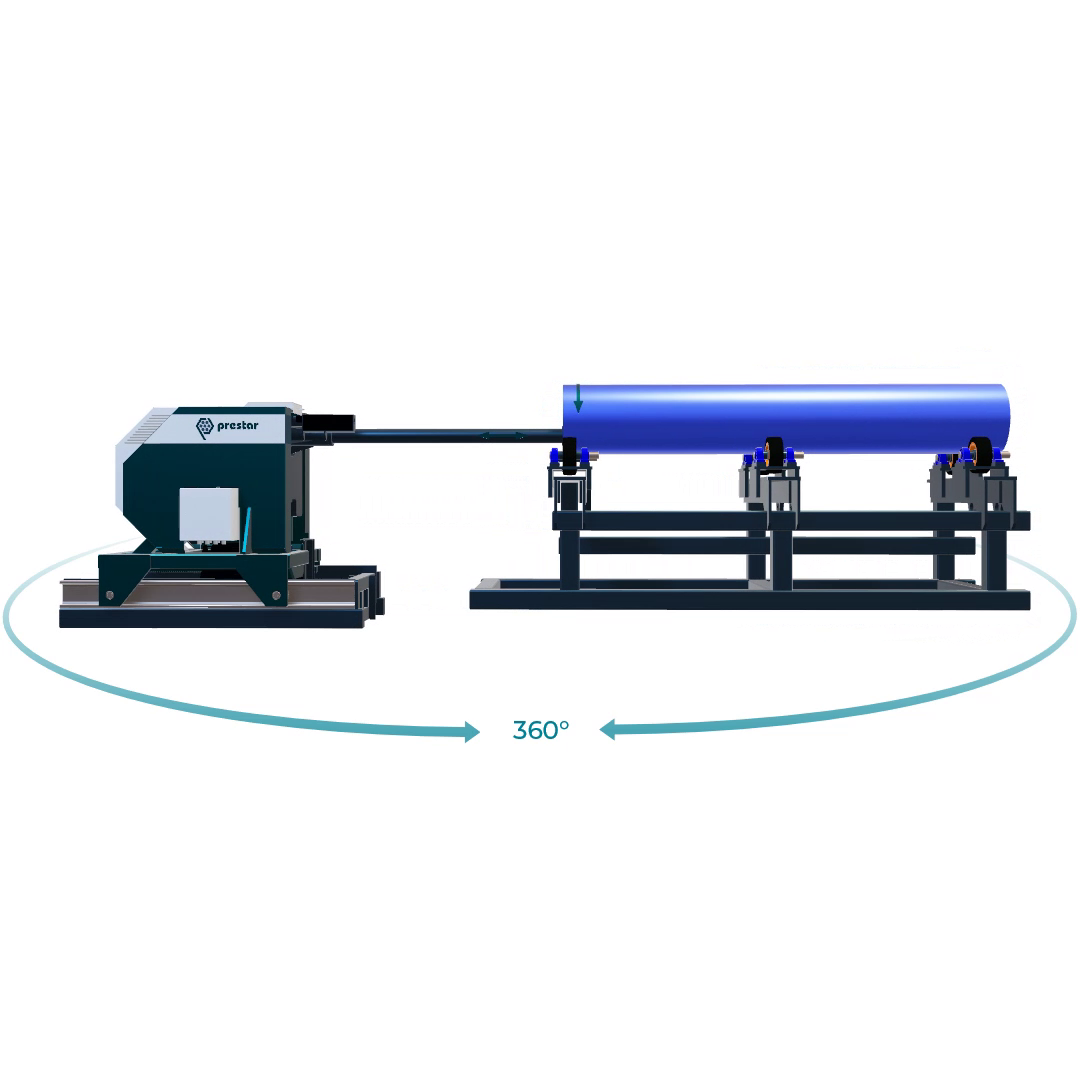
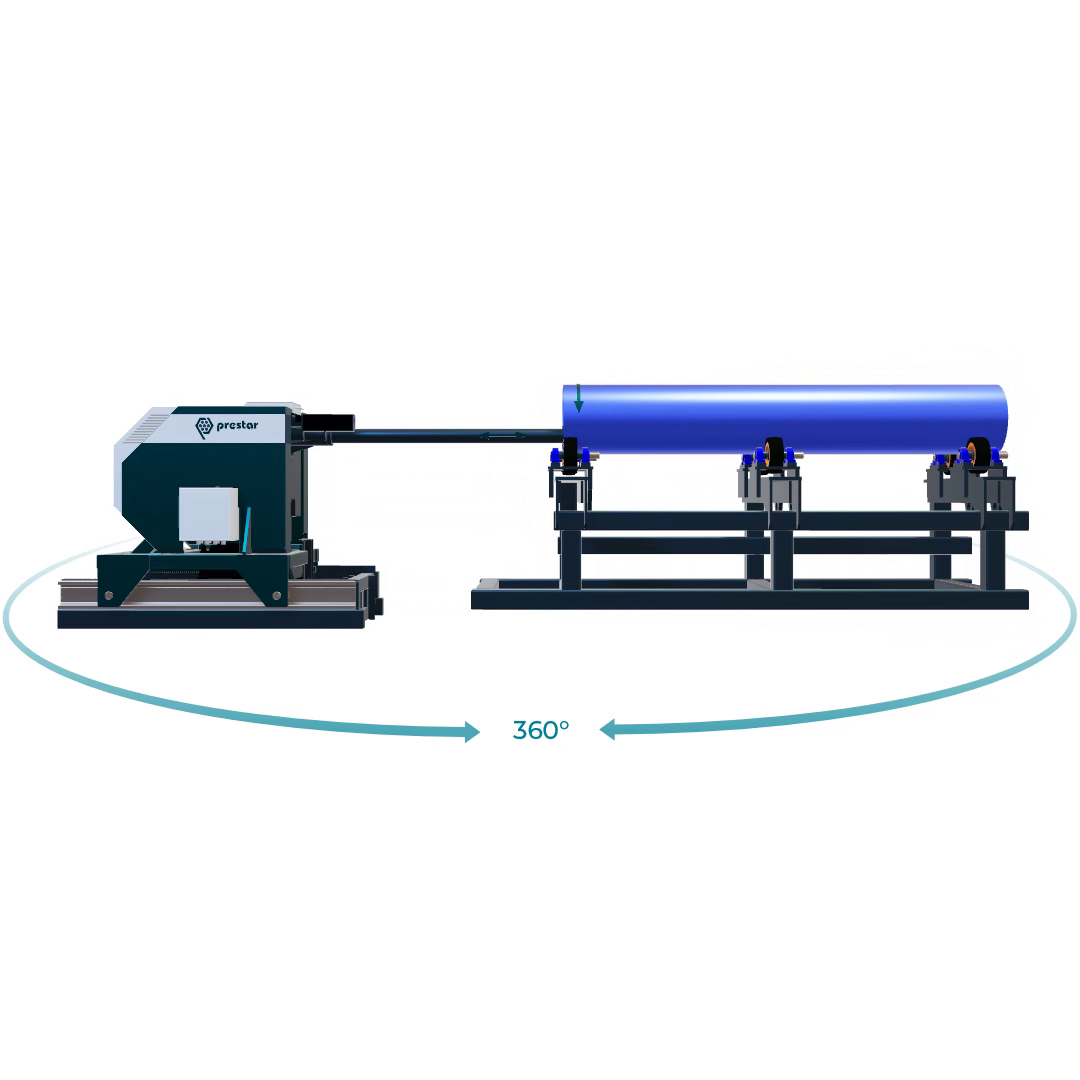
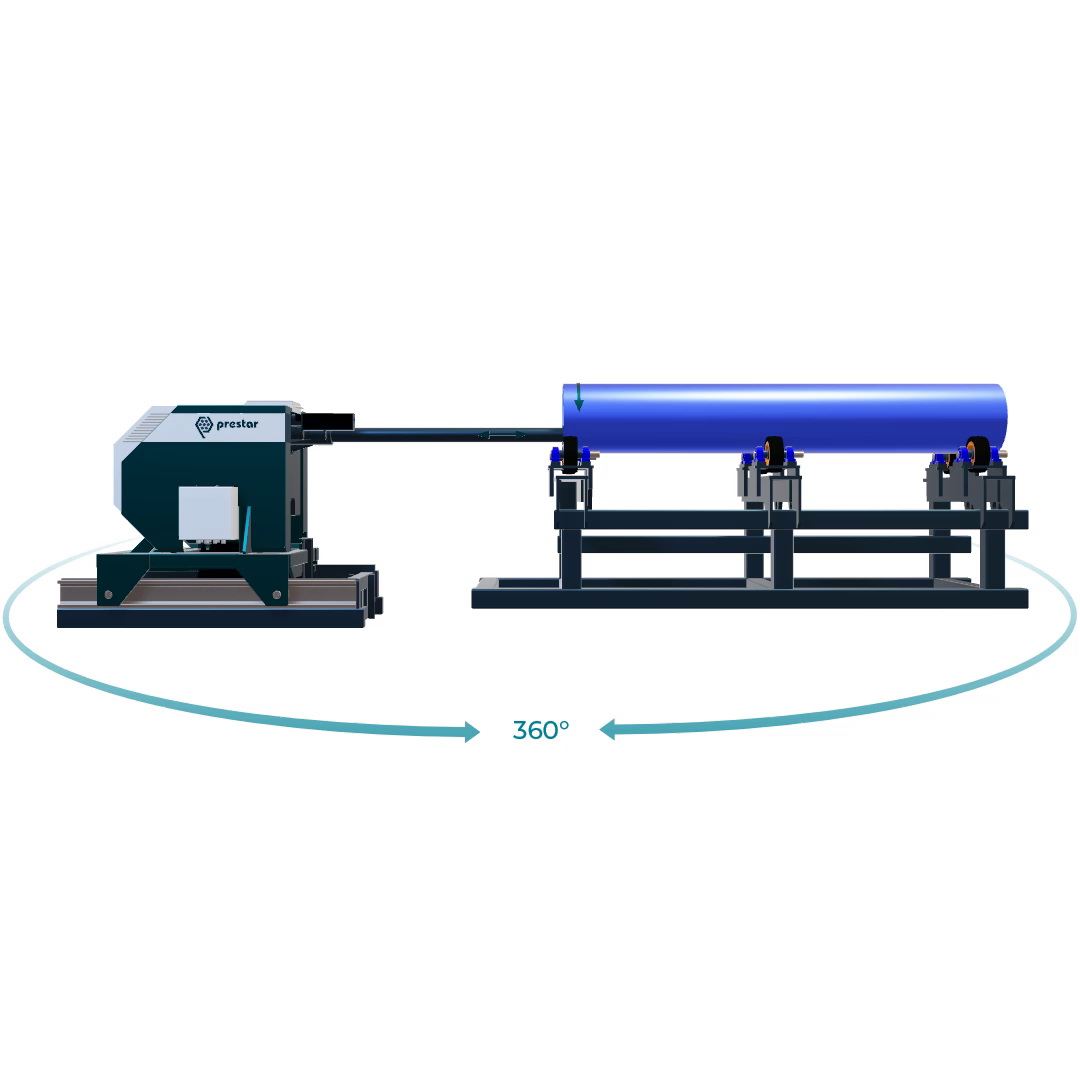
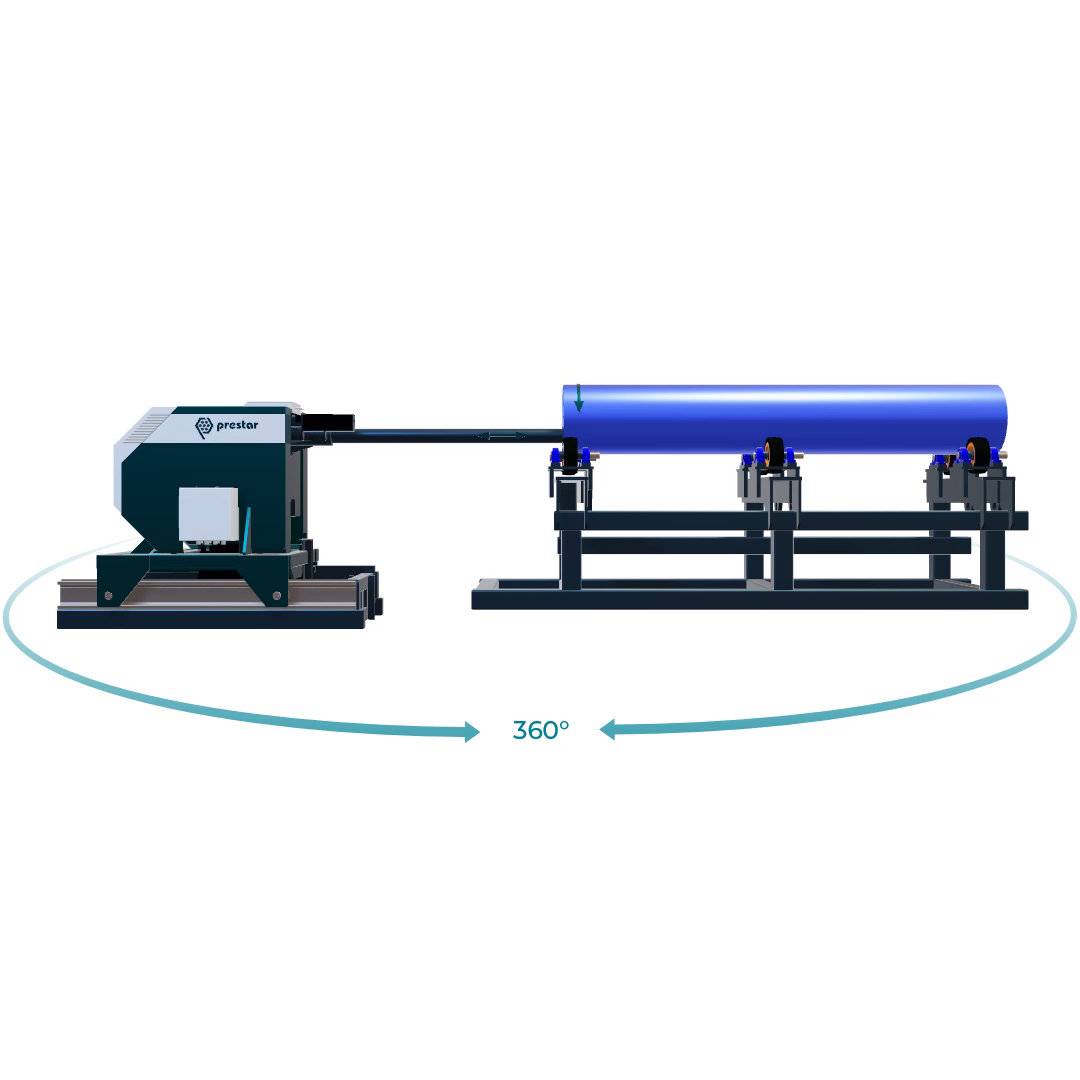
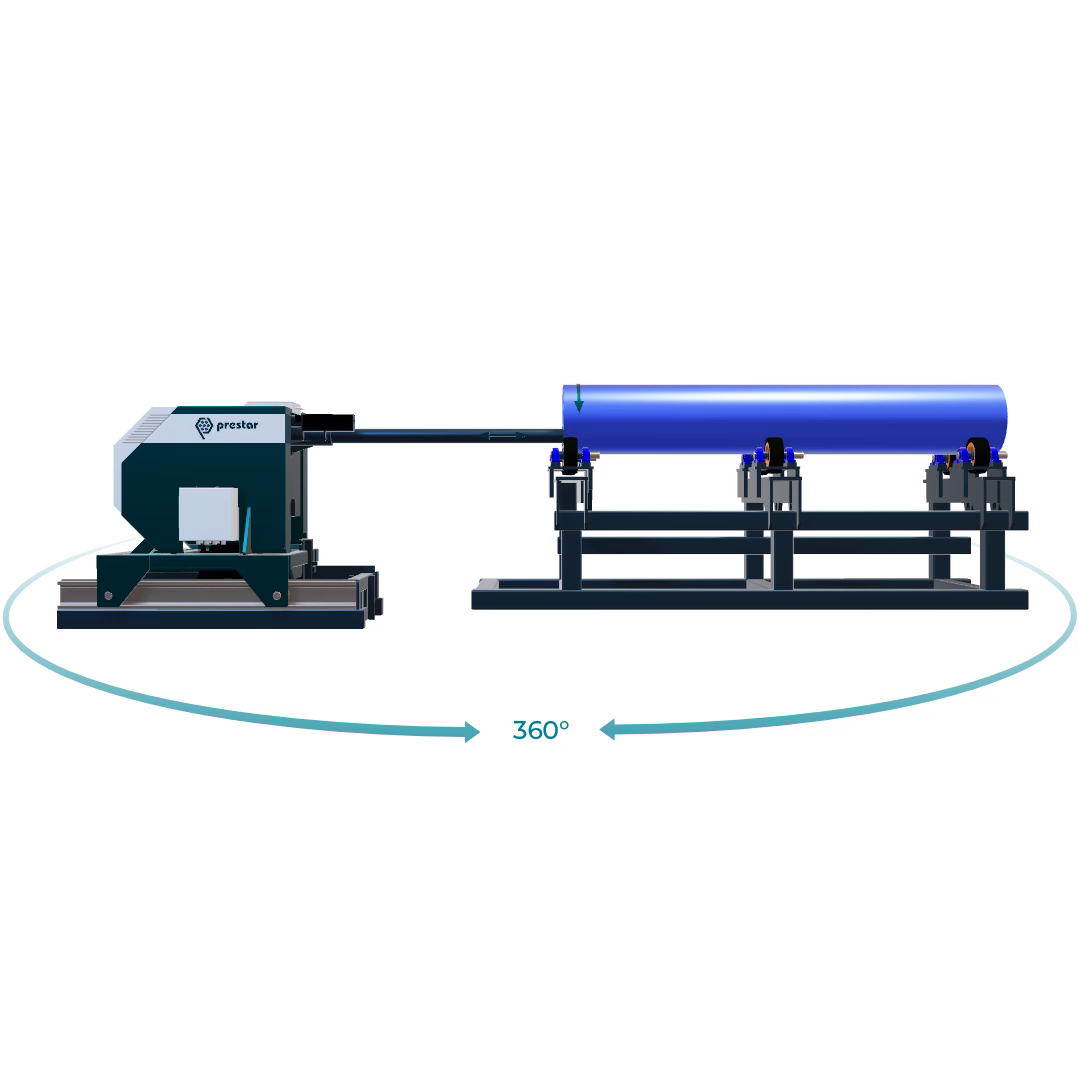
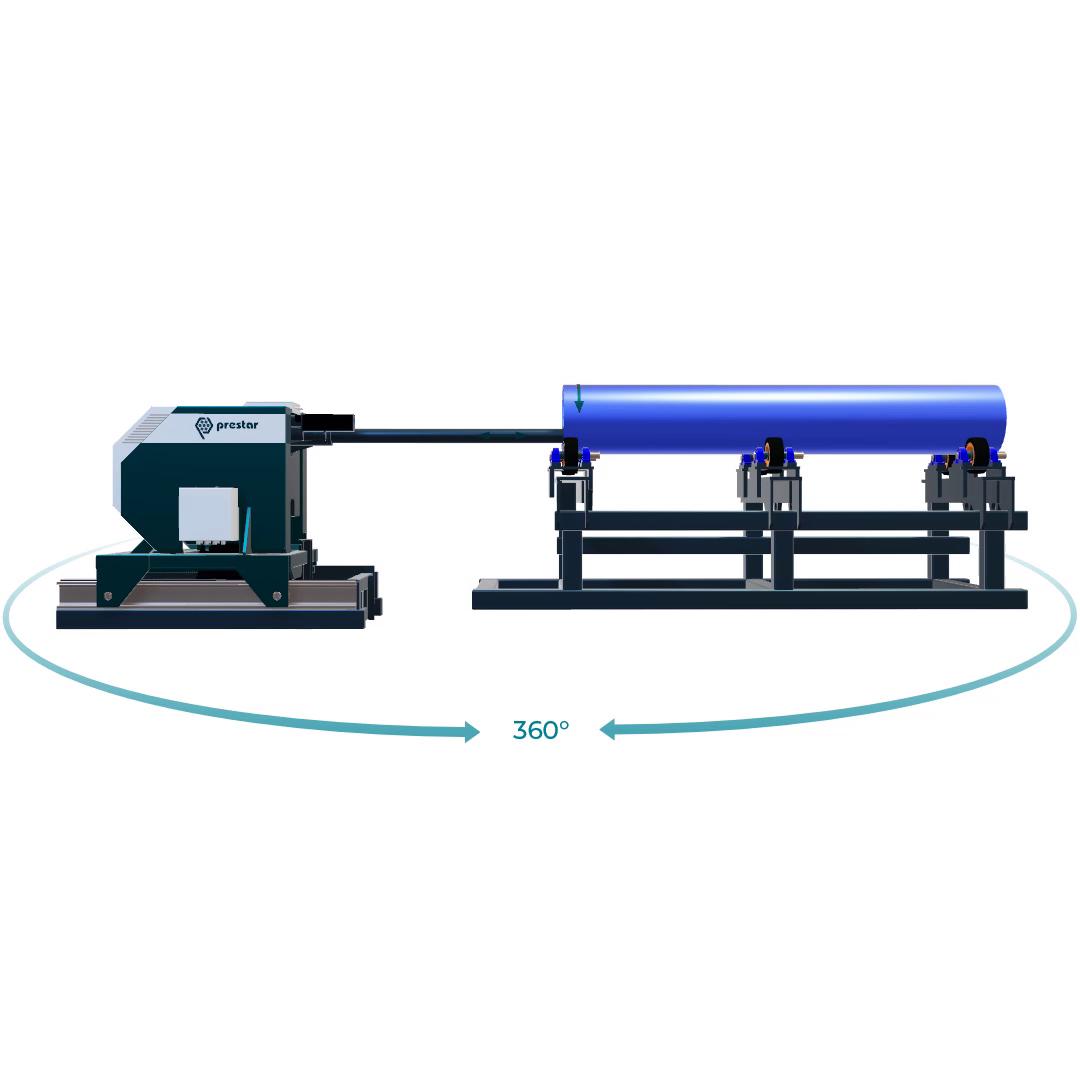
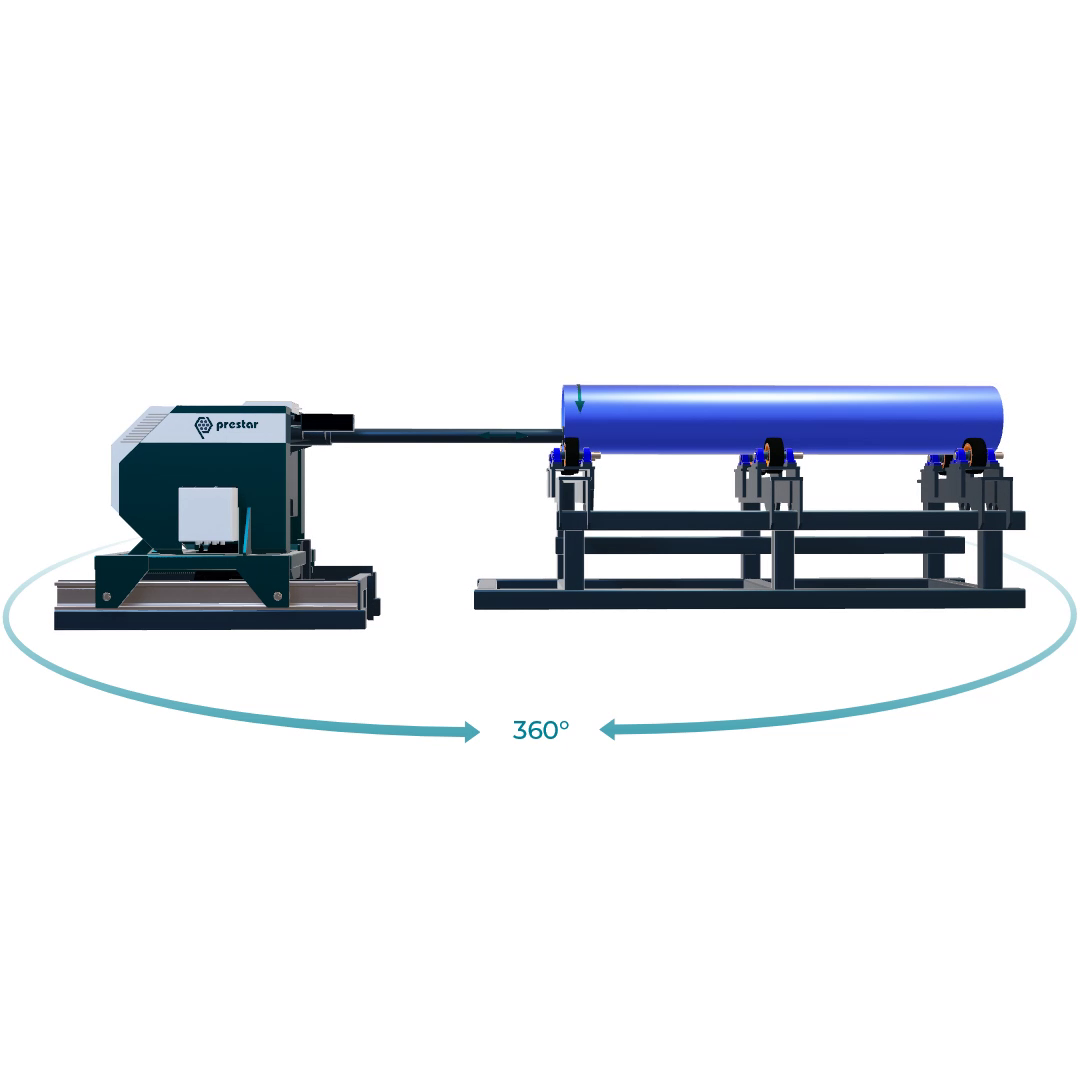
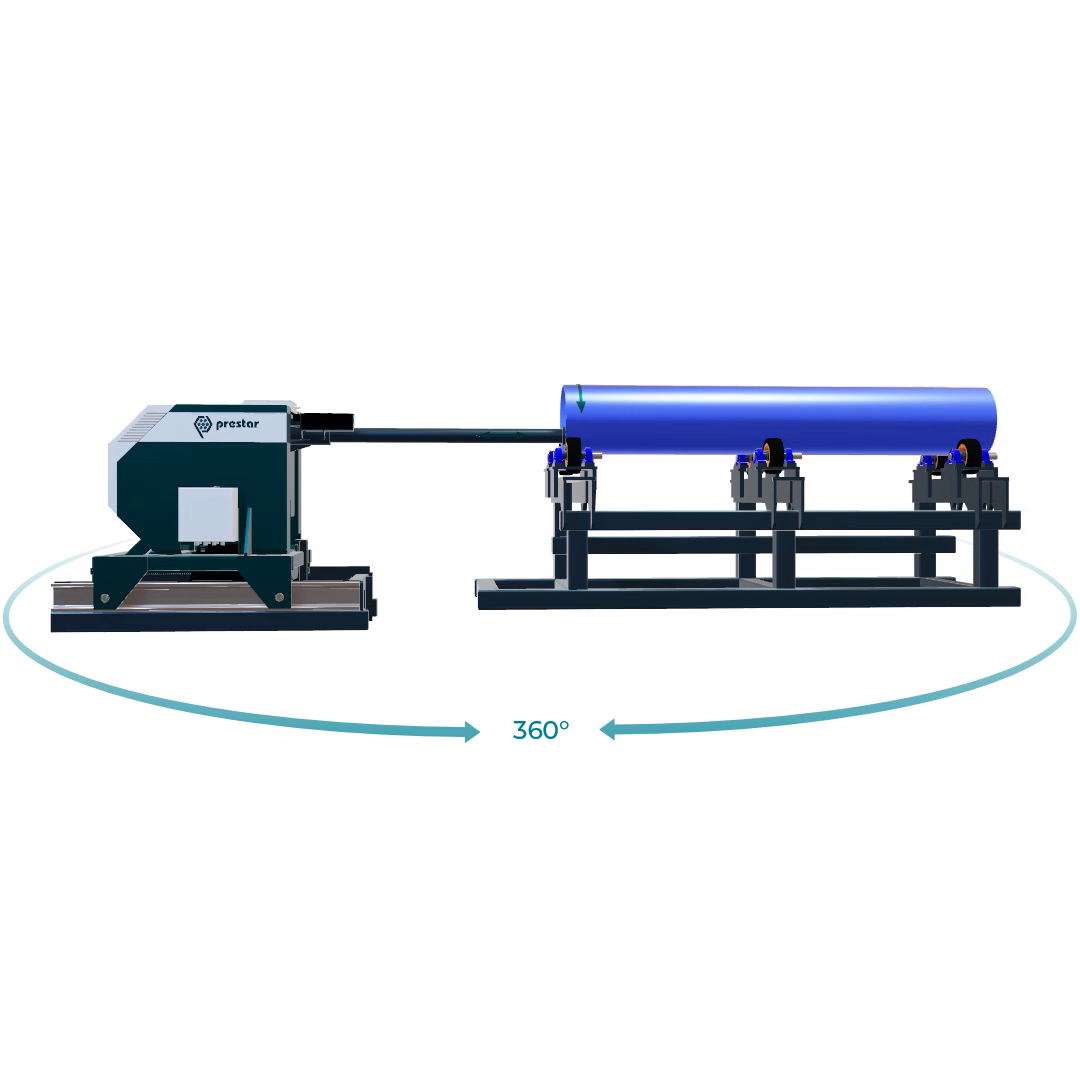
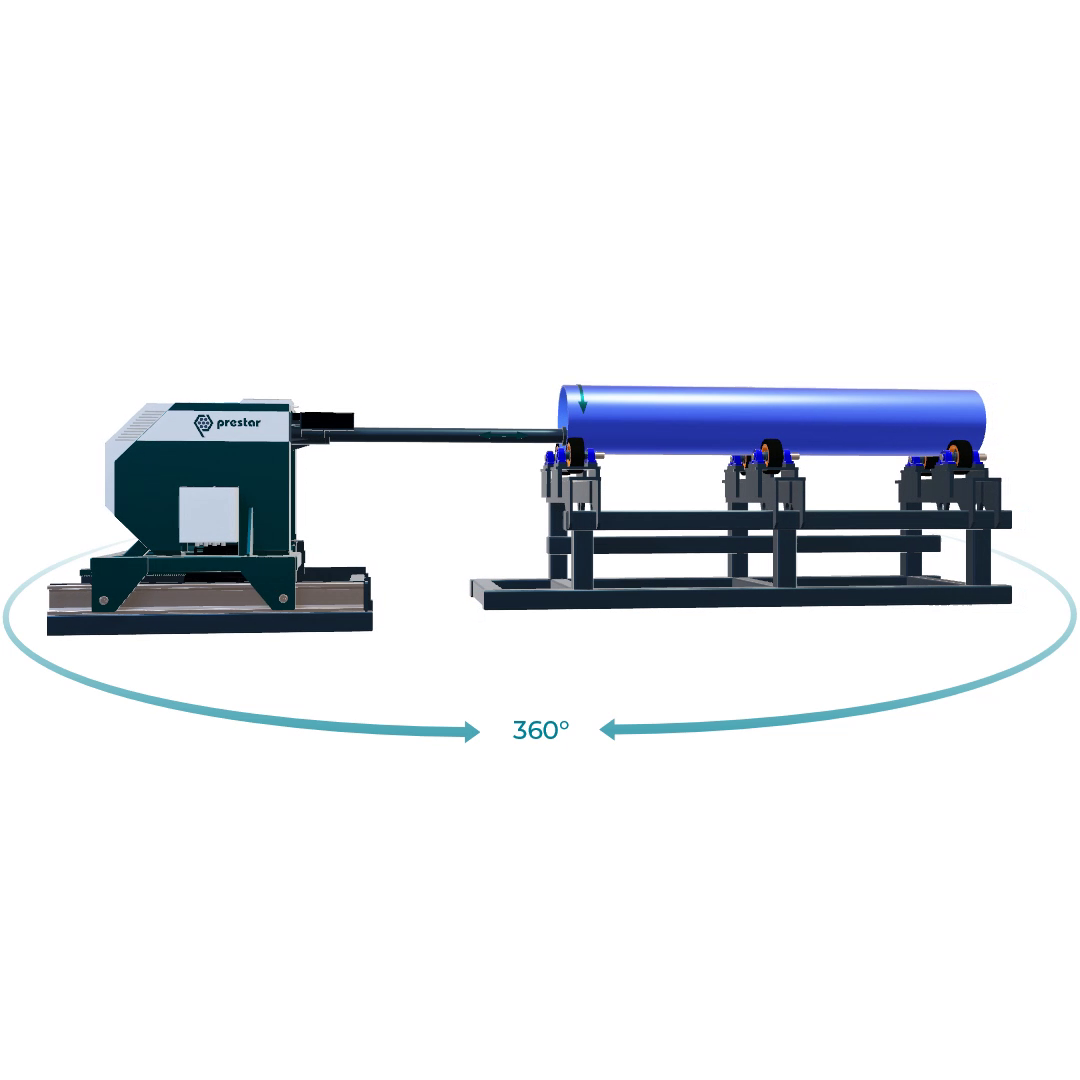
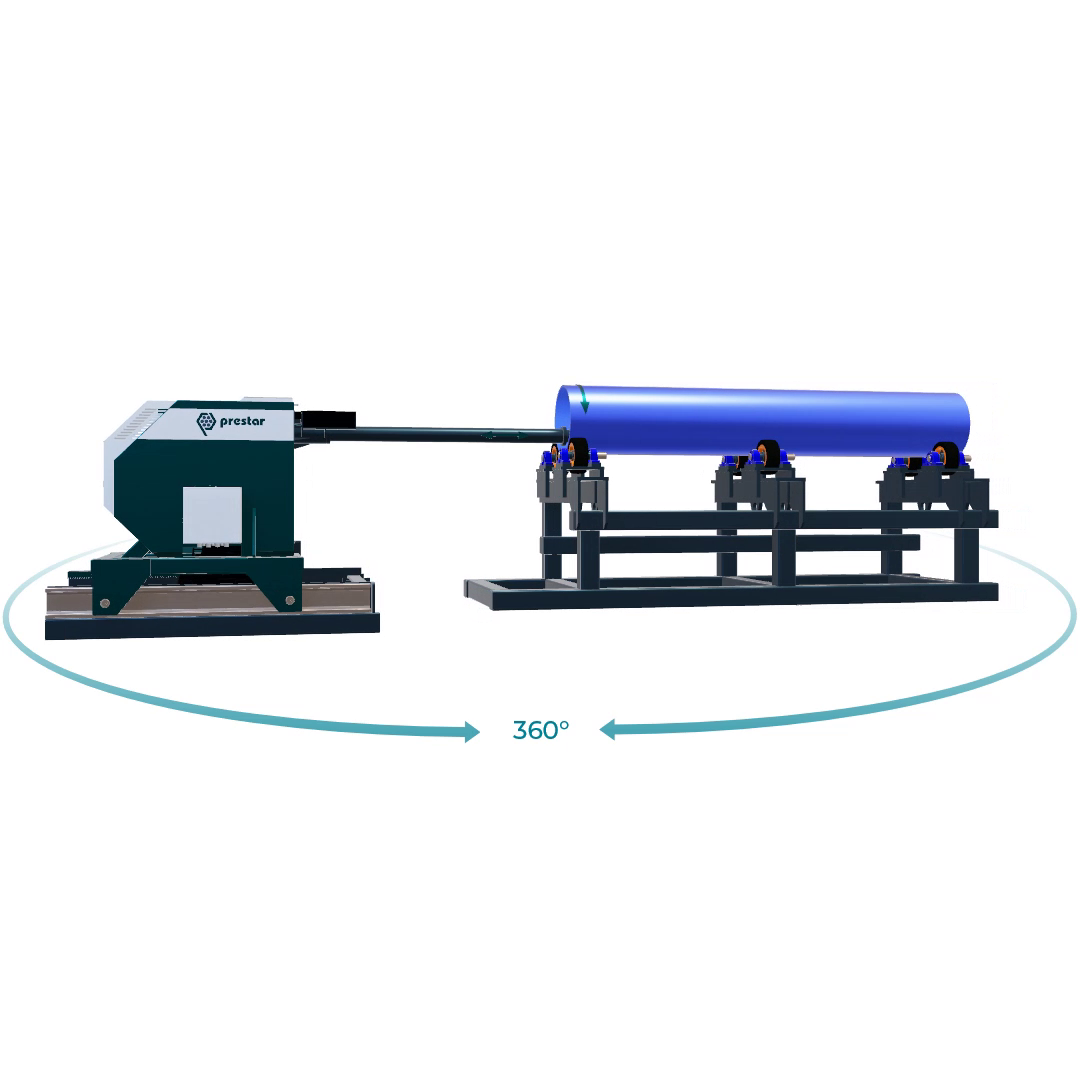
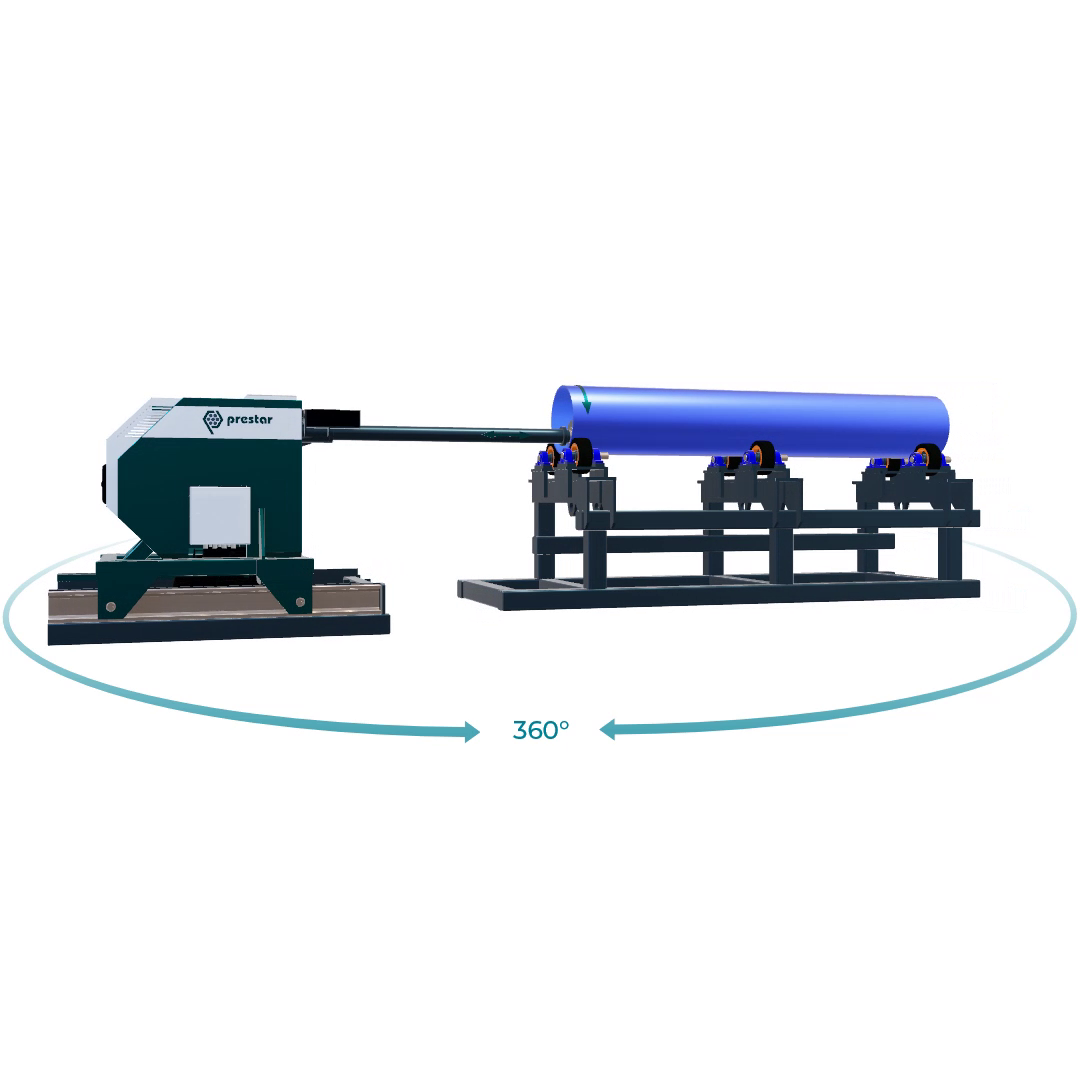
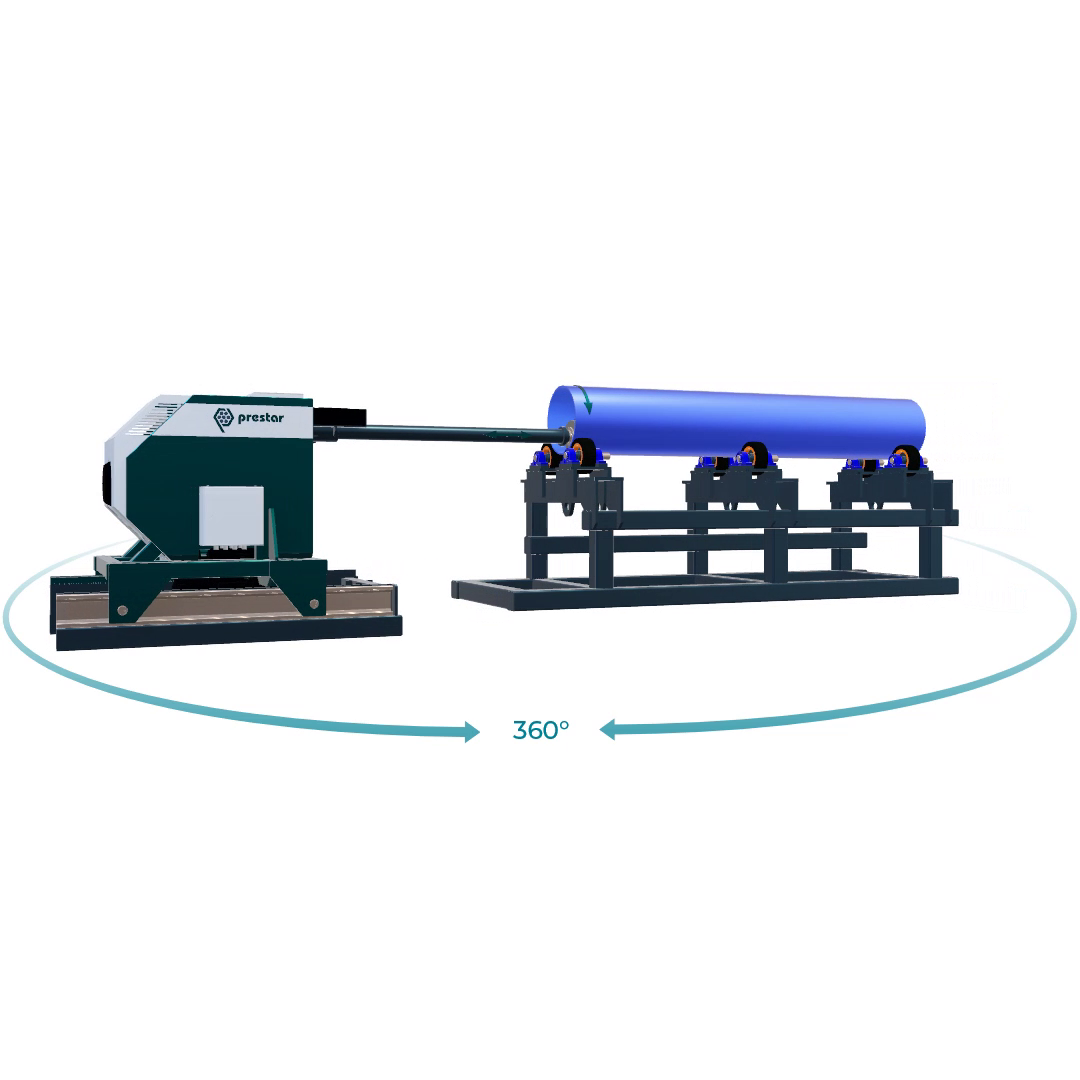
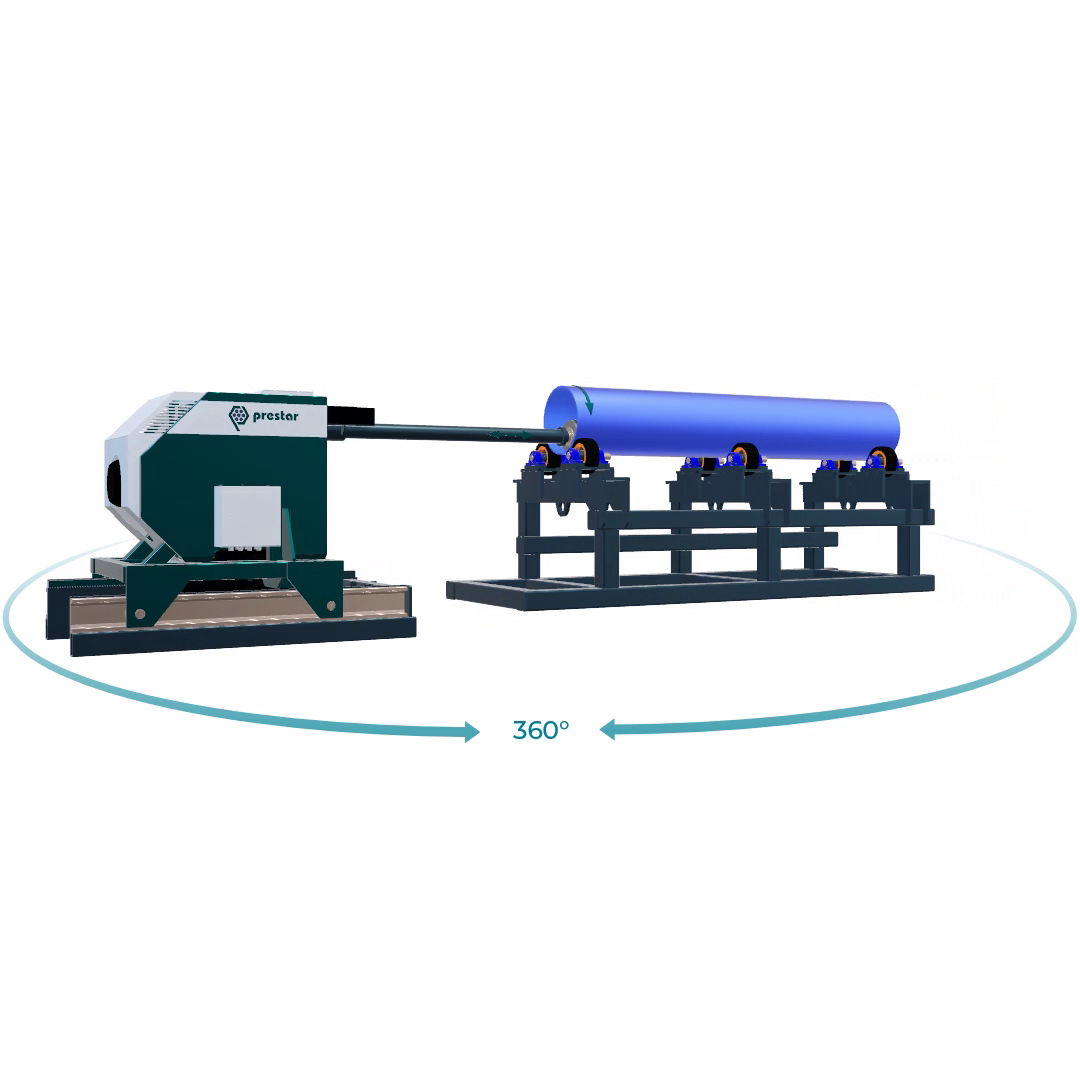
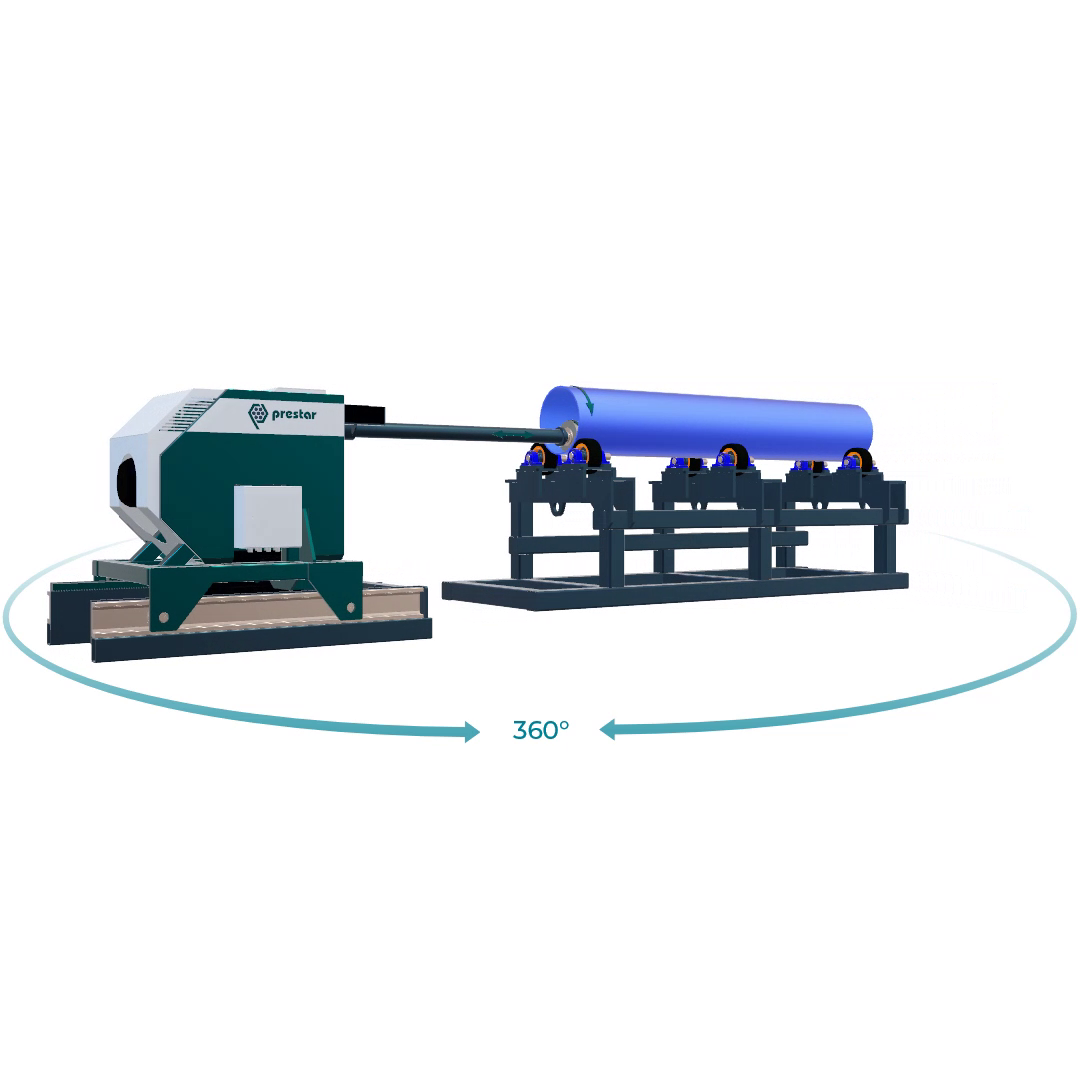
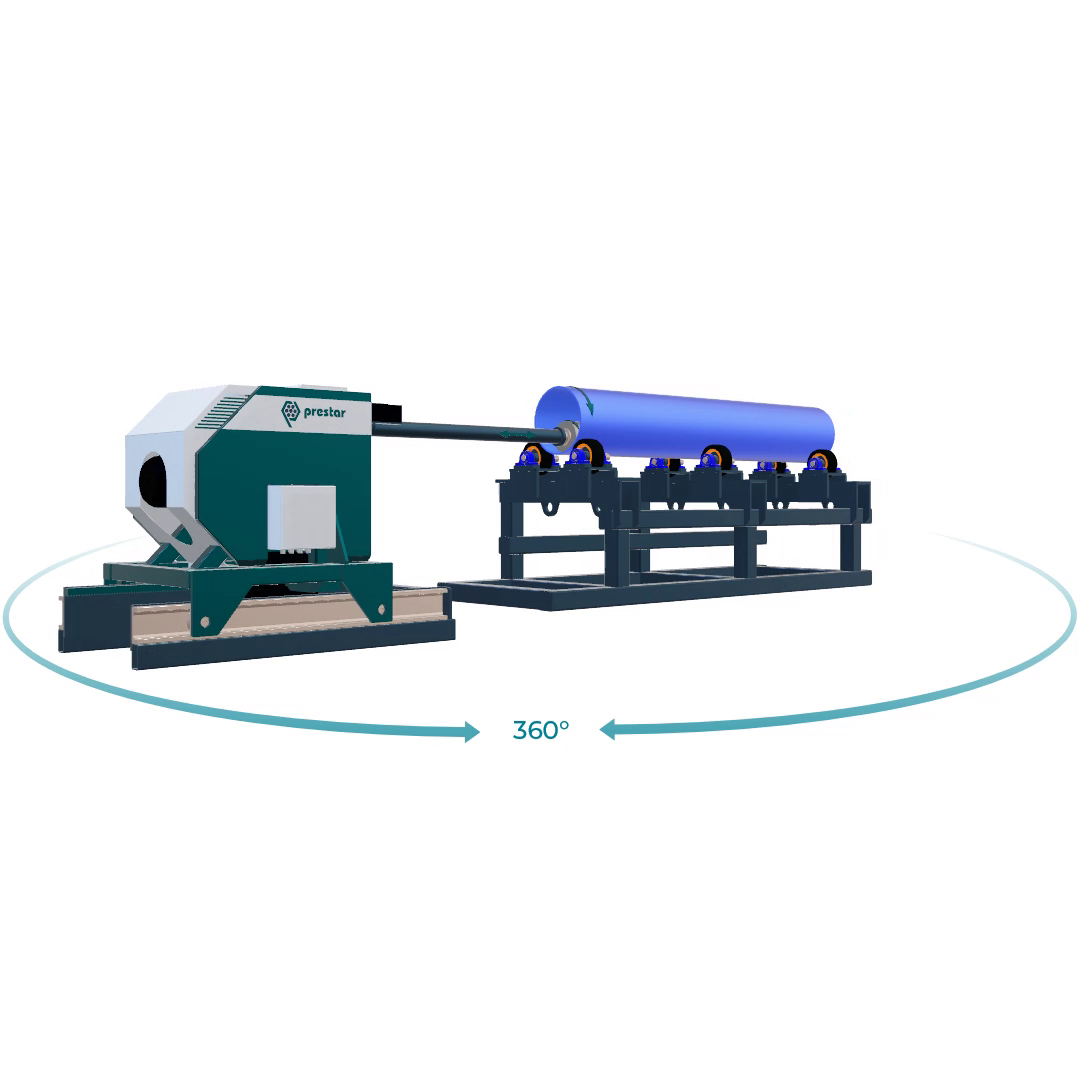
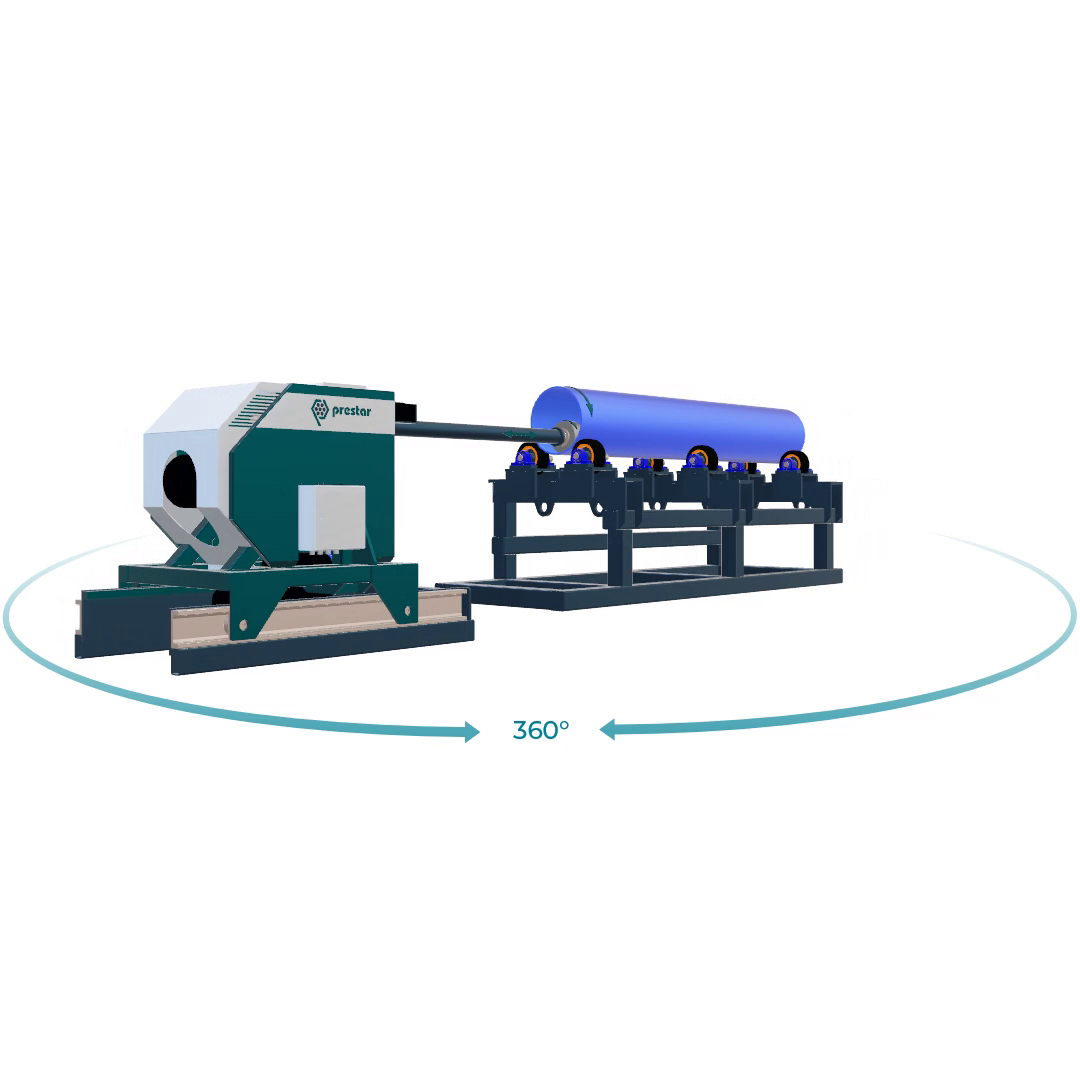
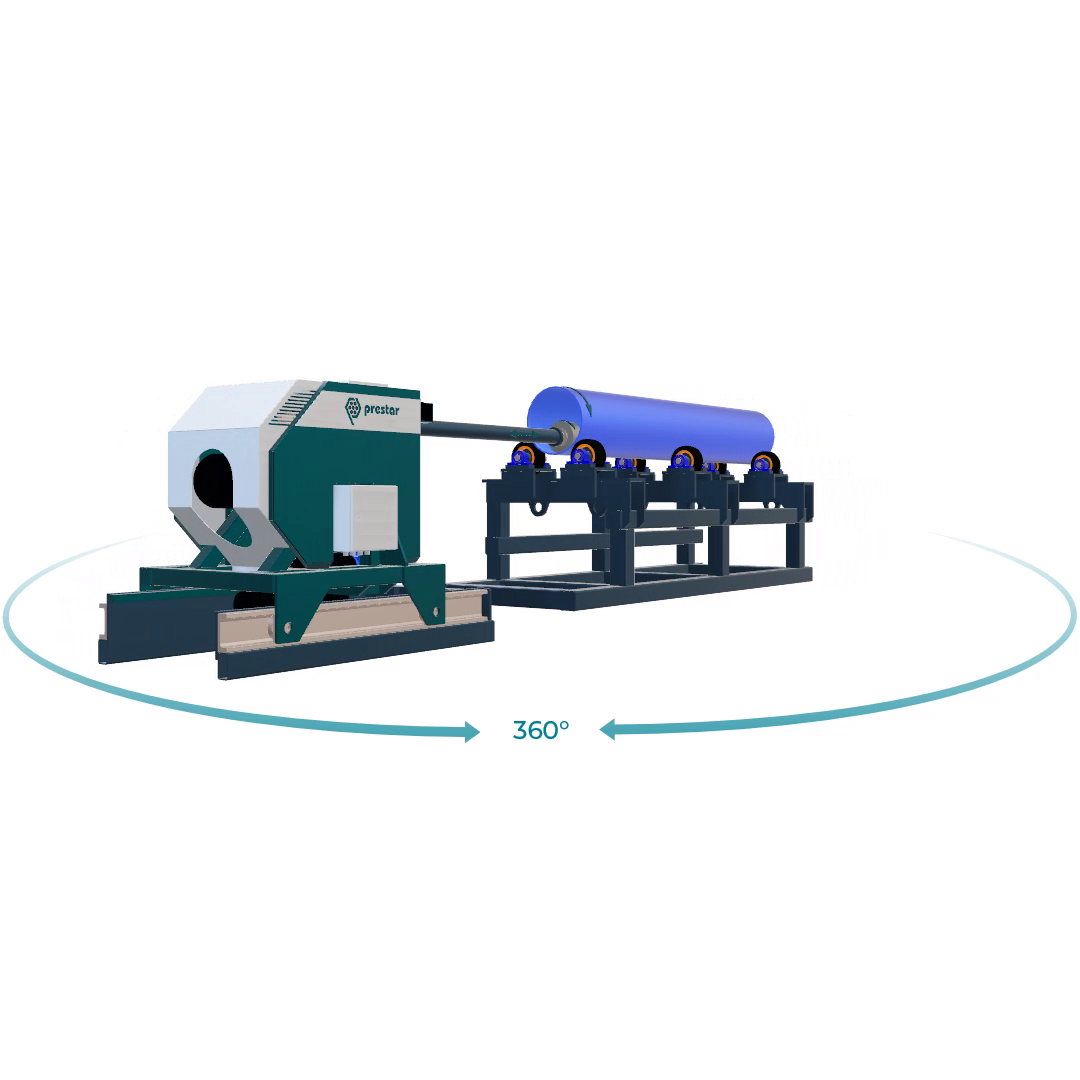
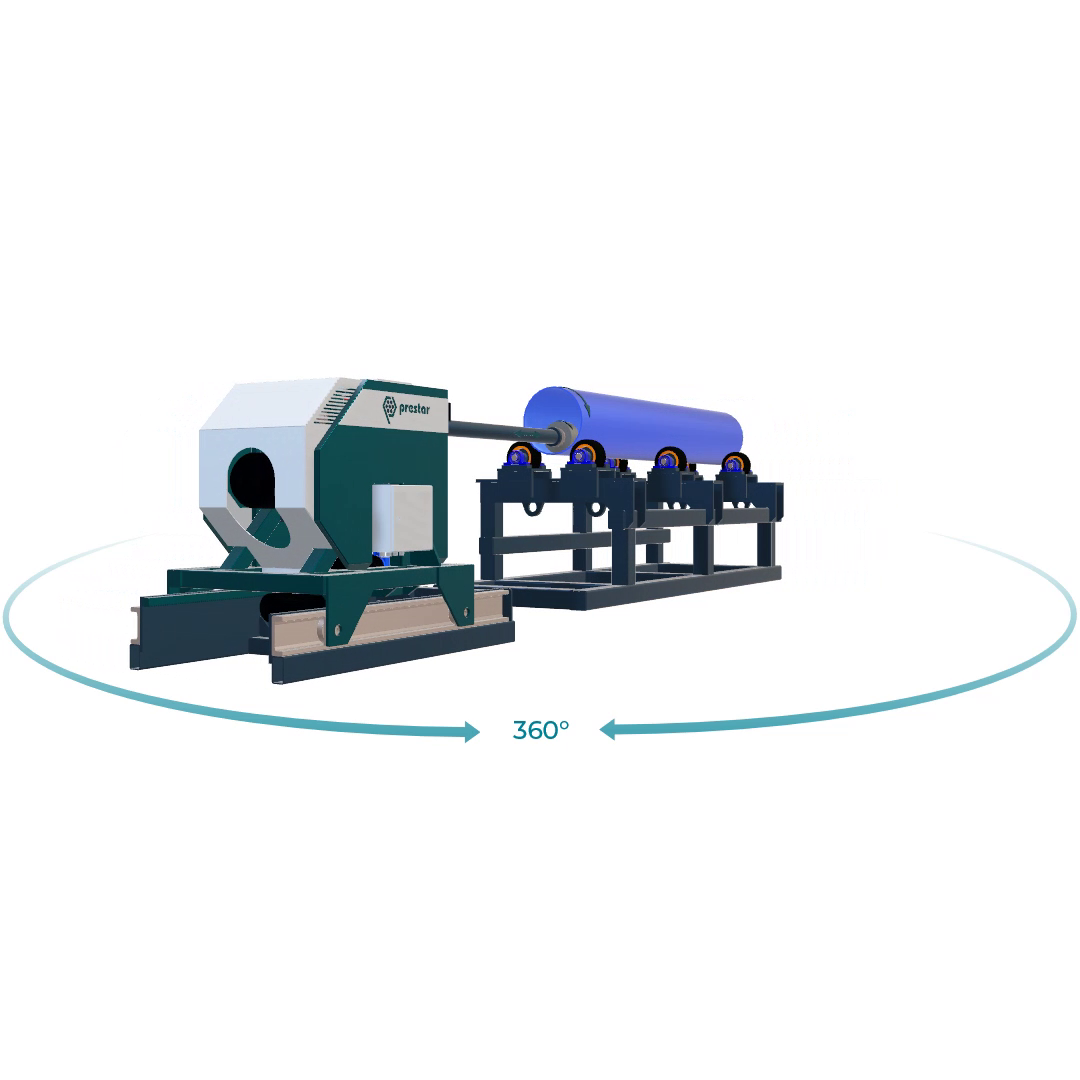
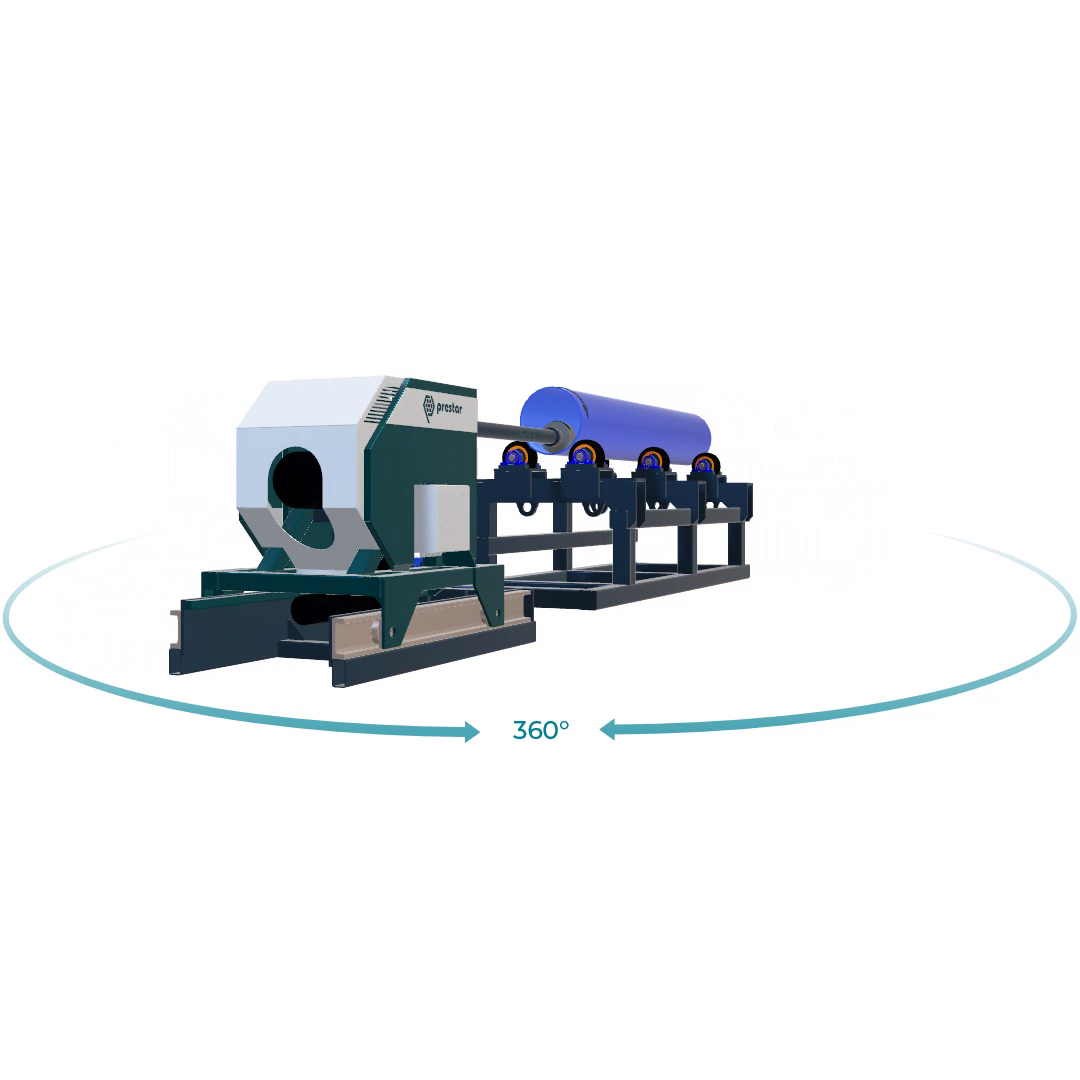
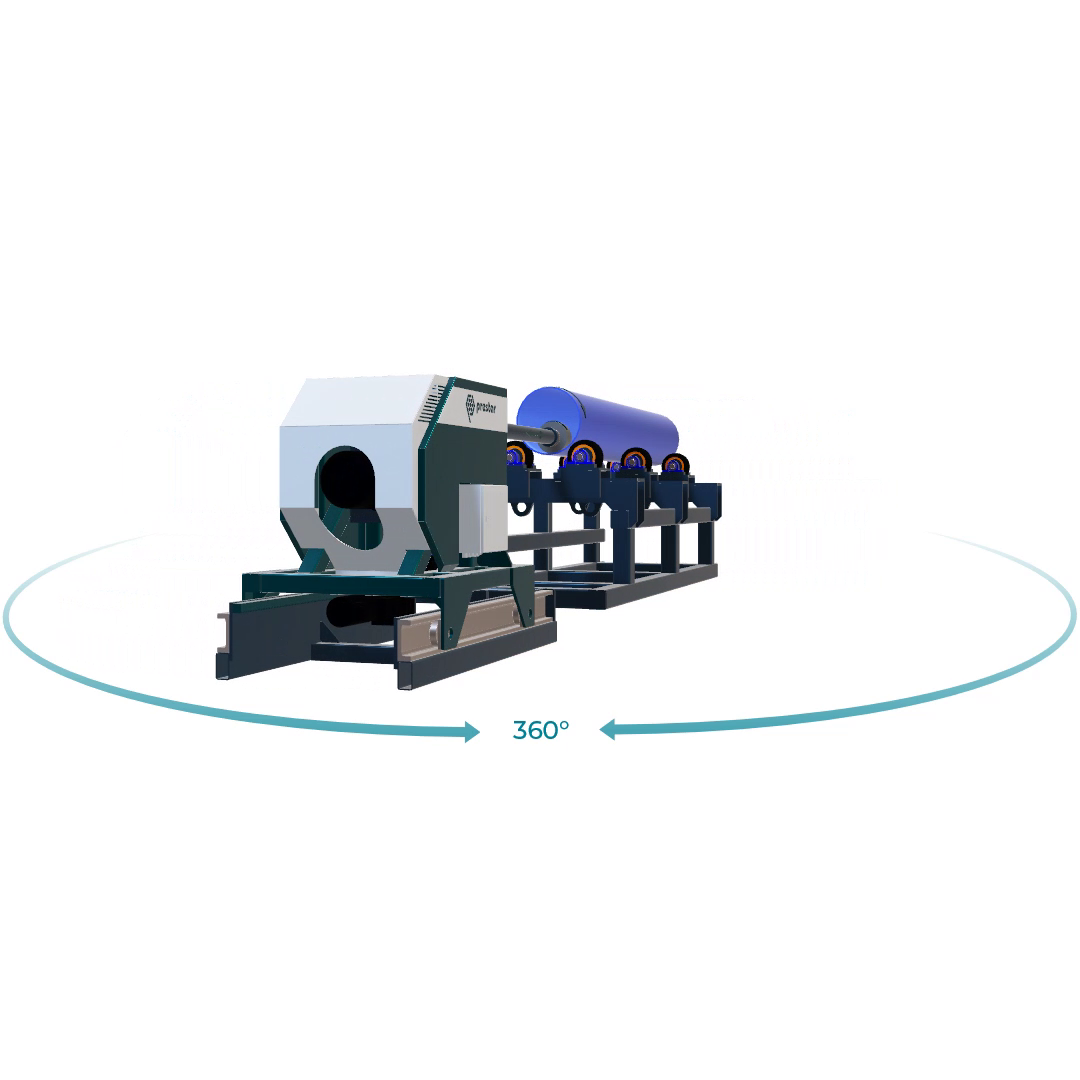
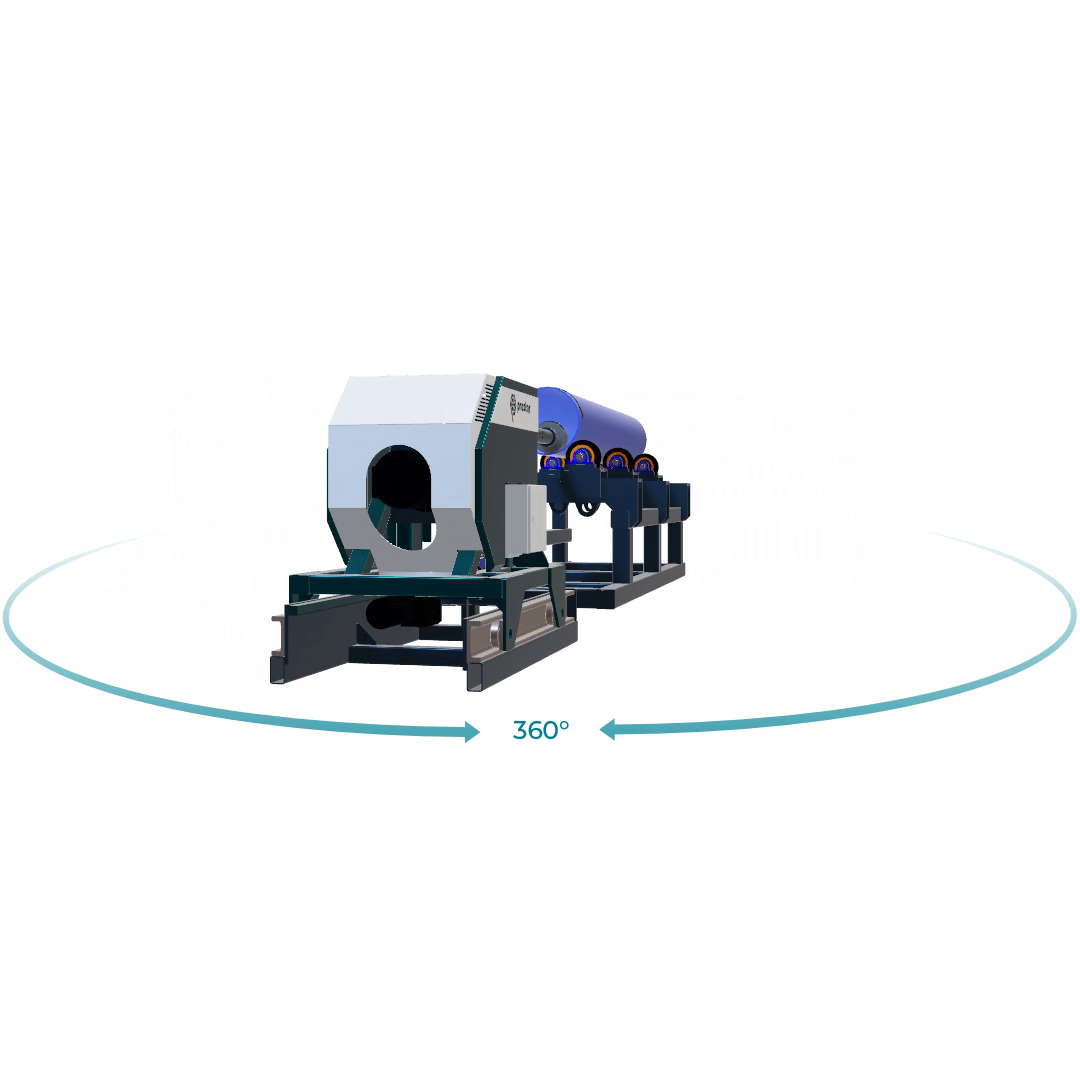
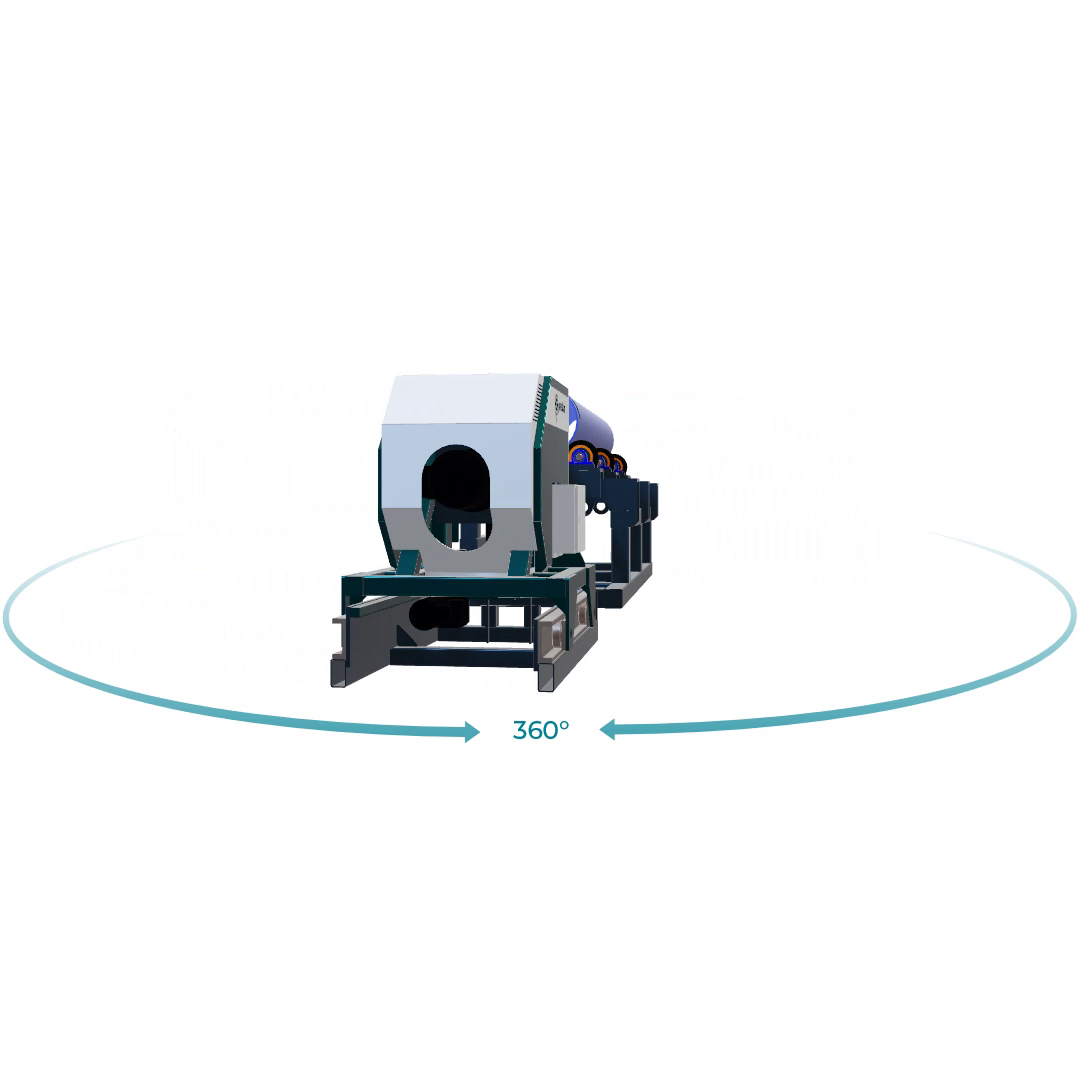

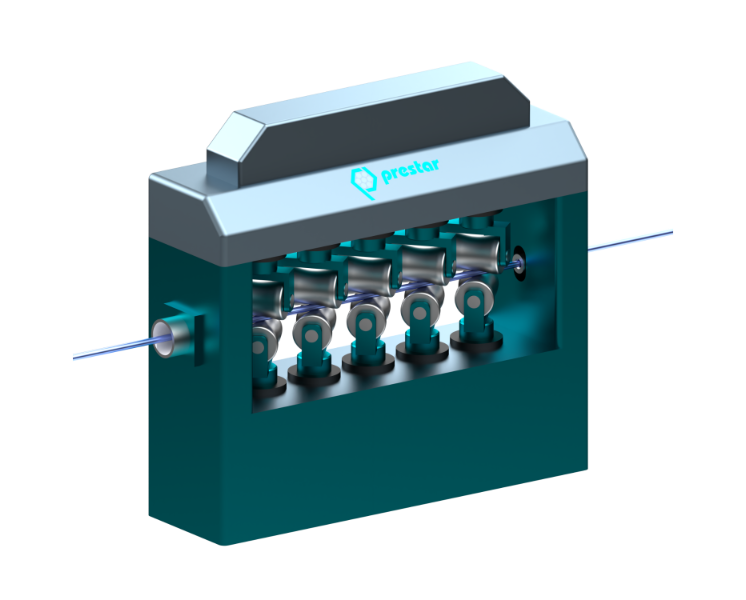
Straightening machines
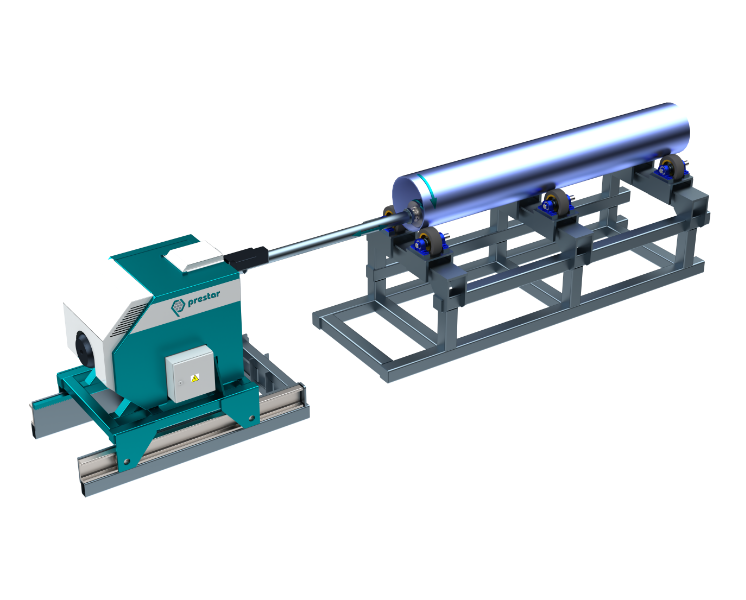
Internal pipe grinder
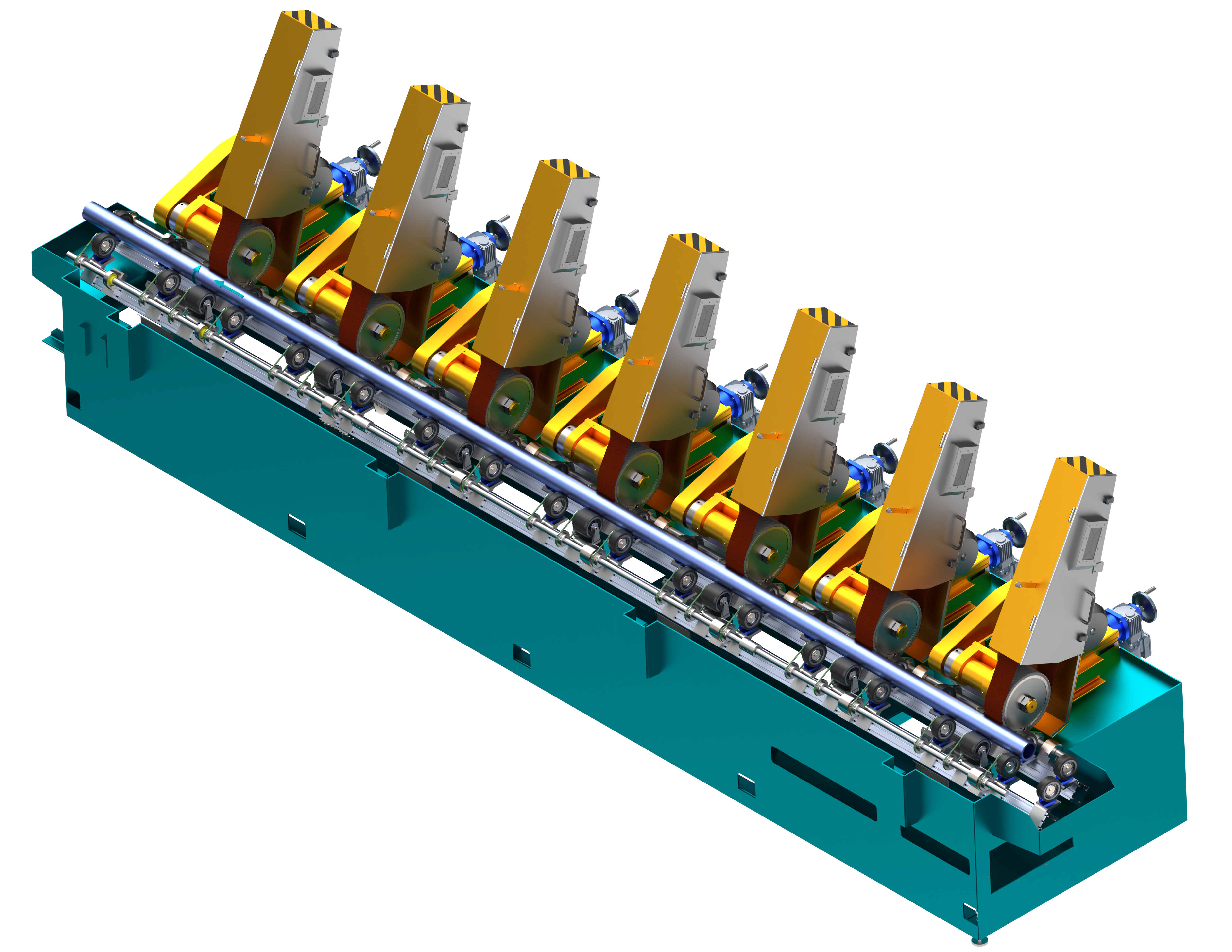
Centerless pipe grinder
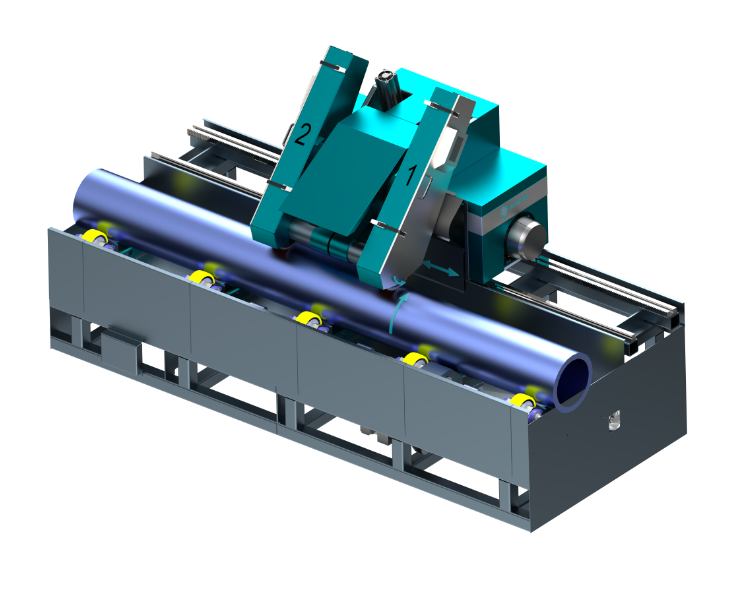
External stationary pipe grinder
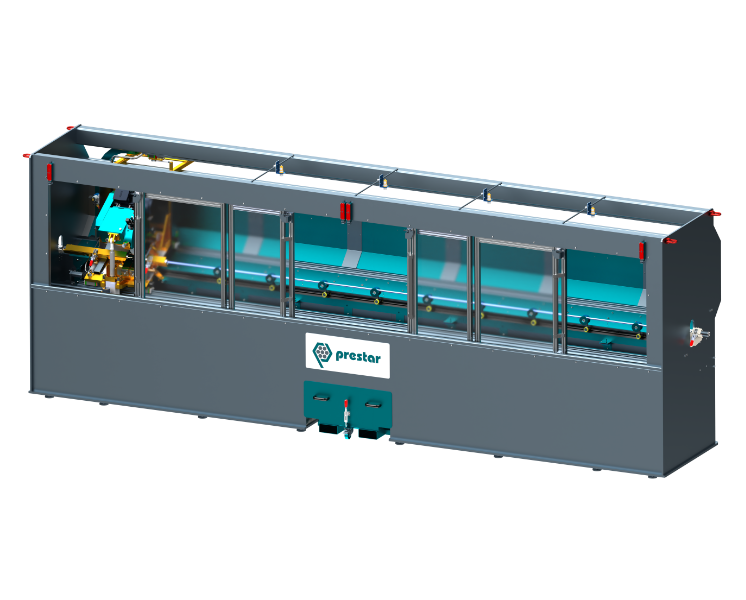
Flying saw
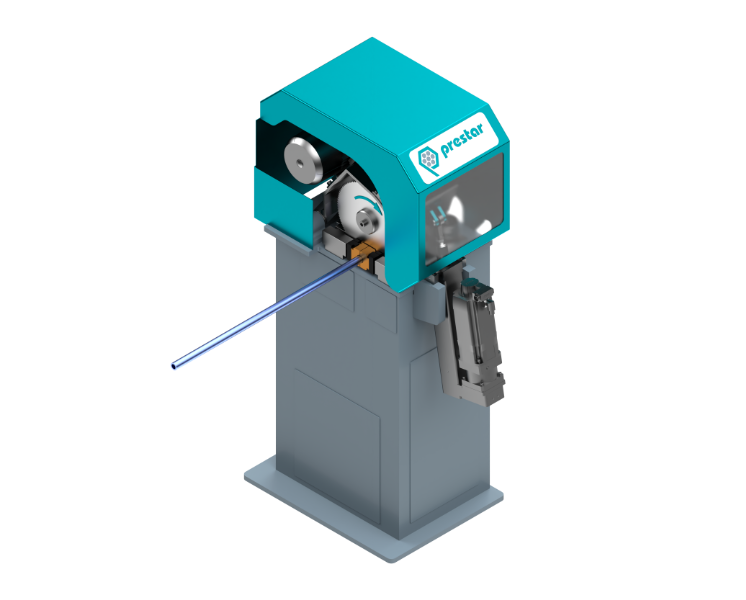
Circular saw
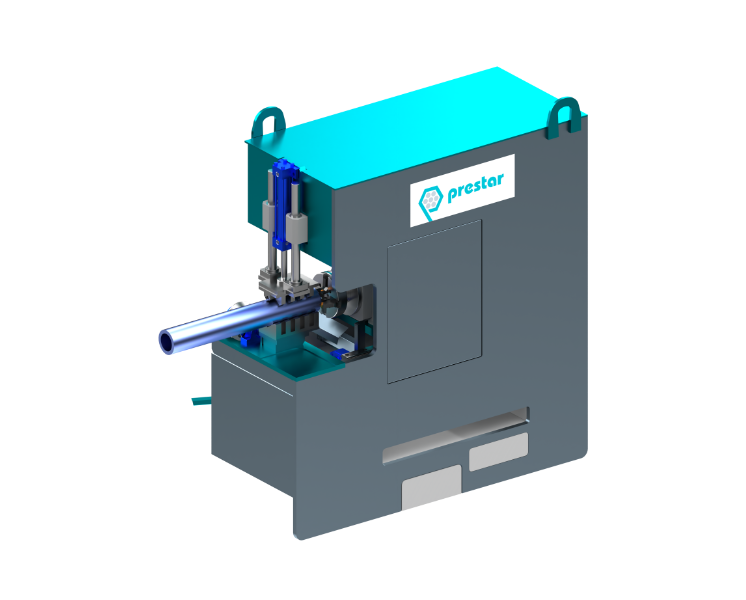
Chamfering of pipes
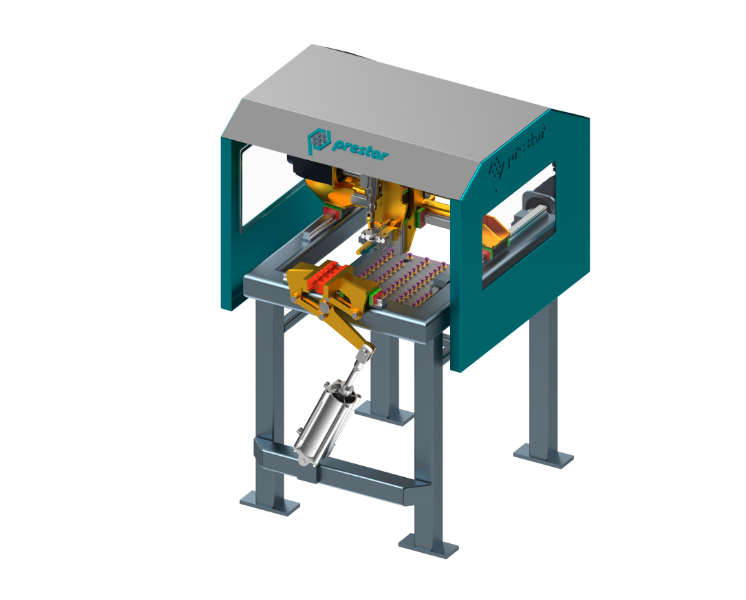
Sorting and plugging
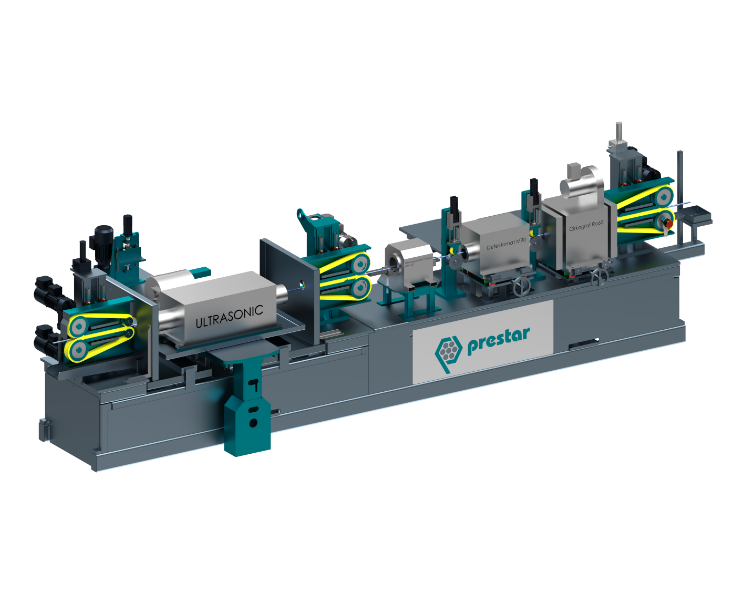
Control tables
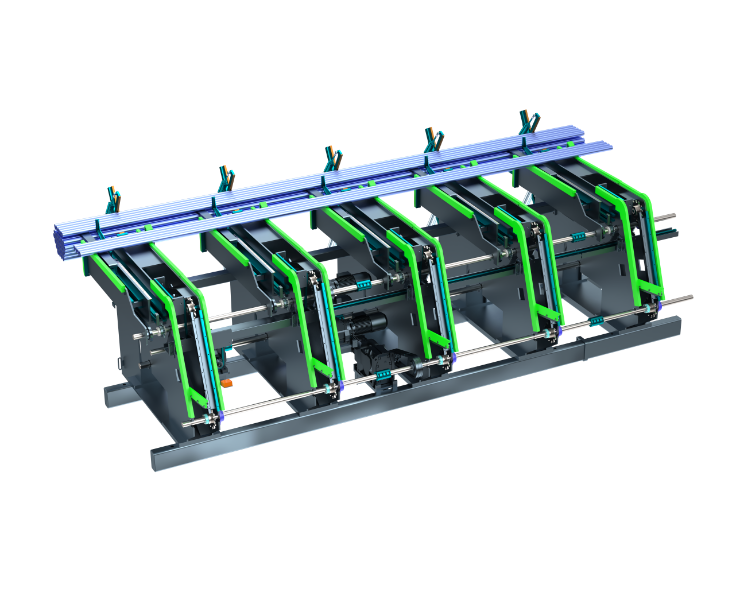
Packaging machines
A new line for pipes or rods will demonstrably make production more efficient